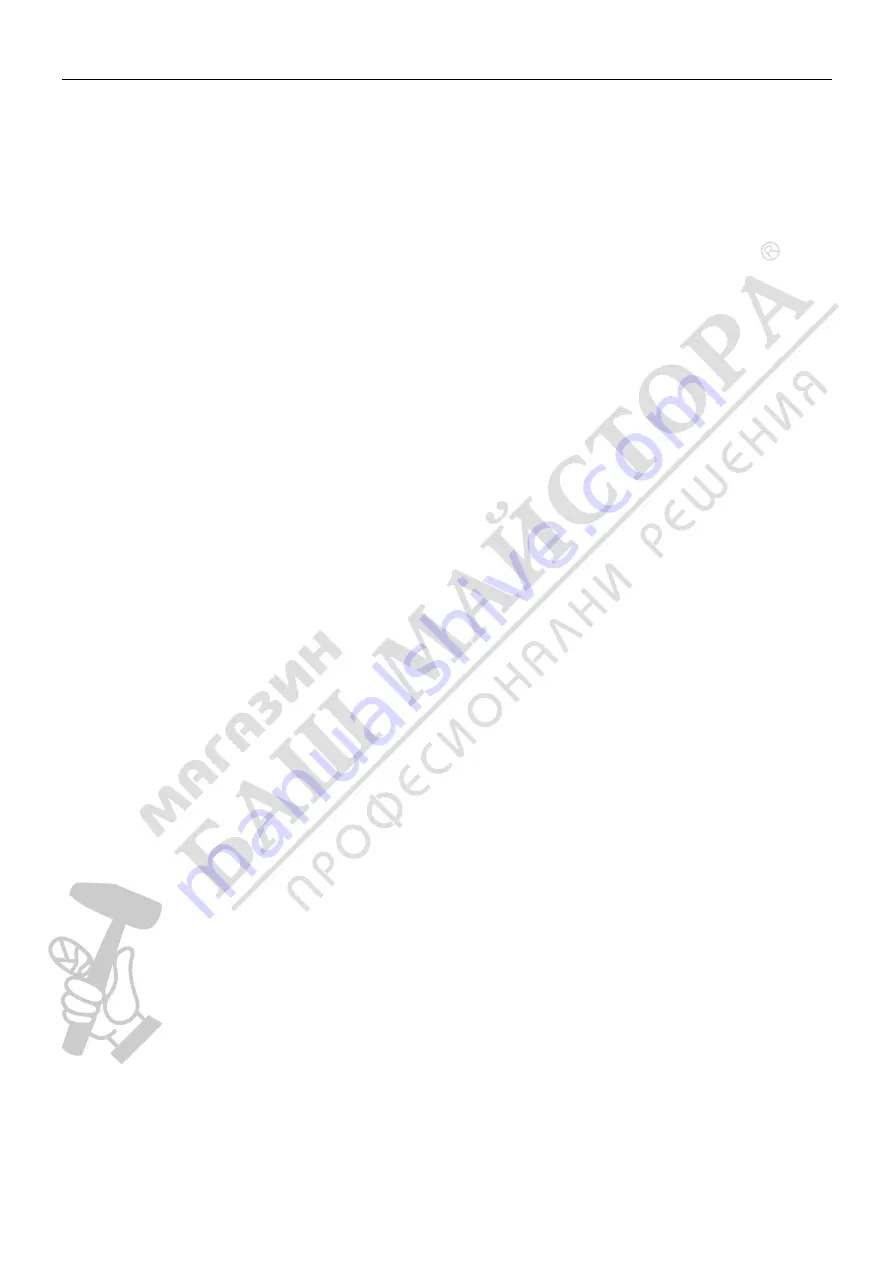
10
5.1.3 Setup for gasless MIG welding operation
5.1.3.1 Connect the MIG Torch Euro Connector (26) to the torch socket on the front of the welder (11). Secure
by firmly hand tightening the threaded collar on the MIG Torch Euro Connector clockwise.
5.1.3.2 Check that the correct flux cored, gasless wire, matching drive roller (21) and welding tip (30) are fitted
5.1.3.3 Connect Torch Connection Power Lead (14) to the negative (-) welding output terminal (13).
5.1.3.4 Connect Earth Lead Quick Connector (28) to the positive (+) output welding terminal (12).
5.1.3.5 Connect Earth Clamp (27) to the work piece. Contact with workpiece must be strong contact with clean,
bare metal, with no corrosion, paint or scale at the contact point.
5.1.4 Setup for gas shielded MIG welding operation
Note
-
Gas shielded MIG welding requires a shielding gas supply, gas regulator and gas shielded MIG wire.
These accessories are not supplied standard with the RW1500MP. Please contact your local Repco
branch for details
5.1.4.1 Connect the MIG Torch Euro Connector (26) to the torch socket on the front of the welder (11). Secure
by firmly hand tightening the threaded collar on the MIG Torch Euro Connector clockwise.
5.1.4.2 Check that the correct gas shielded wire, matching drive roller (21) and welding tip (30) are fitted
5.1.4.3 Connect Torch Connection Power Lead (14) to the positive (+) welding output terminal (12)
5.1.4.4 Connect Earth Lead Quick Connector (28) to the negative (-) output welding terminal (13).
5
.1.4.5 Connect Earth Clamp (27) to the work piece. Contact with workpiece must be strong contact with clean,
bare metal, with no corrosion, paint or scale at the contact point.
5.1.4.6 Connect the gas regulator (optional) and gas line to the inlet on the rear panel (15). If the regulator is
equipped with a flow gauge, the flow should be set between 8
–
15 L/minute depending on application.
If gas regulator is not equipped with a flow gauge, adjust pressure so gas can just be heard coming out
of the torch conical nozzle (29). It is recommended that gas flow is checked again, just prior to starting
weld This can be done by triggering the MIG torch with the unit powered up..
Содержание VARMIG 1605D PROFIMIG
Страница 23: ...22 10 CONNECTION DIAGRAM OF THE MACHINE...