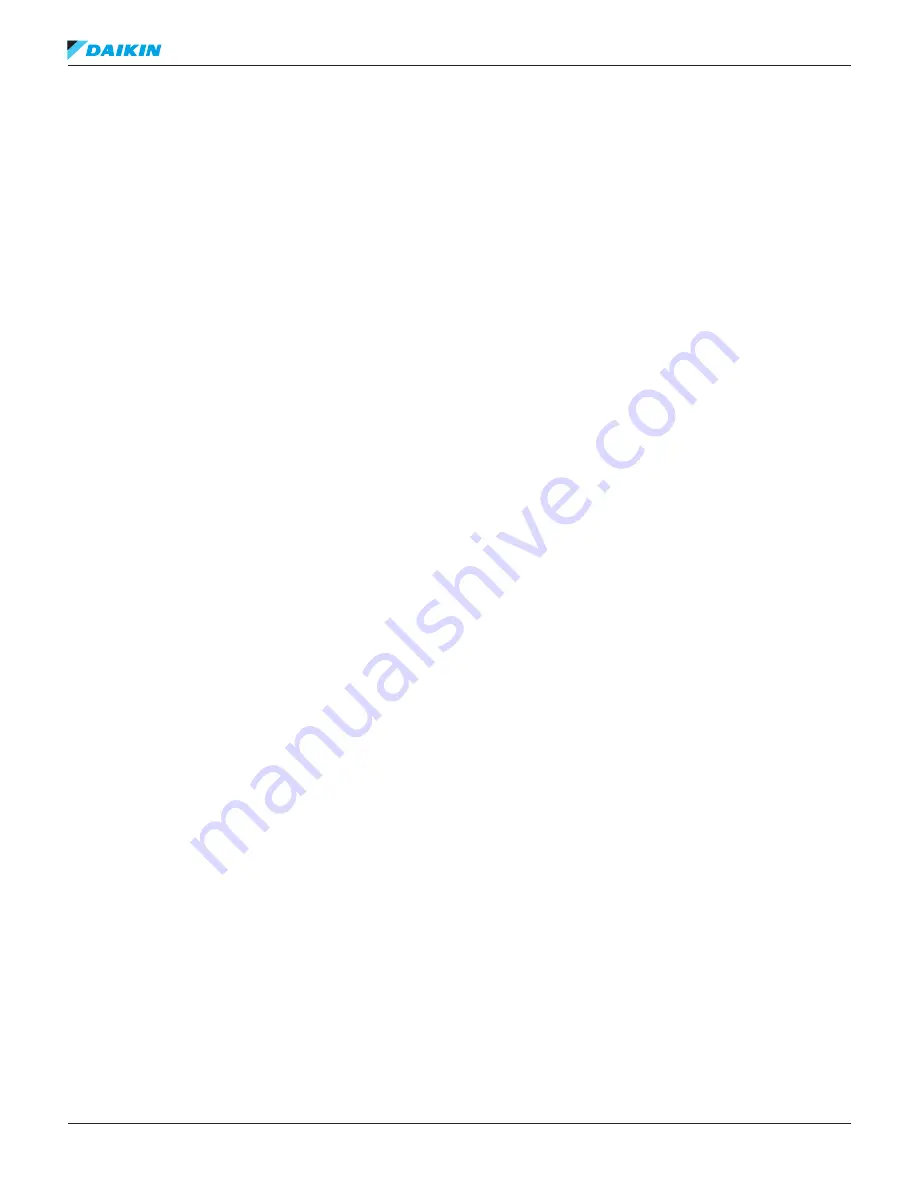
www.DaikinApplied.com 11
AG 31-011 • REFRIGERANT PIPING DESIGN
Possible accessories for this system include:
•
A hot gas bypass port. This is a specialty fitting that
integrates with the distributor – an auxiliary side
connector (ASC).
• A pump down solenoid valve. If a pump down is utilized,
the solenoid valve will be located just before the TX valve,
as close to the evaporator as possible.
• Receivers in the liquid line. These are used to store
excess refrigerant for either pump down or service (if the
condenser has inadequate volume to hold the system
charge), or as part of a flooded low ambient control
approach (More information about flooded low ambient
control approach is available under
).
Receivers are usually avoided because they remove sub-
cooling from the condenser, increase the initial cost, and
increase the refrigerant charge.
Liquid lines should be sloped 1/8 inch per foot (10.4 mm/m) in
the direction of refrigerant flow. Trapping is unnecessary.
Suction Lines
Suction gas lines allow refrigerant gas from the evaporator to
flow into the inlet of the compressor. Undersizing the suction
line reduces compressor capacity by forcing it to operate at
a lower suction pressure to maintain the desired evaporator
temperature. Oversizing the suction line increases initial project
costs and may result in insufficient refrigerant gas velocity
to move oil from the evaporator to the compressor. This is
particularly important when vertical suction risers are used.
(More information about designing vertical suction risers is
“Suction Line Sizing” on page 20
)
Suction lines should be sized for a maximum of 2 to 3°F (1.1 to
1.7°C) pressure loss. The actual pressure drop in PSI (kPa) will
depend on the refrigerant.
Suction Line Piping Details
While operating, the suction line is filled with superheated
refrigerant vapor and oil. The oil flows on the bottom of the
pipe and is moved along by the refrigerant gas flowing above
it. When the system stops, the refrigerant may condense in the
pipe depending on the ambient conditions. This may result in
slugging if the liquid refrigerant is drawn into the compressor
when the system restarts.
To promote good oil return, suction lines should be pitched
1/8 inch per foot (10.4 mm/m) in the direction of refrigerant
flow. Evaporator connections require special care because
the evaporator has the potential to contain a large volume of
condensed refrigerant during off cycles. To minimize slugging
of condensed refrigerant, the evaporators should be isolated
from the suction line with an inverted trap as shown in
and
The trap should extend above the top of the evaporator before
leading to the compressor.
1.
With multiple evaporators, the suction piping should be
designed so that the pressure drops are equal and the
refrigerant and oil from one coil cannot flow into another
coil.
2.
Traps may be used at the bottom of risers to catch
condensed refrigerant before it flows to the compressor.
Intermediate traps are unnecessary in a properly sized
riser as they contribute to pressure drop.
3. Usually with commercially produced air conditioning
equipment, the compressors are “pre-piped” to a
common connection on the side of the unit.
4.
Suction line filter-driers are available to help clean the
refrigerant before it enters the compressor. Because
they represent a significant pressure drop, they should
only be added if circumstances require them, such as
after compressor burnout. In this instance, the suction
filter drier is often removed after the break-in period for
the replacement compressor. Suction filter-driers catch
significant amounts of oil, so they should be installed per
the manufacturer’s specifications to promote oil drainage.