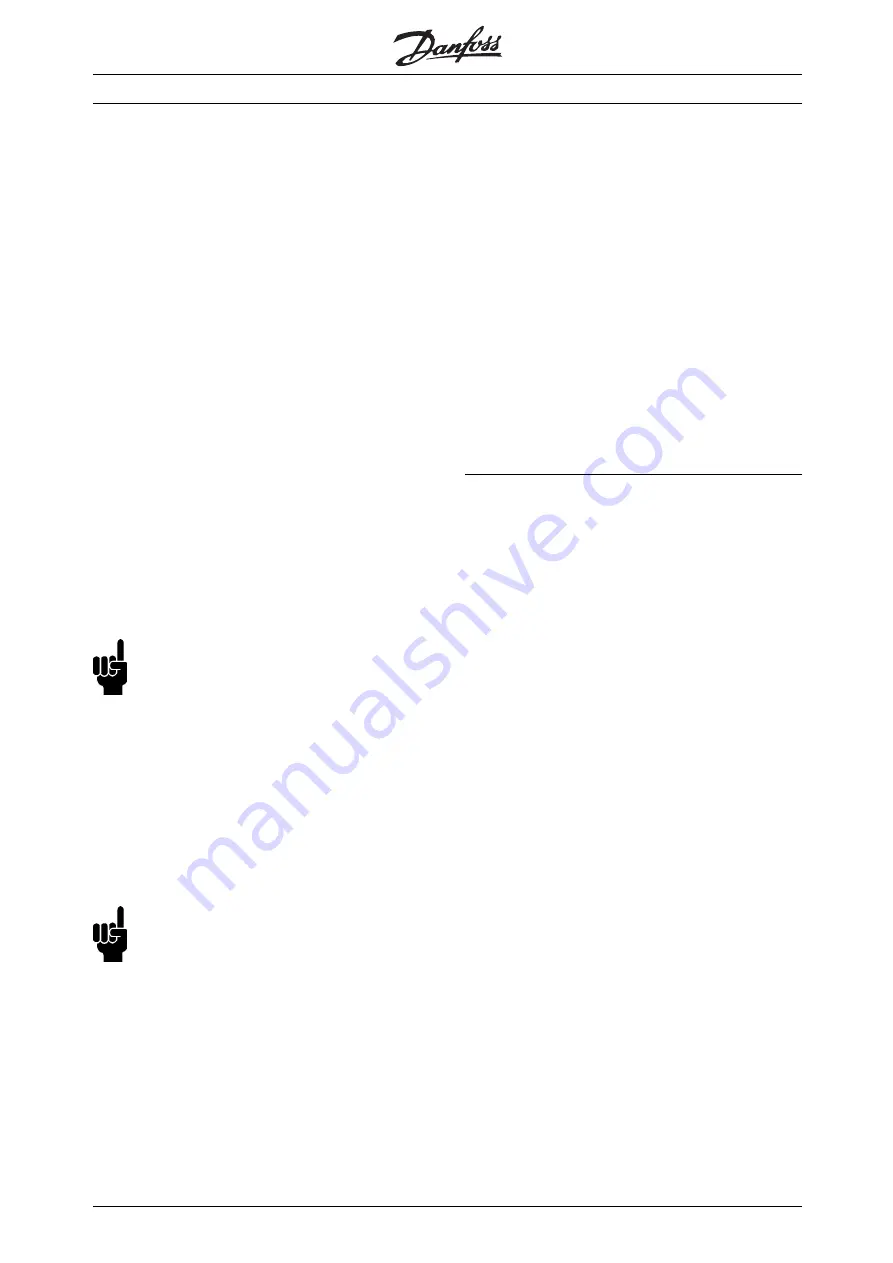
DMS Manual
■
Operation
Once the DMS has been installed, wired and
programmed according to the instructions,
it can be operated.
■
Powering-up the DMS
Power may now be applied to the DMS unit.
The "On" LED should glow when the 24VCD
Control Supply is turned On.
■
Starting the motor :
C24VDC to the "Reset/ Coasting
stop inverse input (27).
To start the motor in the Forward direction,
use the Start CW Input (18). To initiate a stop,
open the Start CW Input.
To start the motor in the Reverse direction, use the
Start CCW Input (19).This feature is optional. To
initiate a stop, open the Start CCW Input.
If the direction of rotation is wrong, change any
two of mains
or
motor phases.
Disconnecting the +24VDC to the "Reset/ Coasting
stop inverse input (27) will disable the DMS and
cause the motor to coast to stop.
NB!:
If both Start CW & Start CCW inputs are
active together, the motor will stop.
■
Brake Release
(For variants with Braking function only -
variants SB, EB, ER).
When a Start is initiated, the DMS automatically
generates a brake release command. This will release
the brakes before the motor starts running.
The motor brake can also be released without
starting the motor by conn24VDC to
the Brake Release input (124).
NB!:
Mains supply to the DMS is required for
the operation of Brake Release. The
Electromechanical brake supply is
not
short-circuit protected.
■
Operation with AS-i Interface
The AS-i switch profile S-7.E is used, having the
following inputs and outputs:
•
Start CW (DO)
•
Start CCW (D1)
•
Brake Control (D2)
•
Reset (D3)
•
Ready output(D0)
•
Run Output (D1)
•
Fault Output (D2)
The profile codes with the different variants are:
•
Profile 7E 1 for Extended
•
Profile 7E 3 for Extended with Brake
•
Profile 7E 4 for Extended with Brake & Reversing
MG.05.A2.02 - VLT is a registered Danfoss trademark
12