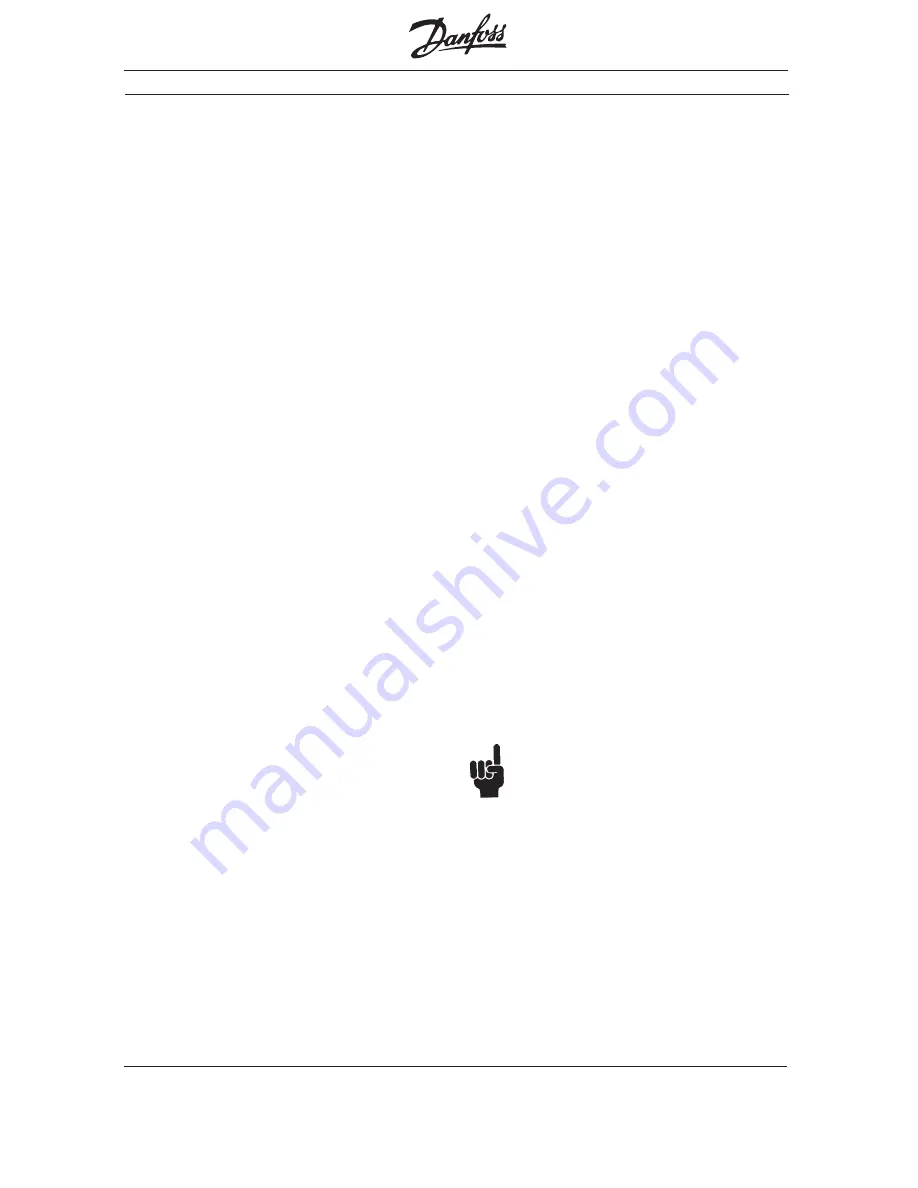
VLT
®
6000 HVAC
13
MG.60.G2.02 - VLT is a registered Danfoss Trademark
Strategy Three
FLN Function
FLN Function
FLN Function
FLN Function
FLN Function – Monitor drive operation
– Monitor drive operation
– Monitor drive operation
– Monitor drive operation
– Monitor drive operation
VL
VL
VL
VL
VLT 6000 Contr
T 6000 Contr
T 6000 Contr
T 6000 Contr
T 6000 Control
ol
ol
ol
ol – From a hard-wired
system, including system feedback
VL
VL
VL
VL
VLT 6000 Mode
T 6000 Mode
T 6000 Mode
T 6000 Mode
T 6000 Mode – Closed Loop
The VLT 6000 follows hard-wired run/stop
signals.The drive uses its internal PID
controller to control motor speed. The
feedback signal is hard wired to the VLT 6000
analog input and the setpoint is programmed
into the drive. The FLN is used to monitor the
status of the drive and the value of the
VLT 6000 PID controller setpoint and
feedback.
