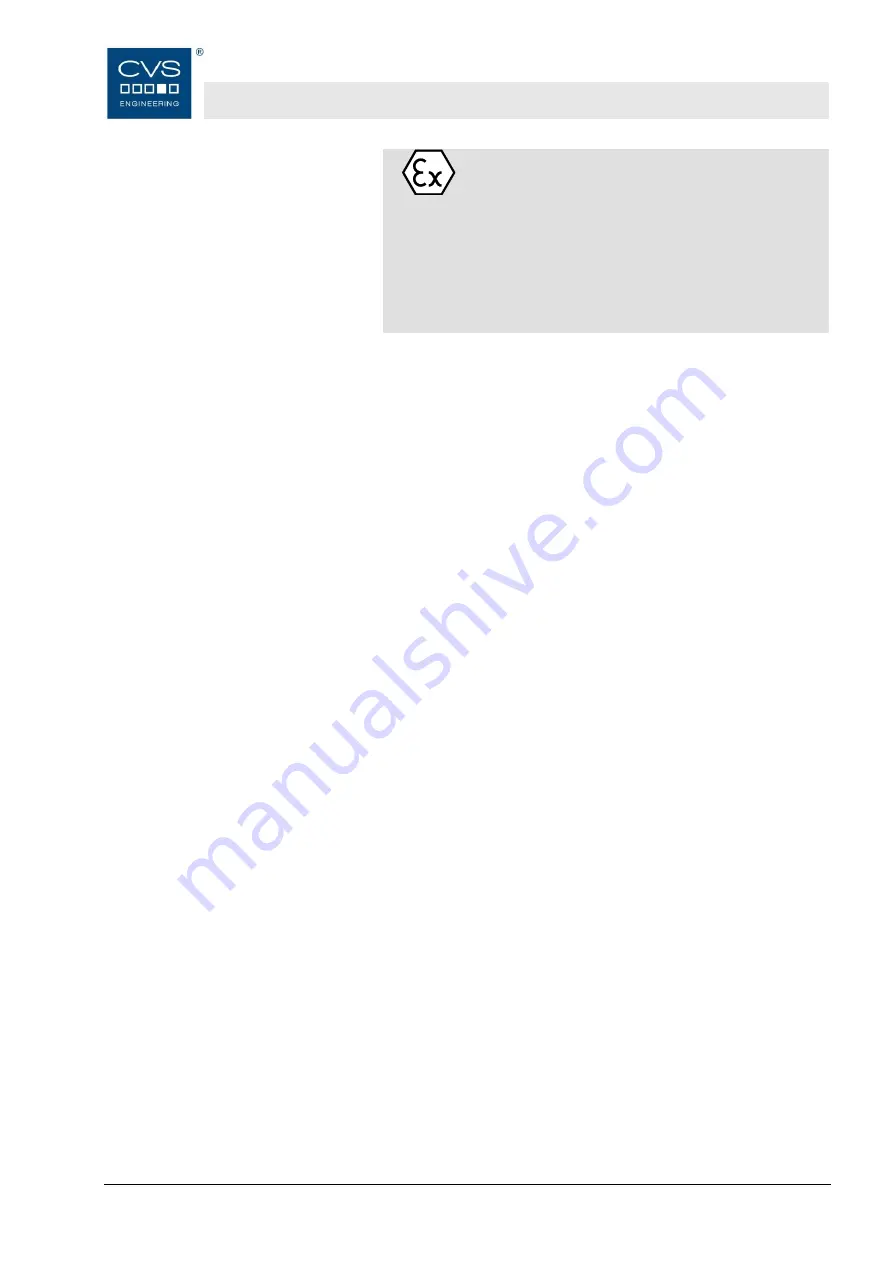
VacuStar W900 / W1300 / W1600
Safety
9
If explosive gases and gas mixtures are conveyed, the
following guidelines must be observed:
– 2014/34/EC
Devices and protection systems for the proper
use in explosive environments
– 99/92/EC
Health protection and safety of the employees in
potentially explosive areas
Only use VacuStar W for the intended use.
All specifications in these operating instructions have to be strictly
complied with (technical data, ATEX regulations, etc.)
All types of claims due to damage arising from improper use are
excluded. The operator alone shall be responsible for any damage
arising from improper use.
2.3 Acceptance and monitoring
The VacuStar W itself is not subject to any acceptance and
monitoring obligation.
2.4 Operator's responsibility
The VacuStar W is used for industrial purposes. The operator of
the VacuStar W is therefore subject to the legal obligations
concerning occupational safety.
The provisions valid at the place of installation as well as the safety
and accident prevention regulations of the Institution for statutory
accident insurance and prevention must be observed. The operator
must in particular:
inform himself on the valid industrial safety regulations.
determine the additional hazards that arise from the special
working conditions at the machine's place of installation by
means of a hazard assessment.
implement the necessary rules of conduct for operation of the
machine at the place of installation by means of user
instructions.
check at regular intervals during the machine's entire period of
use whether the user instructions correspond to the current
state of the body of rules and regulations.
adapt the operation instructions, if necessary to the new
regulations, standards, and operating conditions .
clearly regulate the responsibilities for installing, operating,
maintaining and cleaning the device.
Содержание VacuStar W1300
Страница 38: ......