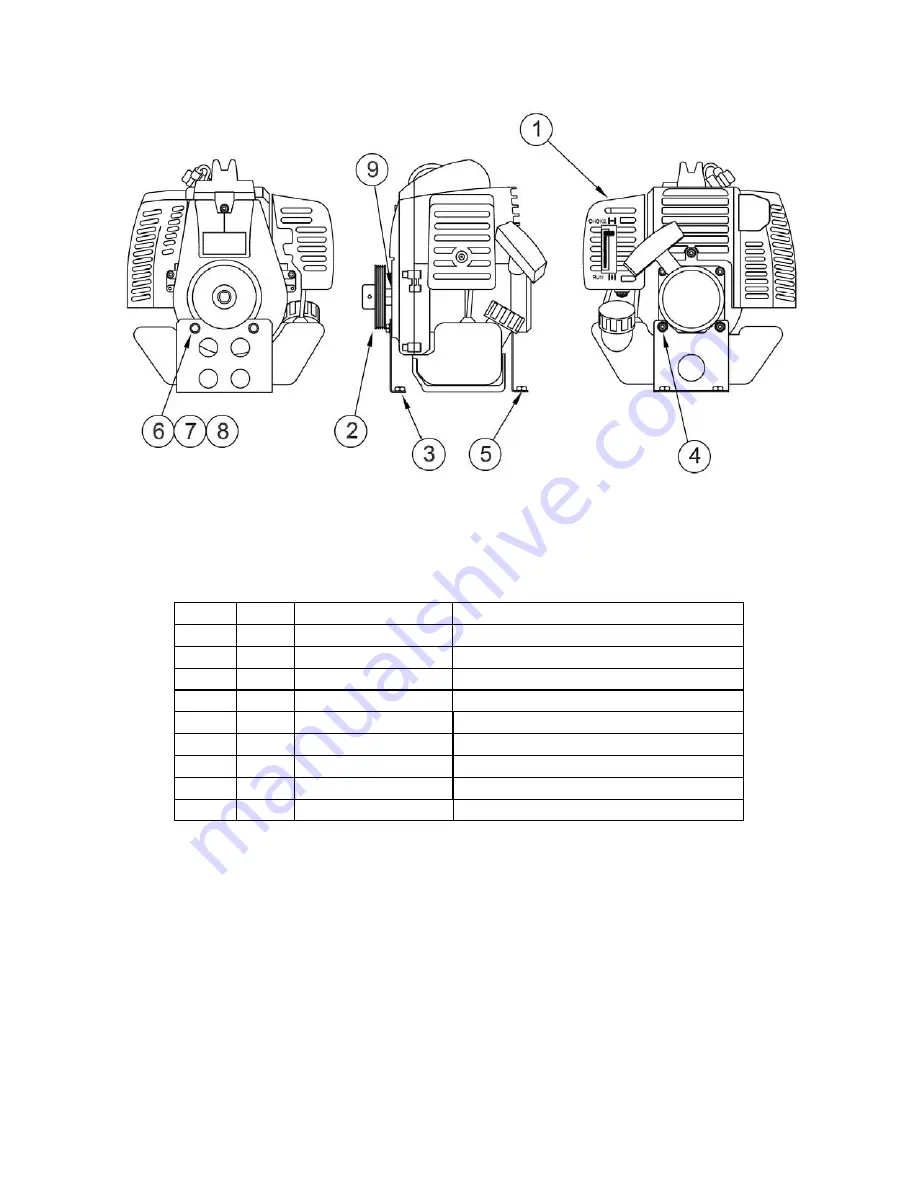
43
CURTIS
DYNA-FOG® Twister™ XL 3
TANAKA PF-4000 ENGINE ASSEMBLY P/N 39656-1
ITEM
QTY.
PART NUMBER
ITEM DESCRIPTION
1
1
39656
ENGINE, 40 CC, TANAKA
2
1
39712
PULLEY/SHAFT ADAPTER AY
3
1
39658
BRACKET, L.H.
4
12
120391
FLAT WASHER, #10
5
11
39659
BRACKET, R.H.
6
2
39720
BOLT 6 MM – 1 MM
7
2
120392
FLAT WASHER, 1/4
8
2
121753
LOCK WASHER, 1/4
9
1
39710
WASHER, LOCK, SPLIT, 10 MM
Содержание TWISTER XL 3 3950
Страница 5: ...5 Twister XL 3 Main Components Diagram ...
Страница 36: ...36 ...
Страница 39: ...39 PLATE AY ENGINE BLOWER P N 39668 ...
Страница 48: ...48 ...
Страница 49: ...49 TANAKA PF 4000 ENGINE ONLY ...
Страница 50: ...50 TWISTER XL 3 DUAL NOZZLE ATTACHMENT P N 39716 ...
Страница 52: ...52 OPTIONAL ...
Страница 53: ... A A A A B A A A A B C D A B DB D E C B A 38 53 ...
Страница 54: ... F 3954 ...
Страница 57: ... F 42 57 ...
Страница 59: ... F A A A A B 44 59 ...
Страница 60: ... F I E J F B Q A B B R E J D A Q N I JI E E IIHO B Q K A A R R R R R R A R R R R R R B A A 45 60 ...