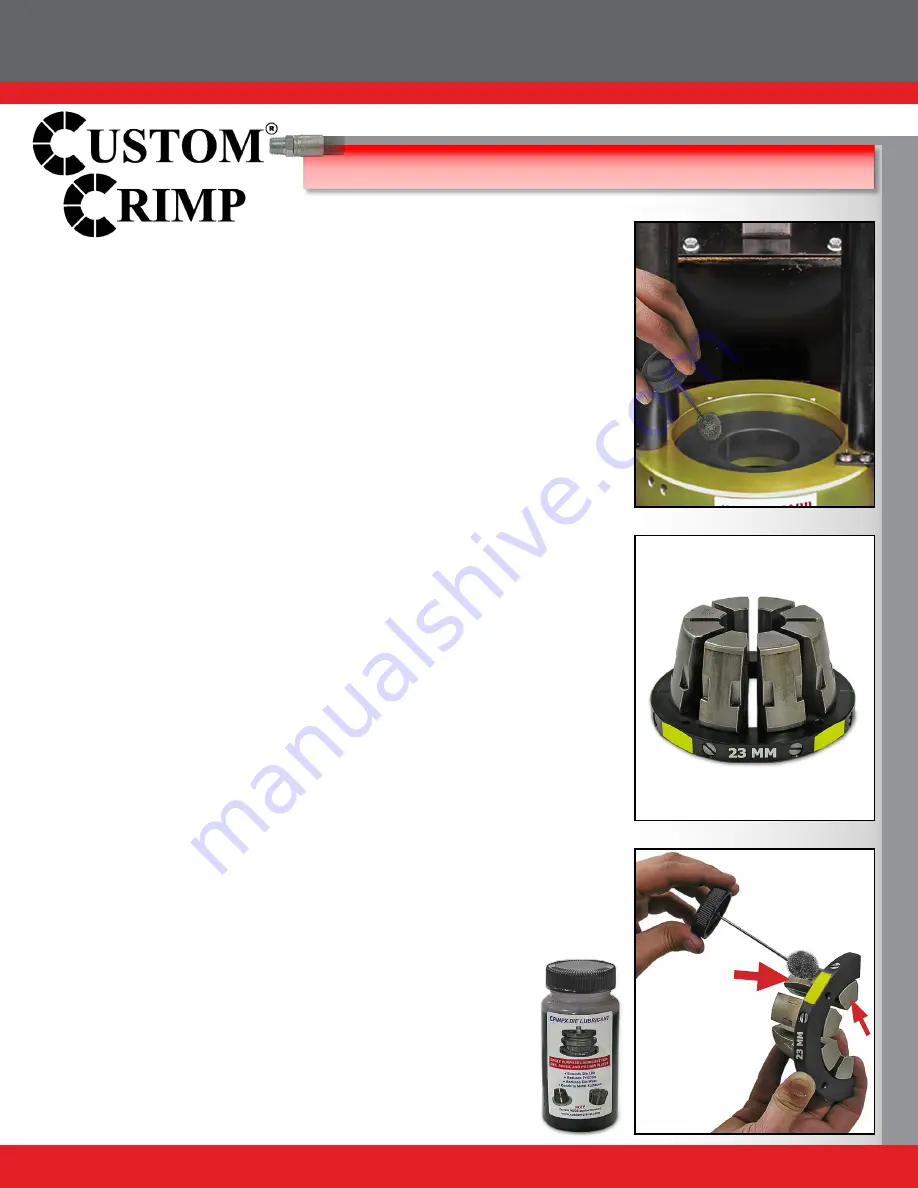
D105
Service Hose Crimper
8
CRIMPING PROCEDURE
Step 2:
Select the correct die set for the combination of hose and fitting
being crimped.
Note:
Consult your hose and fitting manufacturer for the correct die size
for the combination of hose and fitting being crimped.
Note:
The number etched on the OD of the die ring represents the fully
closed diameter of the die set in millimeters. In addition, die sets are
color-coded for easier identification.
Step 3:
Lubricate the contact surfaces, both bottom and outside edges
of the die fingers, with CrimpX oil (supplied with crimper) or a high
pressure molybdenum high pressure grease.
Failure to lubricate the contact surfaces with the correct lubricant
will cause the dies to seize in the compression ring, causing
damage to the die set as well as possibly damaging the crimper.
Note:
Follow the lubrication procedure prior to crimping procedure
.
Step 1:
Insert the pressure plate into the bottom flange of the crimper,
making sure that it is seated squarely into the bottom flange.
Make sure is lubricated prior to inserting the die set.
NOTE: FAILURE TO LUBRICATE THE DIE SET AND COMPRESSION
RING COULD RESULT IN THE DIE SET SEIZING IN THE BASE FLANGE.