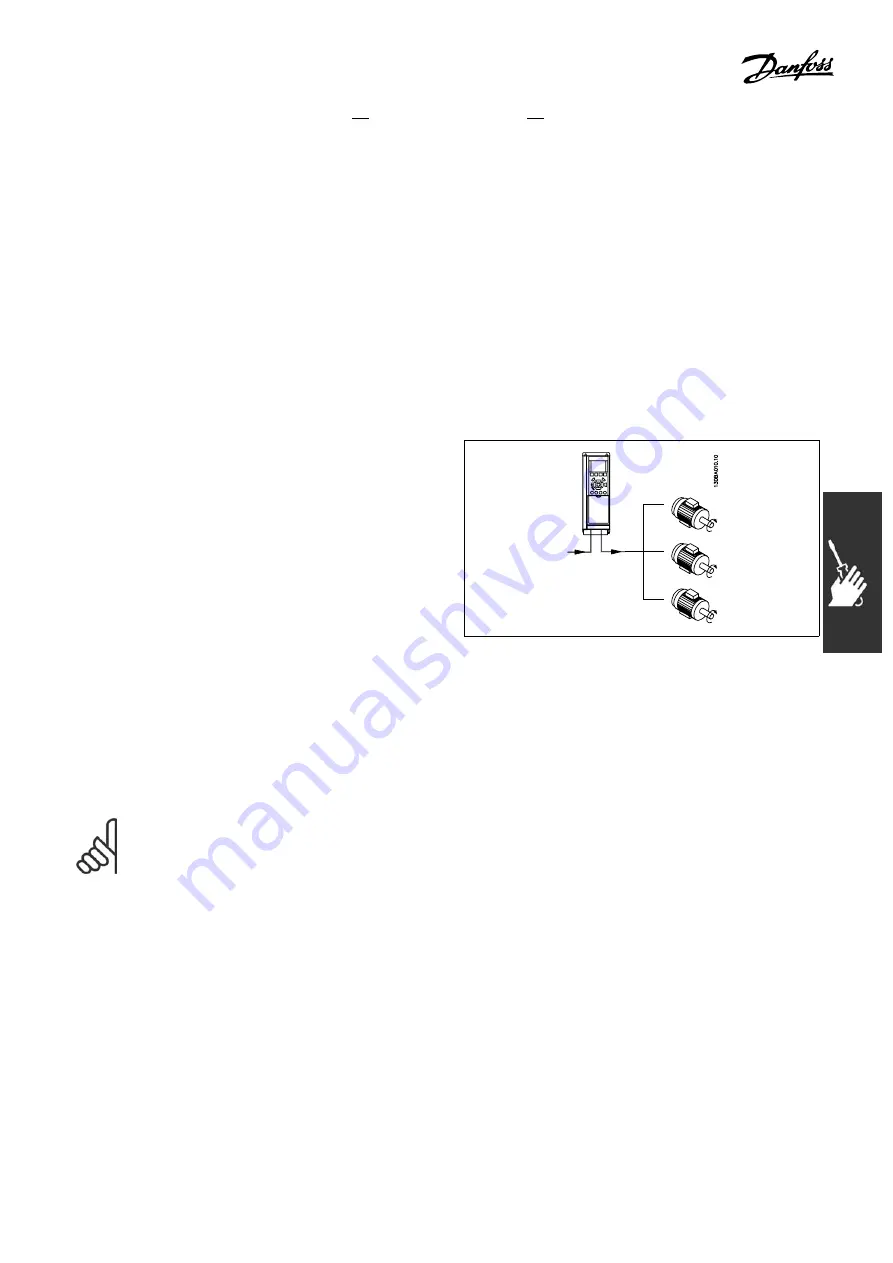
FC 300 Instruction Manual
How to Install
"
Control of Mechanical Brake
In hoisting/lowering applications, you need to be able to control an electromechanical brake.
•
Control the brake using any relay output or digital output (terminal 27 or 29).
•
Keep the output closed (voltage-free) as long as the adjustable frequency drive is unable to
"support" the motor, for example due to the load being too heavy.
•
Select
Mechanical brake control
[32] in par. 5-4* for applications with an electromechanical brake.
•
The brake is released when the motor current exceeds the preset value in par. 2-20.
•
The brake is engaged when the output frequency is less than the frequency set in par. 2-21 or
2-22, and only if the adjustable frequency drive carries out a stop command.
If the adjustable frequency drive is in alarm mode or in an overvoltage situation, the
mechanical brake immediately cuts in.
"
Parallel connection of motors
The FC 300 is able to control several
parallel-connected motors. The total current
consumption of the motors must not exceed the
rated output current I
INV
for the FC 300.
Problems may arise at start and at low RPM values if motor sizes are widely different because small motors’
relatively high ohmic resistance in the stator calls for a higher voltage at start and at low rpm values.
The electronic thermal relay (ETR) of the FC 300 cannot be used as motor protection for the individual motor
in systems with motors connected in parallel. Further motor protection must be provided, e.g. thermistors
in each motor or individual thermal relays. (Circuit breakers are not suitable as protection).
NOTE
When motors are connected in parallel, parameter 1-02
Automatic motor adaptation (AMA)
cannot
be used and Parameter 1-01
Torque characteristics
must be set to
Special motor characteristics
.
For more information, see
VLT AutomationDrive FC 300 Design Guide.
"
Thermal motor protection
The electronic thermal relay in FC 300 has received the UL-approval for single motor protection,
when parameter 1-26
Motor thermal protection
is set for
ETR Trip
and parameter 1-23
Motor
current, I
M, N
is set to the rated motor current (see motor nameplate).
33
MG.33.A4.22 - VLT is a registered Danfoss trademark
Содержание FC 302
Страница 34: ...FC 300 Instruction Manual How to Install 34 MG 33 A4 22 VLT is a registered Danfoss trademark...
Страница 74: ...FC 300 Instruction Manual Troubleshooting 74 MG 33 A4 22 VLT is a registered Danfoss trademark...
Страница 77: ...FC 300 Instruction Manual Index 4 485 V DC 63 77 MG 33 A4 22 VLT is a registered Danfoss trademark...