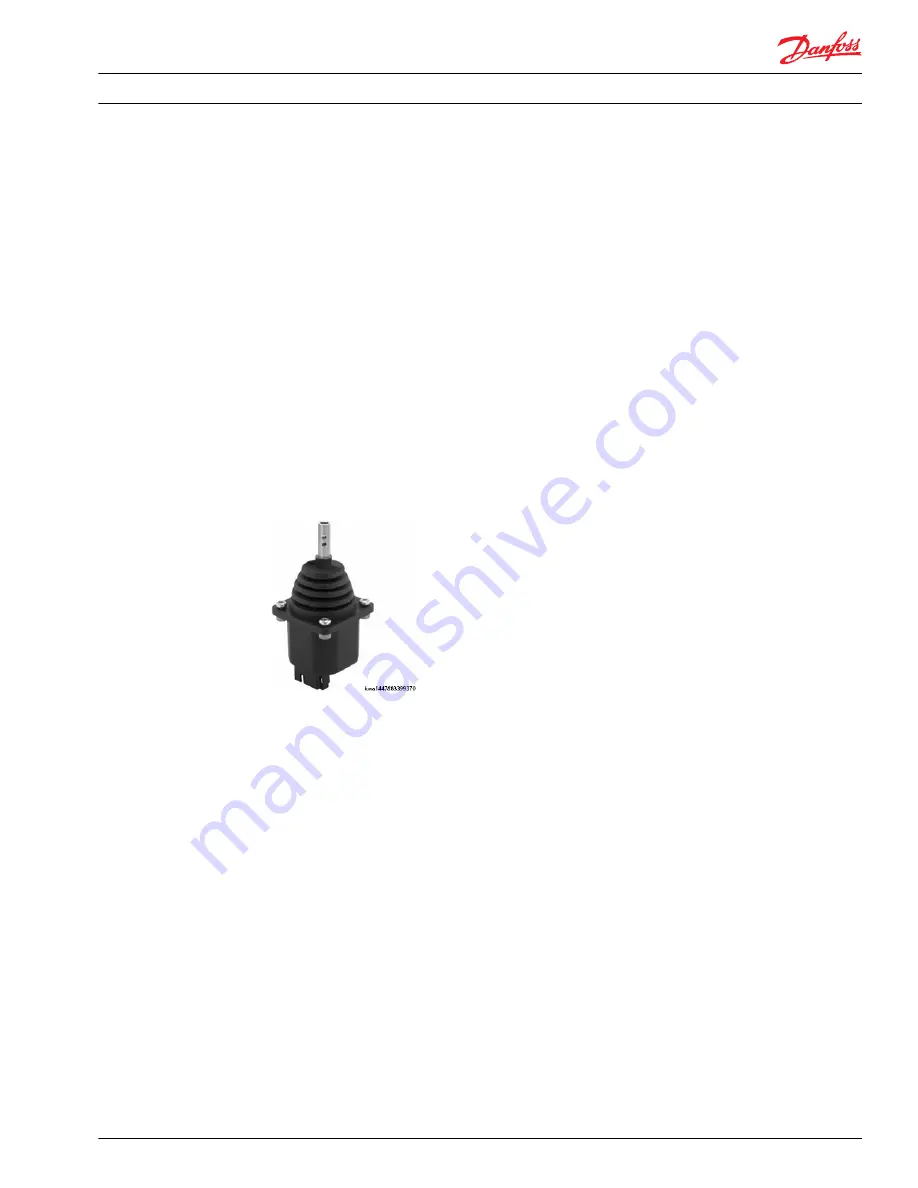
Overview
The JS6000 Joystick Base has been specially developed to meet the harsh operating requirements of
today’s mobile machines. The JS6000 features metal construction with a large diameter stainless steel
operating shaft, an innovative ball and socket gimbal design manufactured from pressure die cast zinc
alloys, a custom high strength material for the center return cone, and optional contactless Hall effect
sensing technology.
The CAN+ version of the JS6000 base allows the value and state of up to eleven digital or seven digital
and four analog inputs from external-to-the-joystick sources to be broadcast along with joystick
Controller Area network (CAN) messages.
The Pulse Width Modulation (PWM) version of the JS6000 base can be used to directly drive a valve, such
as the H1 hydrostatic transmission, without an intermediate microcontroller. This version allows joystick
operating parameters (e.g. ramp rates, button function assignments, output characteristics) to be
configured using the PLUS+1
®
Service Tool interface. Refer to
JS6000 PWM User Manual
, 11060942 for
instructions and information required to configure JS6000 PWM joystick options.
The flexible design of the JS6000 offers many options, making it the right choice for applications that
require more than a simple dual axis joystick with spring return to center.
JS6000 joystick base
Features and options
•
Hall effect or potentiometer sensing (model dependent)
•
One or two sensors per axis for redundancy
•
Single or dual axis
•
Mechanical direction switches
•
2 centering spring forces
•
3 available friction-hold options
•
Output options:
‒
Analog
‒
CAN 2.0B, J1939 protocol
‒
CANopen protocol
‒
High current PWM
•
Multiple grip options:
‒
HKN — plain knob
‒
MG — with operator trigger and hand rest
‒
A— configurable ergonomic
‒
Custom designed grips
•
External-to-joystick analog and digital information included in JS6000 CAN+messages
Technical Information
JS6000 Joystick Base
General information
520L0760 • Rev 1102 • November 2015
5