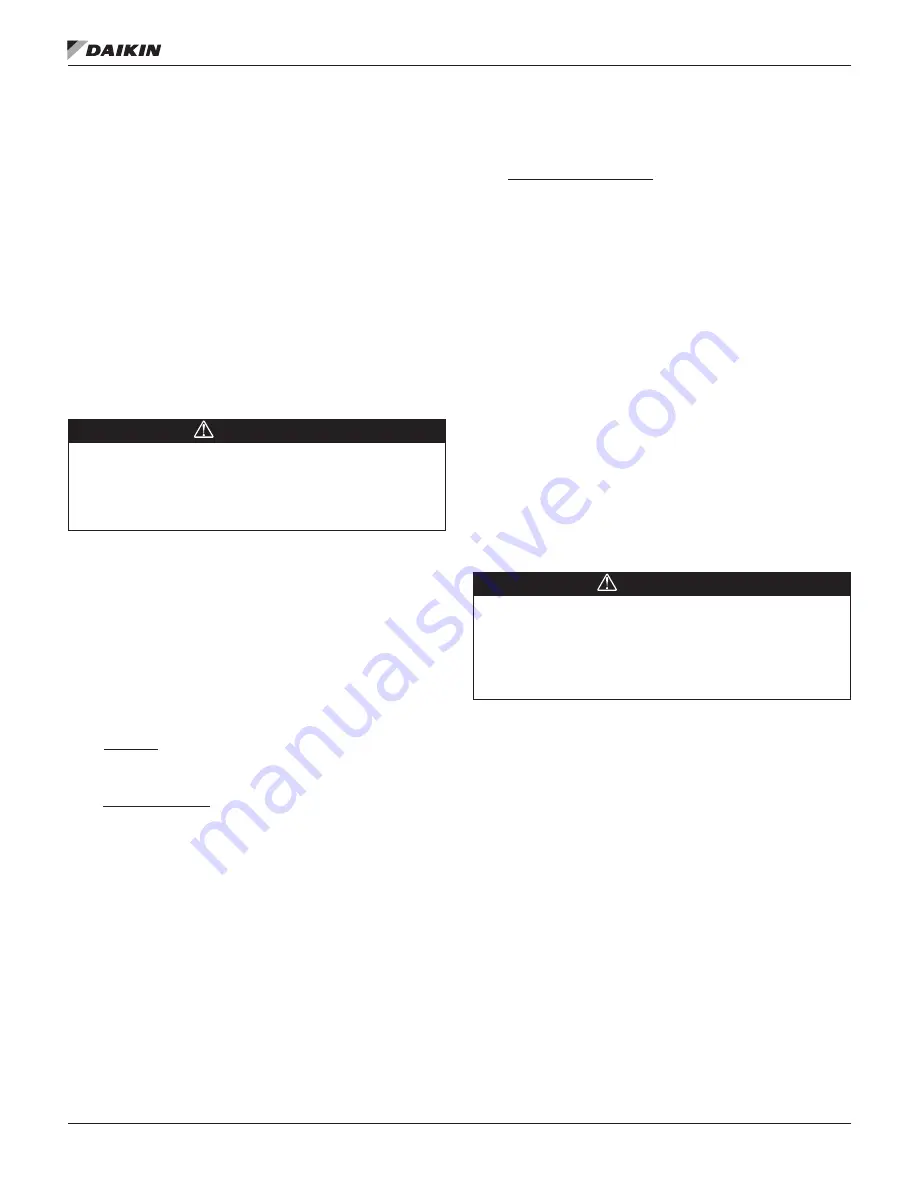
M
aInTenanCe
www.DaikinApplied.com 63
IOM 1210-7 • MAGNITUDE
®
MODEL WMC CHILLERS
M
aInTenanCe
Service Programs
It is important that an air conditioning system receive adequate
maintenance if the full equipment life and full system benefits
are to be realized. Maintenance should be an ongoing program
from the time the system is initially started. A full inspection
should be made after 3 to 4 weeks of normal operation on a
new installation and on a regular basis thereafter.
