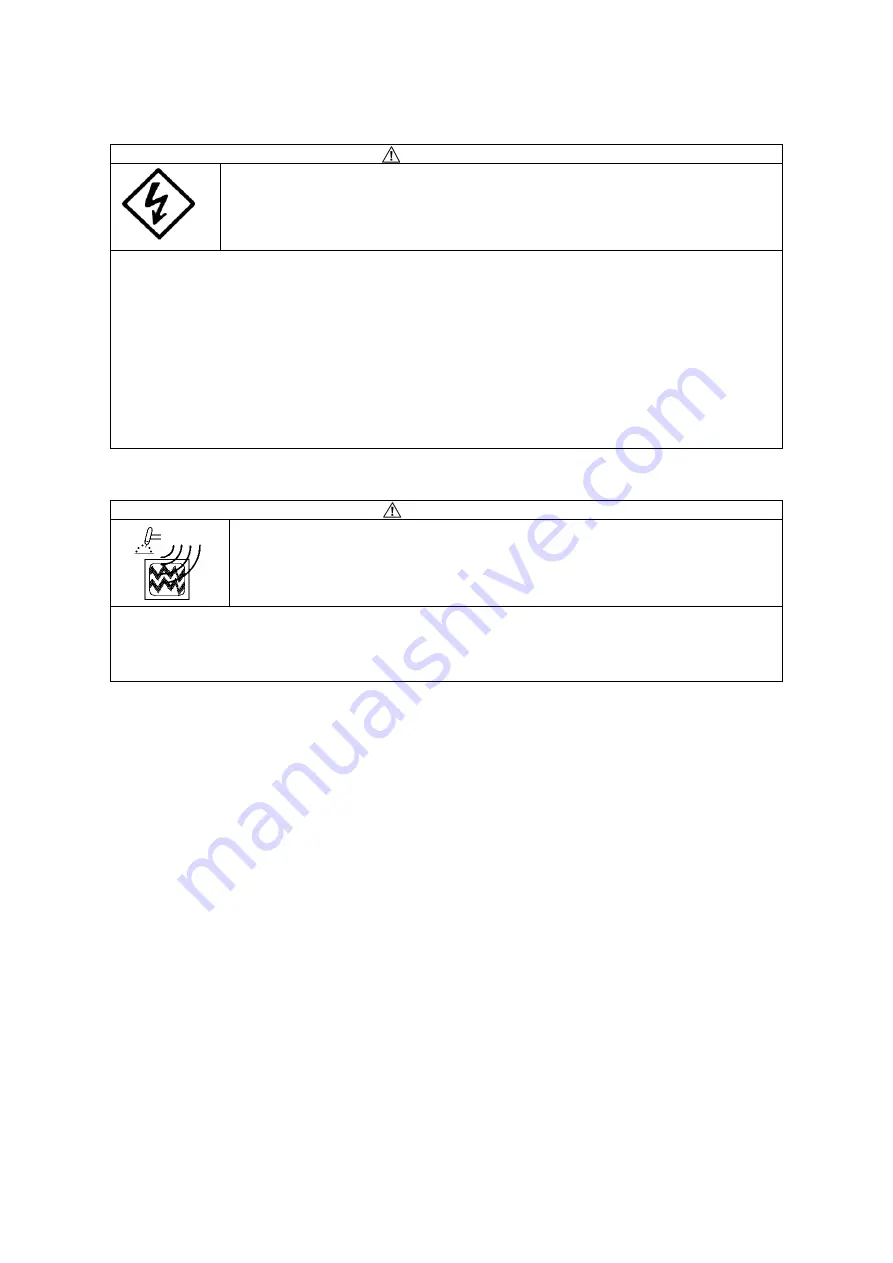
- 15 -
8.
CONNECTION PROCEDURE AND GROUND FOR SAFETY USE
WARNING
Observe the following to prevent electric shock.
Do not touch the live electrical parts; otherwise, you might receive serious electric shock or
get burned.
٨
Do not touch the live electrical parts.
٨
Have a qualified electric engineer ground the case of the welding power source. Have a
qualified electric engineer ground the base metal or jig electrically connected, following a
local low.
٨
Connect the welding machine with all the line disconnect switches inside the switch box
turned off.
٨
Do not use a cable with lack of capacity or a damaged cable.
٨
Tighten and insulate the connections of cables.
٨
Attach the case properly after connecting the cable.
8.1 Connecting of the Welding Power Source
CAUTION
To prevent electromagnetic troubles, read the following.
Also, if electromagnetic troubles occur, check the following again.
٨
Do not use an unnecessarily long cable.
٨
The welding cable is placed as closely on the floor or ground as possible.
٨
Place a base metal cable and an electrode cable as closely as possible.
٨
Do not ground the welding power source commonly with other machines.
HF