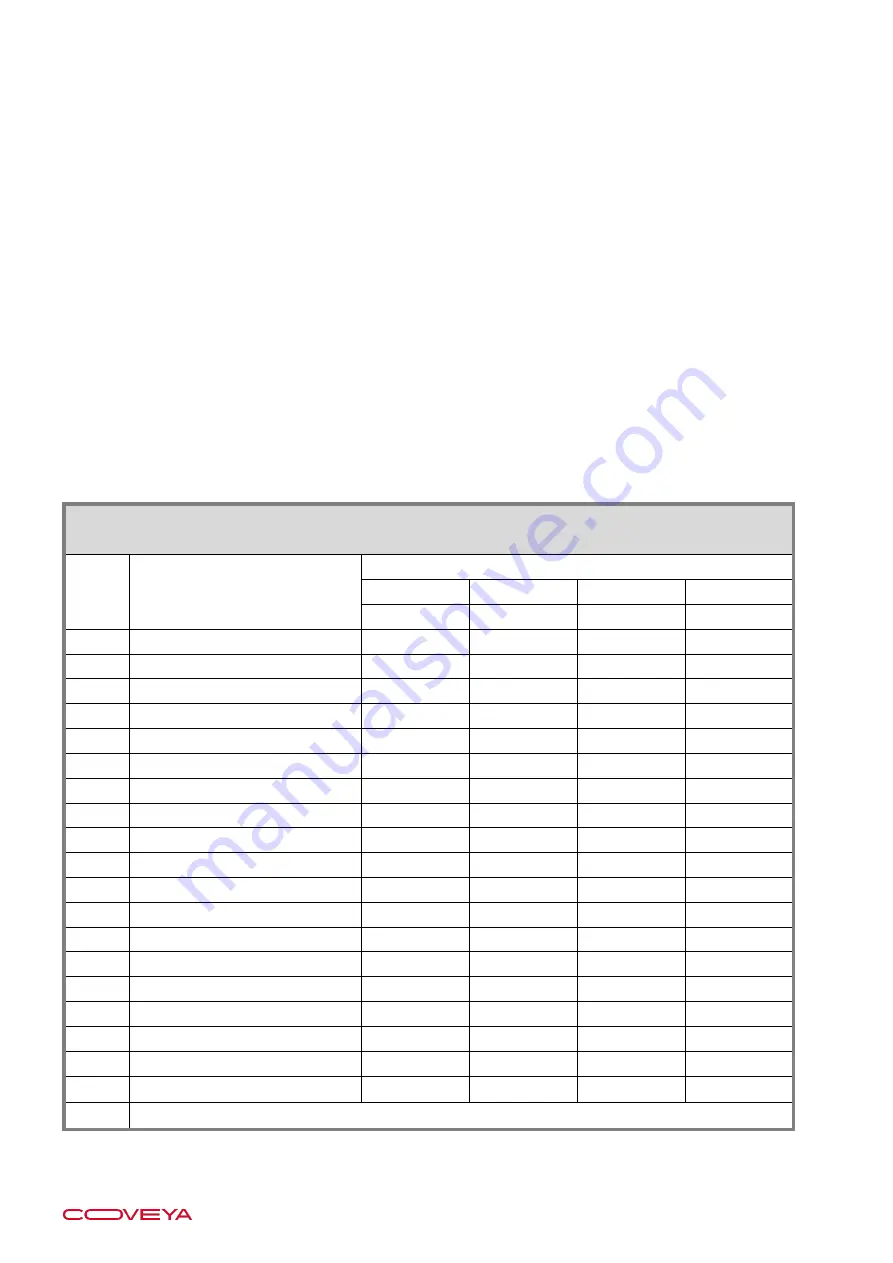
18
18.16 EMERGENCY GRAB WIRES & STOP STATIONS
All Emergency Stop devices must be regularly checked as per the Maintenance Schedule to ensure
they are functioning correctly. (i.e. activate and ensure the conveyor stops). All stop units and cabling
should be checked visually for damage and that all fixings are secure. Any maintenance work
required should be carried out by a qualified electrician.
18.17 MOBILE COMPONENTS
It is important that all lynch pins are inspected to ensure they are correctly positioned and the safety
retaining pins are secure. Pneumatic tyres should be inspected regularly for damage, wear and that
they are inflated with sufficient pressure as indicated on the tyre wall.
18.18 HYDRAULICS
Visually check that there are no leakages or damage at hose connections, along the hose length
and the ram. Check safety lynch pins are correctly inserted and retained. If the conveyor will not
reach this maximum position, it is an indication that there is insufficient hydraulic oil in the system.
Next lower the conveyor to its lowest position, ensuring that the hydraulic ram is in its closed position.
Proceed to add oil to the hydraulic pump as necessary.
18.19. DOCUMENTATION
All maintenance should be documented accordingly in the section at the rear of this Operation and
Instruction Manual
CONVEYOR ROUTINE MAINTENANCE SCHEDULE
Frequency
Item
Maintenance check
Weekly
Monthly
3 Monthly
Annual
or 60 hours
or 250 hours
or 750 hours
or 3000 hours
18.1
Material Handling
18.2
Material Feed Points
18.3
Rubber Belt
18.4
Rollers
18.5
Head Unit
18.6
Tail Unit
18.7
Joint Check
18.8
Motor & Electrics
18.9
Gearbox Units
18.10
Bearings
18.11
Top Covers
18.12
Bottom Covers
18.13
Belt Tracking
18.14
Belt Tensioning
18.15
Hopper
18.16
Emergency Grab Wires
18.17
Mobile Components
18.18
Hydraulics
18.19
Documentation
18.20
Trailer Maintenance (see Section 14
– page 10)