Daikin Applied offers a variety of maintenance services through
the local Daikin Applied service office and can tailor these
services to suit the needs of the building owner. Most popular
among these services is the Daikin Applied Comprehensive
Maintenance Contract. For further information concerning the
many services available, contact your local Daikin Applied
service office.
Chiller Maintenance
DANGER
Use approved Lock Out / Tag Out procedures to disconnect
power from the unit. Wait 20 minutes after disconnecting
power from the unit before opening any compressor access
covers. The DC link capacitors store enough energy to cause
electrocution.
Electrical System
Maintenance of the electrical system involves the general
requirement of keeping connections clean and tight. Pump
interlocks and flow switches should be checked to be sure they
interrupt the control circuit when tripped.
Cleaning and Preserving
A common cause of service calls and equipment malfunction
is dirt. This can be prevented with normal maintenance. The
system components most subject to dirt are:
1. Strainers: Remove and clean strainers in the chilled
water system and condenser water system at every
inspection.
2. Condenser Tubes: Inspect the condenser tubes
annually for fouling and clean if required. The standard
waterboxes should be removed with care due to their
weight. One method for handling standard waterboxes
follows (only qualified service personnel should perform
these tasks):
• After draining water, remove all but two head bolts
at roughly 10 and 2 o’clock.
• Loosen the remaining two bolts to enable the head
to be separated from the tube sheet sufficiently for
a clevis pin or hook to be inserted into an open bolt
hole at the top of the head.
• Attach a hoist to the pin or hook, lift the head
to remove weight from the two remaining bolts,
remove the bolts, and carefully remove the head.
• Do not try to install a machine thread eyebolt into
the head vent fitting, which has pipe threads.
• Reverse this procedure to mount the head, using a
new gasket.
3. Condenser Flow Sensor: The condenser sensor
should be cleaned anytime the condenser is opened.
This should typically be performed at the annual
inspection; however, more frequent cleaning may be
required depending on the conditions of the jobsite.
Recommended maintenance includes the following:
• Check the sensor tip for buildup.
• Clean the tip using a soft cloth. Stubborn buildup —
such as lime — can be removed using a common
vinegar cleaning agent.
Water Treatment
Special care must be taken when utilizing open system water
that is usually not treated (such as lakes, rivers, and ponds).
The use of untreated water will result in corrosion, erosion,
slime buildup, scaling, or algae formation. Water treatment
service must be used. Special tube and water head material
may be required to reduce damage from corrosion. Daikin
Applied is not responsible for damage or faulty operation from
untreated or improperly treated water.
Seasonal Shutdown
CAUTION
The condenser and evaporator are not self-draining. Where the
chiller can be subject to freezing temperatures, the condenser
and evaporator must be drained of all water. Water permitted
to remain in the piping and vessels can rupture these parts if
subjected to freezing temperatures. Dry air blown through the
vessels will aid in forcing all water out.
Except for freezing conditions, it is desirable to leave water in
the vessels to avoid long term exposure to air.
Continuous forced circulation of antifreeze through the
vessels is one method of avoiding freeze up.
Seasonal Startup
Seasonal startup procedures are as follows:
1. Leak test the unit.
2. Check and tighten all electrical connections.
3. Replace the drain plugs (including cooling tower pump
and tower drain) if they were removed at shutdown the
previous season.
Содержание Magnitude
Страница 4: ......
Страница 23: ...Installation www DaikinApplied com 21 IOM 1210 7 MAGNITUDE MODEL WMC CHILLERS...
Страница 24: ...IOM 1210 7 MAGNITUDE MODEL WMC CHILLERS 22 www DaikinApplied com Installation Figure 20 Wiring Index...
Страница 25: ...Installation www DaikinApplied com 23 IOM 1210 7 MAGNITUDE MODEL WMC CHILLERS...
Страница 26: ...IOM 1210 7 MAGNITUDE MODEL WMC CHILLERS 24 www DaikinApplied com Installation Figure 21 Controller Box Wiring...