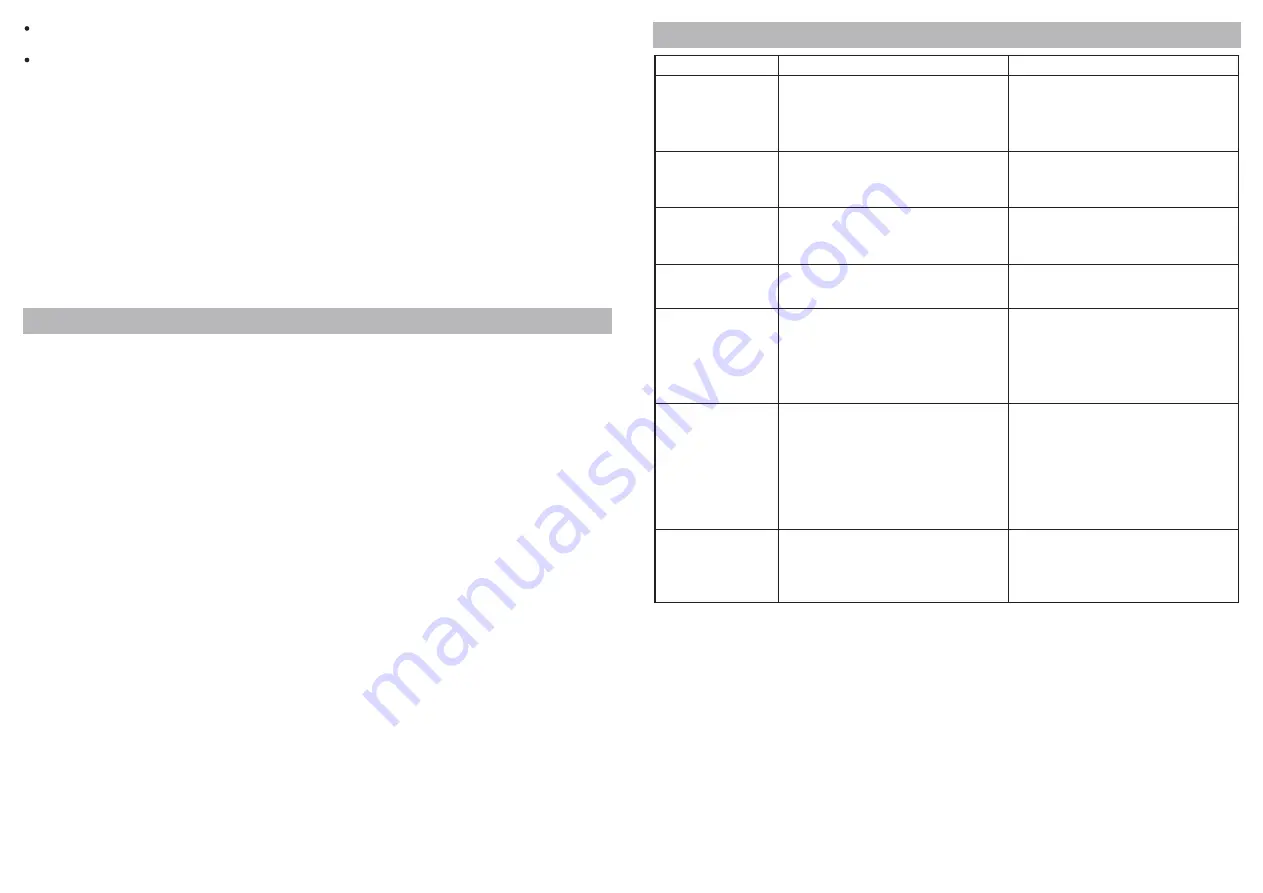
English
8
English
7
You should endeavor in any event to work with the lowest possible air pressure. This will give you
three significant advantages;
Avoid triggering the fastener driving tool if the magazine is empty.
Any defective or improperly functioning fastener driving tool must immediately be disconnected
from the compressed air supply and passed to a specialist for inspection.
In the event of longer breaks in work or at the end of the working shift, disconnect the tool from the
compressed air supply and it is recommended to empty the magazine.
The compressed air connectors of the fastener driving tool and the hoses should be protected
against contamination, the ingress of coarse dust chips, sand etc, will result in leaks and damage to
the fastener driving tool and the couplings.
Disconnect the tool from the compressor before adjusting, clearing jams, servicing &maintenance,
relocating and during non operation.
Regular lubrication, if your tool without using the in-liner automatic oilier, place 2 or 6 drops of
pneumatic tool oil into the air inlet before each work day or after 2 hours of continuous use
depending in the characteristic of workpiece or type of fasteners.
Air-operated tools must be inspected periodically, and worn or broken parts must be replaced to
keep the tool operating safely and efficiently. Check and change all worn or damaged O-ring, Seals,
etc. Tight all the screws and caps in case personal injury.
Make regular inspection for free movement of trigger, Spring and safety mechanism to assure safe
system is complete and functional: no loose and missing parts, no building or stocking parts.
Keep magazine and nose of tool clean and free of any dirt lint or abrasive particles.
When temperatures are below freezing, tools should be kept warm by any convenient, safe
method.
SYMPTOM
PROBLEM
SOLUTIONS
If the fastener is protruding, increase the air pressure in increments of 0.5 bar, checking the result
after each new adjustment;
If the fastener is driven into an excessive depth reduce the air pressure I increments of 0.5 bar until
the result is satisfactory.
1.energy will be saved,
2.less noise will be produced,
3.a reduction in fastener driving tool wear will be achieved.
V. Maintenance
VI. Troubleshooting (See Table 1)
Air leak near top
of tool or in
trigger area
Air leak near
bottom of tool.
1. O-ring in trigger valve is damaged.
2. Trigger valve head are damage.
3. Trigger valve stem, seal or O-ring
are damaged.
1. Check and replace O-ring.
2. Check and replace.
3.Check and replace trigger valve
stem, seal or O-ring
1. Loose screws.
2. Worn or damaged O-rings or
bumper.
1. Tighten screws.
2. Check and replace O-rings or
bumper.
Air leak between
body and cylinder
cap.
1. Loose screws.
2. Worn or damaged O-rings or seals.
1. Tighten screw.
2. Check and replace O-rings or
bumper.
Tool does not
operate well: can
not drive fastener
or operate
sluggishly.
1. Inadequate air supply.
2. Inadequate lubrication.
3. Worn or damaged O-rings or seals.
4. Exhaust port in cylinder head is
blocked.
1. Verify adequate air supply.
2. Place 2 or 6 drops of oil into air
inlet.
3. Check and replace O-rings or seal.
4. Replace damaged internal parts.
1. Incorrect or damaged fasteners.
2. Damaged or worn driver guide.
3. Magazine or nose screw loose.
4. Magazine is dirty.
1. Change and use correct fastener.
2. Check and replace the driver.
3. Tighten the magazine.
4. Clean the magazine.
Tool skips
fasteners.
Tool jams.
1. Worn bumper or damaged spring.
2. Dirt in front plate.
3. Dirt or damage prevents fasteners
from moving freely in magazine.
4. Worn or dry O-ring on piston or
lack of Lubrication.
5. Cylinder covers seal leaking.
1. Replace bumper or pusher spring.
2. Clean drive channel on front plate.
3. Magazine needs to be cleaned.
4. O-ring needs to be replaced.
And lubricate.
5. Replace Sealing washer.
Blade driving
fastener too deep.
1. Worn bumper.
2. Air pressure is too high.
1. Replace bumper.
2. Adjust the air pressure.