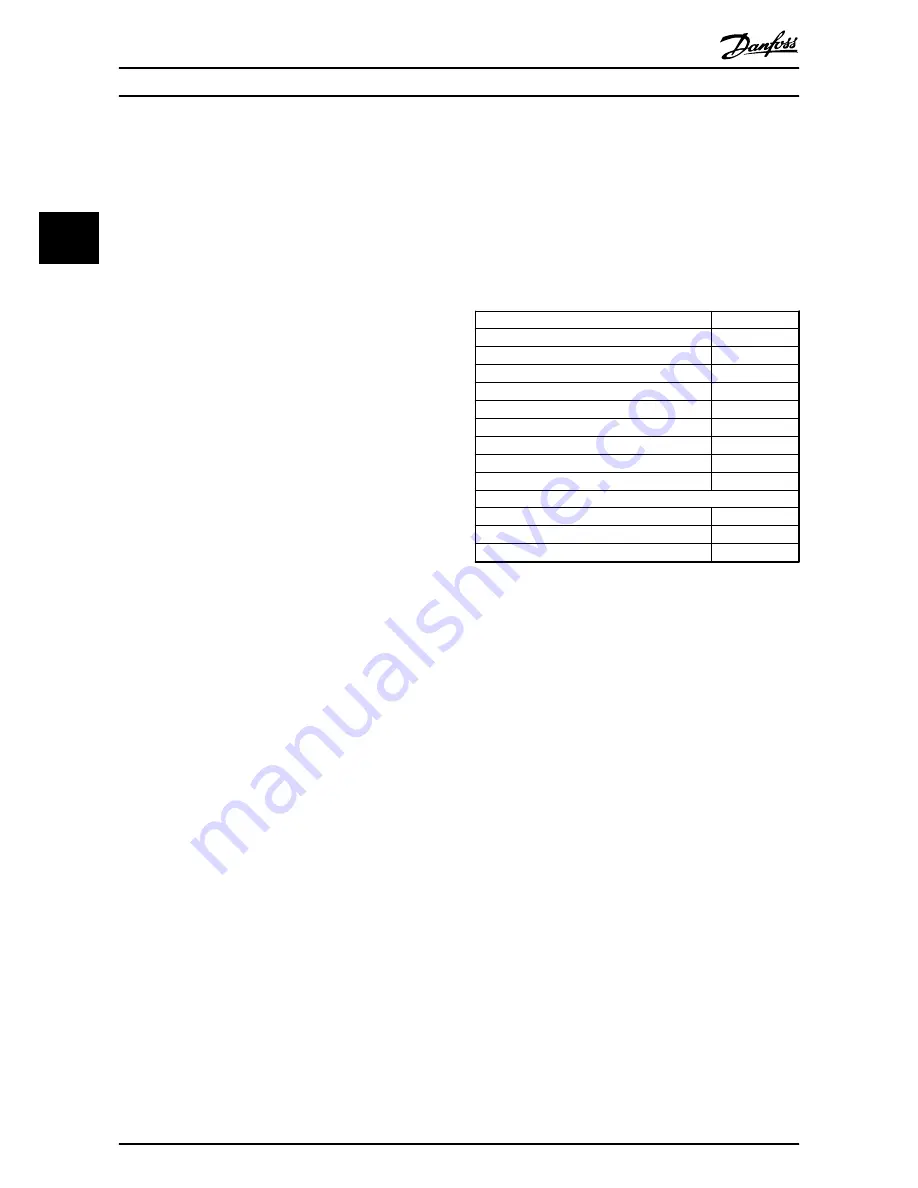
3.3 Commissioning Guide
This guideline is only describing basic configuration and
optimizing of MCO 305, before starting the following steps
must be completed.
1.
Basic commissioning of VLT AutomationDrive.
NOTE
VLT AutomationDrive must be optimized and have good
control over the motor and application before commis-
sioning MCO 305. Guidelines can be found in
VLT
AutomationDrive Operating Instructions (MG.33.AX.XX)
.
2.
Install the PC software tools (MCT 10 Set-up
Software)
3.
Establish communication between PC and VLT
AutomationDrive using USB, RS-485 or PROFIBUS
DPV1.
Then follow these steps to set-up and optimize MCO 305.
1.
Setting of basic MCO 305 parameters (groups 32-
** and 33-**).
2.
Connect and test encoder(s).
3.
Optimize PID controller.
NOTE
Error 113 will show up right after power up if the VLT
AutomationDrive is not ready. The VLT AutomationDrive is
in the “Not ready” state when
-
it has an alarm (trip),
-
it is in hand mode, [Hand on] key,
-
local LCP stop is activated, [OFF] key,
-
there is no signal on input 37 safe stop (only FC
302).
Error 113 can only be reset using the ERRCLR command or
with BREAK [Esc] in the PC software and only when the
VLT AutomationDrive is in the “ready” state, which means
none of the above may be true. The VLT AutomationDrive
monitoring function can be switched off by selecting [0] in
33-82 Drive Status Monitoring
.
Read the Safety Instructions before installing the frequency
converter.
3.4 Basic MCO Parameter Settings
The following parameters must always be checked and if
necessary adjusted. Depending on the requirements of the
application it might be necessary to adjust other
parameters as well.
For the other parameters, use the default settings at first
and then optimize the controller as needed at a later point
in time with a
Testrun
.
The MCT 10 Set-up Software will support you to set the
parameters in LCP. For a detailed description of all
parameters, please refer to
8 Appendix
.
3.4.1 Setting of Encoder Parameters
Define the used type of feedback encoder in parameter
group 32-0*.
These defaults are set:
32-0* Encoder 2 - Feedback
Default
32-00 Incremental Signal Type
[1] RS422
32-01 Incremental Resolution
1024
32-02 Absolute Protocol
[0] None
32-03 Absolute Resolution
8192
32-05 Absolute Encoder Data Length
25
32-06 Absolute Encoder Clock Frequency
262000
32-07 Absolute Encoder Clock Generation
[1] On
32-08 Absolute Encoder Cable Length
0
32-09 Encoder Monitoring
[0] Off
For CAN Encoders
32-14 Enc.2 node ID
127
32-15 Enc.2 CAN guard
[0] Off
33-91 X62 MCO CAN baud rate
[20] 125 kbps
3.4.2 Setting of parameters for CANopen
feedback encoder
-
In
32-00 Incremental Signal Type
select the setting
[3] “CAN encoder”.
-
In
32-01 Incremental Resolution
set the resolution
of the encoder.
-
In
32-14 Enc.2 node ID
set the CAN ID of the
encoder.
-
In
32-15 Enc.2 CAN guard
activate or deactivate
the guarding.
-
In
33-91 X62 MCO CAN baud rate
set in the CAN
bus baud rate.
The following parameters are only relevant for synchro-
nizing applications when a master encoder signal is used.
These defaults are set:
How to Install
MCO 305 Operating Instructions
14
MG.33.K3.02 - VLT
®
is a registered Danfoss trademark
3
3