Network Inputs to the VL
Network Inputs to the VL
Network Inputs to the VL
Network Inputs to the VL
Network Inputs to the VLT 6000:
T 6000:
T 6000:
T 6000:
T 6000: Because the
FLN is simply monitoring the operation of the drive, it
provides no inputs.
Network Outputs fr
Network Outputs fr
Network Outputs fr
Network Outputs fr
Network Outputs from the VL
om the VL
om the VL
om the VL
om the VLT 6000:
T 6000:
T 6000:
T 6000:
T 6000: In addition
to the points listed in Strategy One, it may be useful
to monitor the following points related to the
operation of the VLT 6000 PID controller.
Feedback:
Feedback:
Feedback:
Feedback:
Feedback:
6 0
6 0
6 0
6 0
6 0
INPUT REF
INPUT REF
INPUT REF
INPUT REF
INPUT REF – This is the setpoint for the
VLT 6000 PID controller in units defined in
parameter 415,
Units Relating to Closed Loop
.
6 2
6 2
6 2
6 2
6 2
PI FEEDBACK
PI FEEDBACK
PI FEEDBACK
PI FEEDBACK
PI FEEDBACK – This is the value of the
feedback signal for the VLT 6000 PID controller
in the units defined in parameter 415.
Strategy Four
FLN Function
FLN Function
FLN Function
FLN Function
FLN Function – Provide the drive with
setpoint and feedback values using the VLT
6000 PID controller to determine motor speed
VL
VL
VL
VL
VLT 6000 Contr
T 6000 Contr
T 6000 Contr
T 6000 Contr
T 6000 Control
ol
ol
ol
ol – From the FLN
VL
VL
VL
VL
VLT 6000 Mode
T 6000 Mode
T 6000 Mode
T 6000 Mode
T 6000 Mode – Closed Loop
The VLT 6000 follows run/stop signals from the FLN.
The FLN receives the feedback signal from the
controlled system. It sends this and the desired
setpoint to the VLT 6000 PID controller. The drive
compares the feedback signal with the setpoint and
adjusts the speed of the drive accordingly.
Network Inputs to the VL
Network Inputs to the VL
Network Inputs to the VL
Network Inputs to the VL
Network Inputs to the VLT 6000:
T 6000:
T 6000:
T 6000:
T 6000: In addition to
start/stop control, which was discussed in Strate-
gy Two, the FLN provides the drive with feedback
and setpoint information using the following points.
Feedback:
Feedback:
Feedback:
Feedback:
Feedback:
7 1
7 1
7 1
7 1
7 1
FB MIN
FB MIN
FB MIN
FB MIN
FB MIN - The VLT 6000 can display the PID
controller’s setpoint and feedback signal in
units chosen in drive parameter 415,
Units
Relating to Closed Loop
. The value that the
minimum feedback signal represents can be
set using either point 71 or drive parameter
413,
Minimum
Feedback.
7 2
7 2
7 2
7 2
7 2
FB MAX
FB MAX
FB MAX
FB MAX
FB MAX - The VLT 6000 can display the PID
controller’s setpoint and feedback signal in
units chosen in drive parameter 415. The value
that the maximum feedback signal represents
can be set using either point 72 or drive
parameter 414,
Maximum Feedback
.
7 3
7 3
7 3
7 3
7 3
BUS FB 1
BUS FB 1
BUS FB 1
BUS FB 1
BUS FB 1 - A value of 0 represents the
minimum feedback signal, as defined by point
71 or parameter 413. A value of 16383
represents the maximum feedback signal, as
defined by point 72 or parameter 414. This
should be the feedback used if only one
feedback signal is supplied to the drive.
NOTE:
NOTE:
NOTE:
NOTE:
NOTE:
If drive terminal 53 is programmed in
parameter 308,
Analog Inputs
, for feedback,
any signal applied to terminal 53 is added to value
provided at point 73. Therefore, it is generally
advisable not to program parameter 308 for
feedback.
74 BUS FB 2
74 BUS FB 2
74 BUS FB 2
74 BUS FB 2
74 BUS FB 2 - This is used when two feedback
signals are supplied to the drive PID
controller. VLT 6000 parameter 417,
Feedback Function
, determines the the
function that the drive applies to these
signals. Functions include minimum,
maximum, sum, difference, and average. A
value of 0 represents the minimum
feedback signal, as defined by point 71 or
Network Outputs fr
Network Outputs fr
Network Outputs fr
Network Outputs fr
Network Outputs from the VL
om the VL
om the VL
om the VL
om the VLT 6000:
T 6000:
T 6000:
T 6000:
T 6000:
The points listed in Strategy One are commonly used.