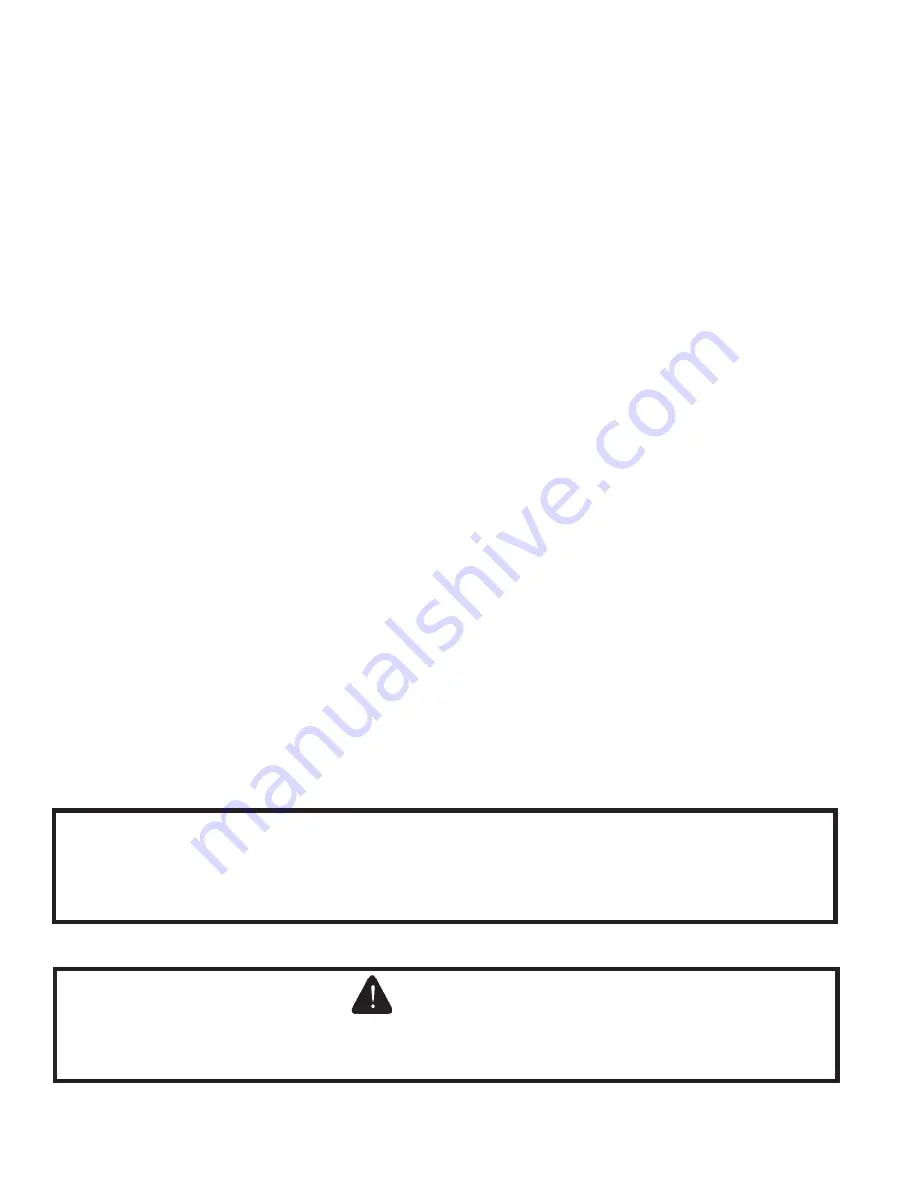
32
20) Verify that the smoke level still does not exceed #1 and that the draft over fire is -0.02 inch w.c.
21) Turn off the burner and remove pressure gauge. Install and tighten gauge port plug, than restart the burner.
22) Check for clean cutoff of the burner. Air in the oil line between fuel pump and nozzle will compress, while burner is
running, and expand, when burner shuts off, causing oil line pressure to drop and nozzle drip after burner stops. Cycle burner
on and off 5 to 10 times to purge air completely.
23) Check thermostat operation by raising or lowering its set point as required, cycling burner on and off.
24) Verify primary control operation and safety features according to procedure outlined in the instructions furnished with
the burner.
25) Check pressure limit control operation. Jump thermostat terminals and allow burner to run until boiler pressure exceeds
cut-in pressure plus the differential. The burner should shut down.
26) Check low water cut-off operation. With the thermostat still jumped, fire the boiler and crack the boiler drain valve so that
water is slowly drained from the boiler. Confirm that the burner shuts down before the water level drops below the bottom
of the sight glass.
Do not permit the boiler to fire without water visible in the sight glass
. Add water to the boiler and
confirm that the burner restarts. Remove thermostat jumper and reconnect thermostat upon check completion.
27) After the boiler has operated for approximately 30 minutes, check the boiler and heating system for leaks. Repair any
leaks found at once.
28) After the above checks have been completed, leave thermostat(s) at desired setting. Leave all instructions provided with
the boiler with owner or in boiler room, displayed near boiler.
29) After new boiler has been installed and put into continuous operation for several days, clean the boiler of oil, grease,
sludge, and other contaminants that may have been present in existing piping. This will prevent unsteady water line and water
carry over into supply main. The boiler boil-out should be done as follows:
a) Turn off the burner.
b) Drain water from boiler until about one inch of water is visible in gauge glass.
c) Run a hose or temporary piping from the boiler drain valve to a location where hot water can be safely discharged.
Drain approximately five gallons of water from the boiler and mix-in an appropriate amount of an approved boil-out
compound. Remove safety valve and refill the boiler with prepared solution through funnel. Replace safety valve.
d) Run a hose or temporary piping from the 1-1/2” skimmer tap on the upper rear section to a location where hot water
can be safely discharged.
e) Start the burner. Run boiler for several hours, boiling the water, without generating steam pressure. Open the water
feed valve sufficiently to allow a slight overflow of water through the skimmer tapping drain line. Continue boiling
until water coming out is clear.
f) Turn off the burner. Drain hot water from boiler through boiler drain valve to a location where hot water can be
safely discharged. Refill the boiler to normal water line level. If water in the gauge glass does not look clear, repeat
above boil-out procedure again until water clears out.
g) Conduct pH and Alkalinity test of water in the system. The pH reading should be in 7 to 11 range.
NOTICE
When substantial amount of make-up water is used due to lost condensate, or when
make-up water is hard or corrosive, water treatment is required. Contact qualified water
treatment company for recommended water treatment compounds and procedure.
WARNING
Attempts to use burners or burner configurations other than those shown in Table 12.0
could result in reliability problems, property damage or unsafe operation.
Содержание KSB Series
Страница 2: ...2...
Страница 12: ...10 FIGURE 4 1 FIELD INSTALLATION OF FLUE BAFFLES...
Страница 18: ...16 FIGURE 6 4 ALLAIR FROM OUTDOORS USING HORIZONTAL DUCTS INTO BOILER ROOM...
Страница 32: ...30 FIGURE 11 2 INDIRECT WATER HEATER FIELD WIRING...
Страница 43: ...41...