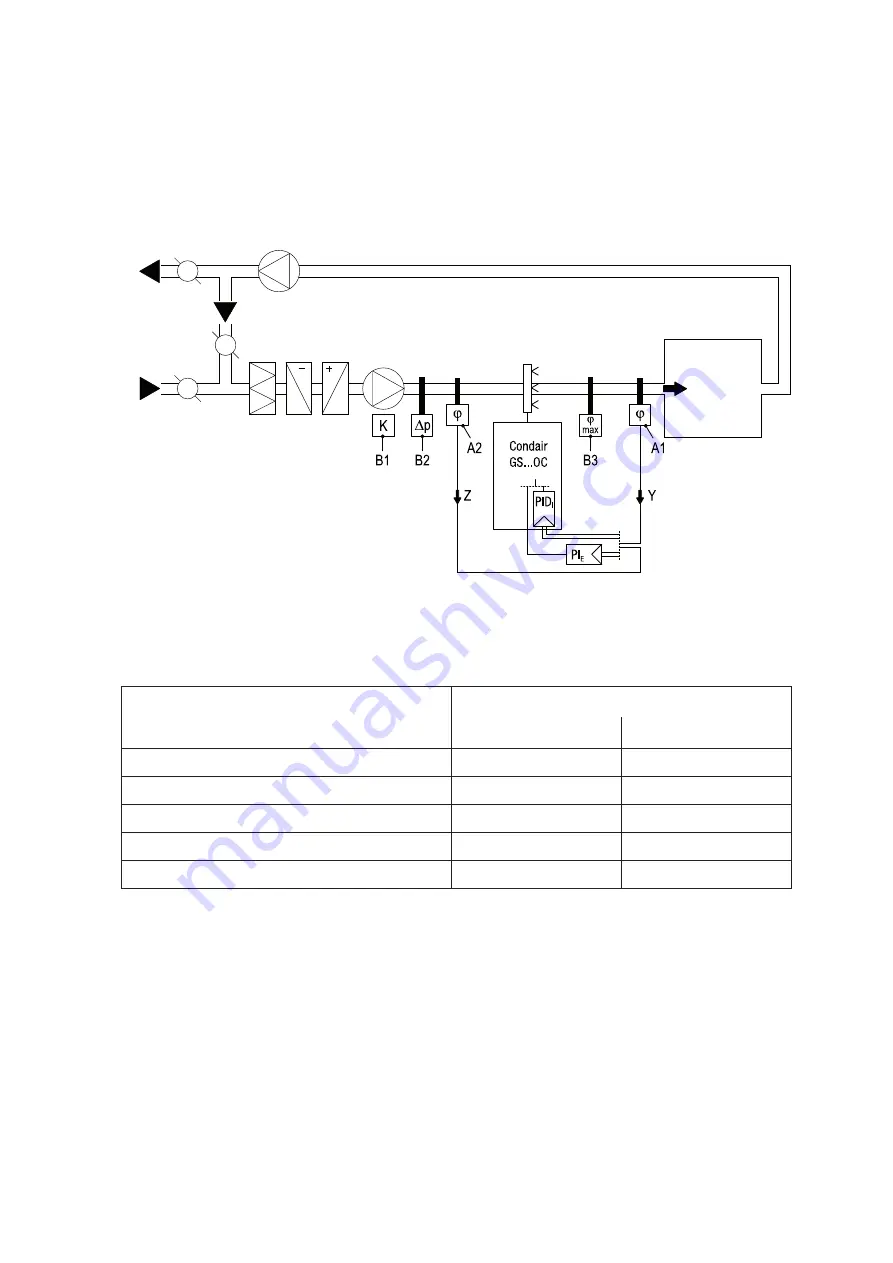
16
–
System 3: Supply air humidity control with continuous output limitation
Supply air humidity control (humidity sensor installed in supply air duct) should be used
only where room humidity control is impracticable for technical reasons
. Such systems always
require a PIcontroller.
The humidity sensor (A1) is located in the supply air duct after the steam distribution pipe. The
humidity sensor (A2) for the continuous output limitation is located in the supply air duct before the
steam distribution pipe. Such a system requires
the internal PID controller or
an external PIcontroller
with the option to connect a second humidity sensor.
Which humidity control system for which application?
Application
Location of the humidity sensor
Room or exhaust air duct
supply air duct
Air conditioning systems with:
Supply air portion up to 33%
System 1
System 1
Supply air portion up to 66%
System 1 or 2
System 2 or 3
Supply air portion up to 100%
System 2
System 3
Supply air humidity control
–––
System 3
Please contact your Condair supplier, if your application meets the following conditions:
– Humidification of small rooms up to 200 m
3
– Air conditioning systems with a high number of air exchanges
– Systems with variable air volume flow
– Test facilities with extreme control accuracy requirements
– Rooms with a high variation in max. steam capacity
– Systems with temperature fluctuations
– Cold rooms and systems with dehumidification
A1/2 humidity sensor
B1 ventilation interlock
B2 airflow monitor
B3 safety humidistat
PI
E
external PI-controller
PID
I
internal continuous controller (PID controller)
Y
input signal from A1
Z
input signal from A2
Содержание GS 120 OC
Страница 2: ......
Страница 69: ...69 Notes...
Страница 70: ...Notes...
Страница 71: ...Condair Ltd Printed in Switzerland Technical modifications reserved...