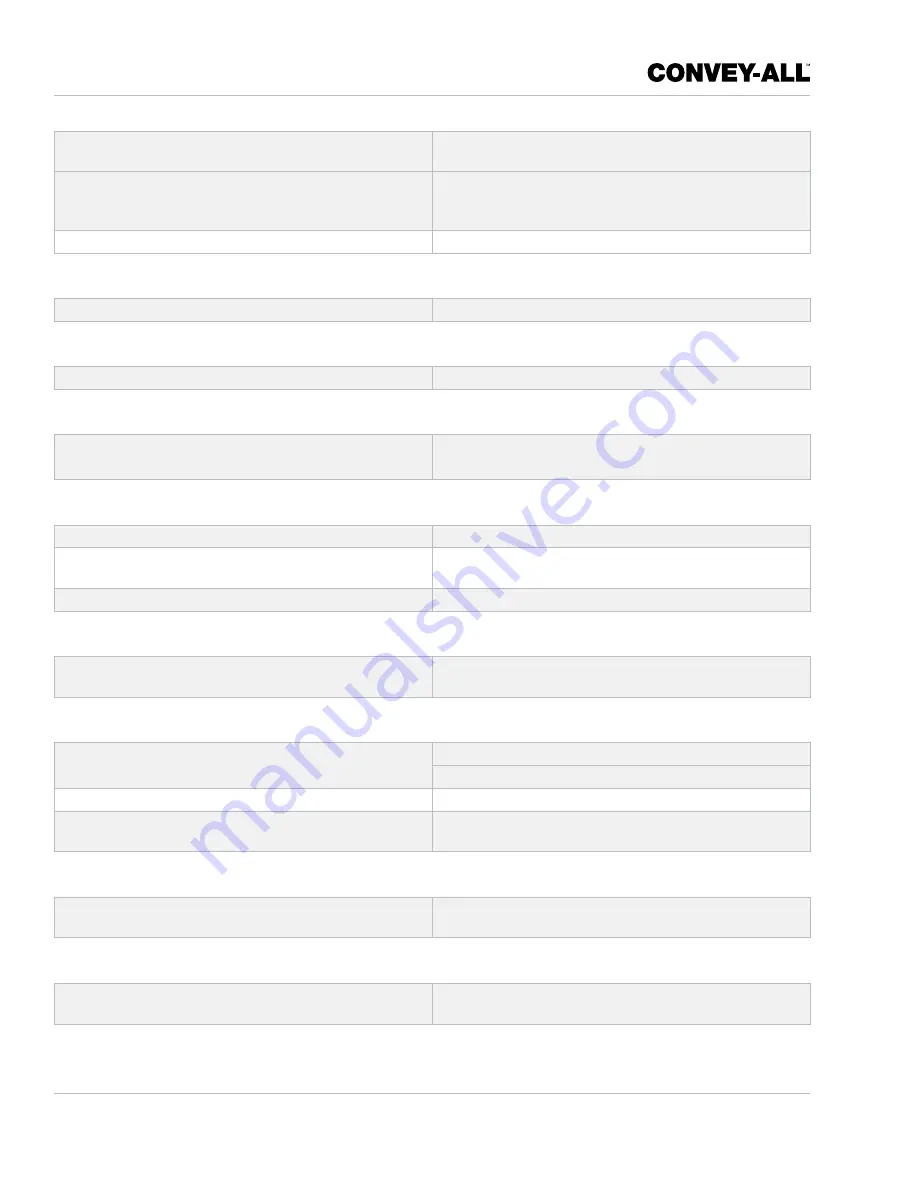
Operator’s Manual: 1600-SP Series Conveyor
5-2
Revised 06.2019
Conveyor belt doesn’t turn or is slipping, continued
Belt/roller is jammed
Check for sticks, stones, other objects jammed in belt
drive area and remove
Set screw (relief valve) on Detent on control valve on
belt drive valve isn’t set correctly
Sweet spot is to turn the set screw all the way in, then
turn back 1-1/2 turns. Turning back/out increases
volume of flow, turning in increases pressure.
Hydraulic motor on drive roller may be damaged
Hydraulic motor may need to be replaced
Conveyor belt won’t align
Roller lagging may be worn
Replace roller or have it re-lagged
Conveyor belt fraying
Belt not aligned
Align and adjust tension
Product leakage
Product may be getting under the belt at the hopper,
traveling up inside the belt and leaking off delivery end
Replace hopper flashing
Low capacity
Conveyor belt not tight enough
Tighten conveyor belt
Conveyor belt not pinched enough
Inside drive box there is a drive roller and pinch roller.
Be sure the belt is snug between both rollers.
Conveyor angle exceeds 30 degrees
Reposition with a lower tube slope
Belt is slowing down
Problem with 2 stage pump
Check flow of the pumps. Replacement of entire pump
may be needed
No hydraulic flow
Hydraulic valve closed or plugged
Open hydraulic valve
Clean or replace hydraulic valve
Hydraulic pump may be damaged
Check hydraulic pump. Replace if necessary
Hydraulic pressure may be low, check gauge. It should
be in 2000 lb range
Check hydraulic pump. Replace if necessary
Drive wheel keeps sinking to the ground
Leak in hydraulic manifold or cylinder
Replace cartridge in check valve, or
replace seals in cylinder
10 inch swing-out mover kit drives too fast/too slow
Hydraulic valve adjustment incorrectly set
Twist set screw IN to slow down wheels
Twist set screw OUT to speed up
Содержание 1685-SP
Страница 1: ...SELF PROPELLED CONVEYOR Models 1685 SP 1690 SP 1695 SP OPERATOR S MANUAL ...
Страница 4: ...This page intentionally left blank ...
Страница 8: ...Operator s Manual 1600 SP Series Conveyor 1 2 08 2016 This page intentionally left blank ...
Страница 60: ...Operator s Manual 1600 SP Series Conveyor 6 2 08 2016 This page intentionally left blank ...