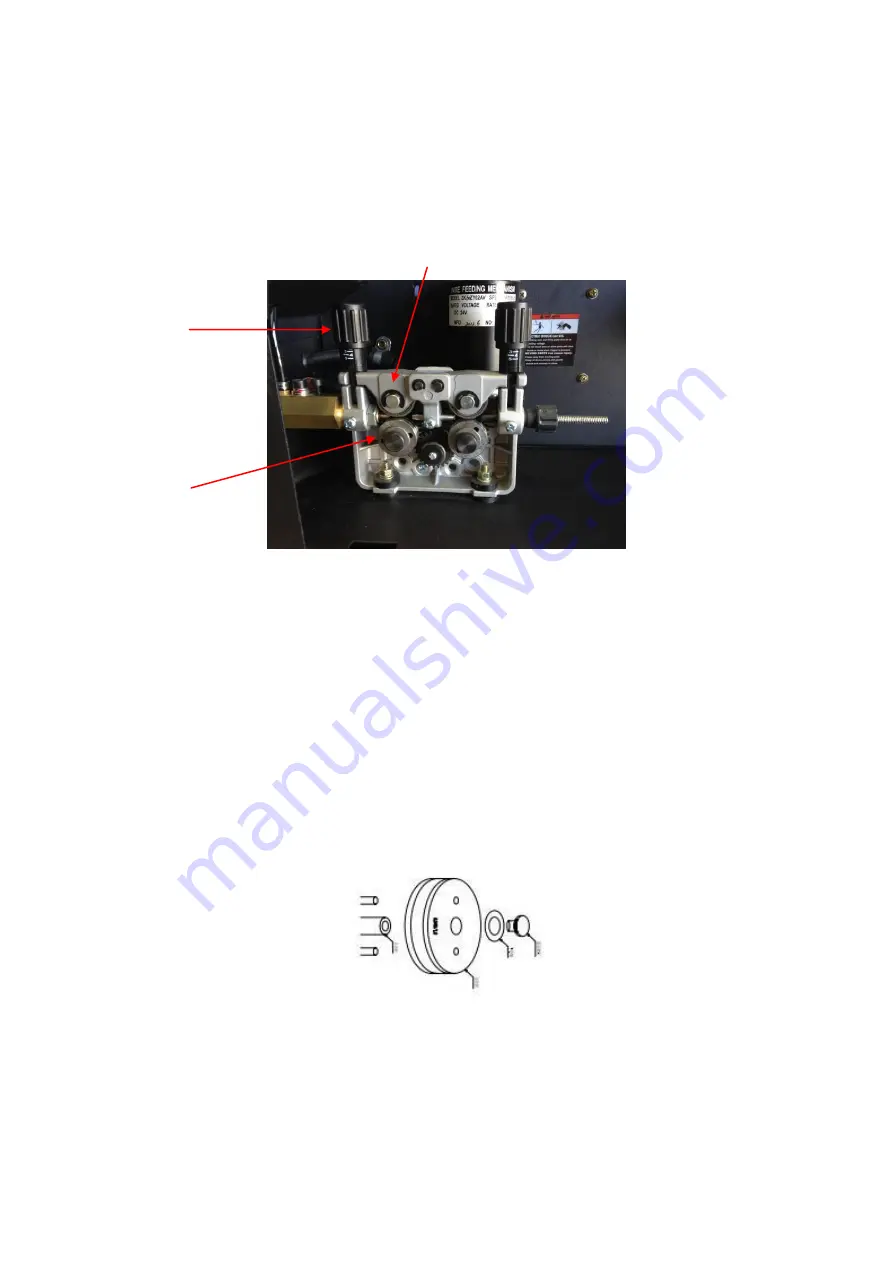
Page of 28
12
electrical codes for your specific area. Do not use an extension cord over 25 ft. in length.
3. INSTALL THE WIRE ROLLER - The wire roller has been factory installed. However, check to
make certain the correct wire groove is in place to accommodate the size of wire you are using.
Open the wire feed compartment. Adjust the drive roller according to the following steps, see
following picture about the wire feeder structure:
3.1 Open the door to the welder drive compartment.
3.2 Remove the drive tension by loosening the Drive Tension Adjuster (1) and moving the Drive
Tension Adjustor away from the Drive Tension Arm (2). The Drive Tension Arm will spring away from
the Drive Roller (3).
3.3 If there is wire already installed in the welder, roll it back onto the wire spool by hand-turning the
spool clockwise. Be careful not to all the wire to come out of the rear end of the inlet guide tube
without holding onto it or the wire spool will unspool itself. Put the end of the wire into the hole on
the outside edge of the wire spool and bend it over to hold the wire in place. Remove the spool of
wire from the drive compartment of the welder.
3.4 Remove the drive roller by turning the drive roll knob (3) counter-clockwise. Carefully slide the
drive roll assembly off of the drive shaft. This drive roll assembly consist of three pieces. The thumb
screw, washer spacer and the drive roll. Take care to keep from misplacing any of these pieces.
3.5 Based on the wire diameter select the correct groove. See the chart below for assistance.
When installing the drive roller, the number stamped on the drive roller for the wire size you are
using should be facing inward. Push the Drive Roller onto the Drive Roller Shaft.
(1)
(2)
(3)
Содержание MIG 250MGS
Страница 25: ...Page of 28 25 DIAGRAM PARTS LIST...