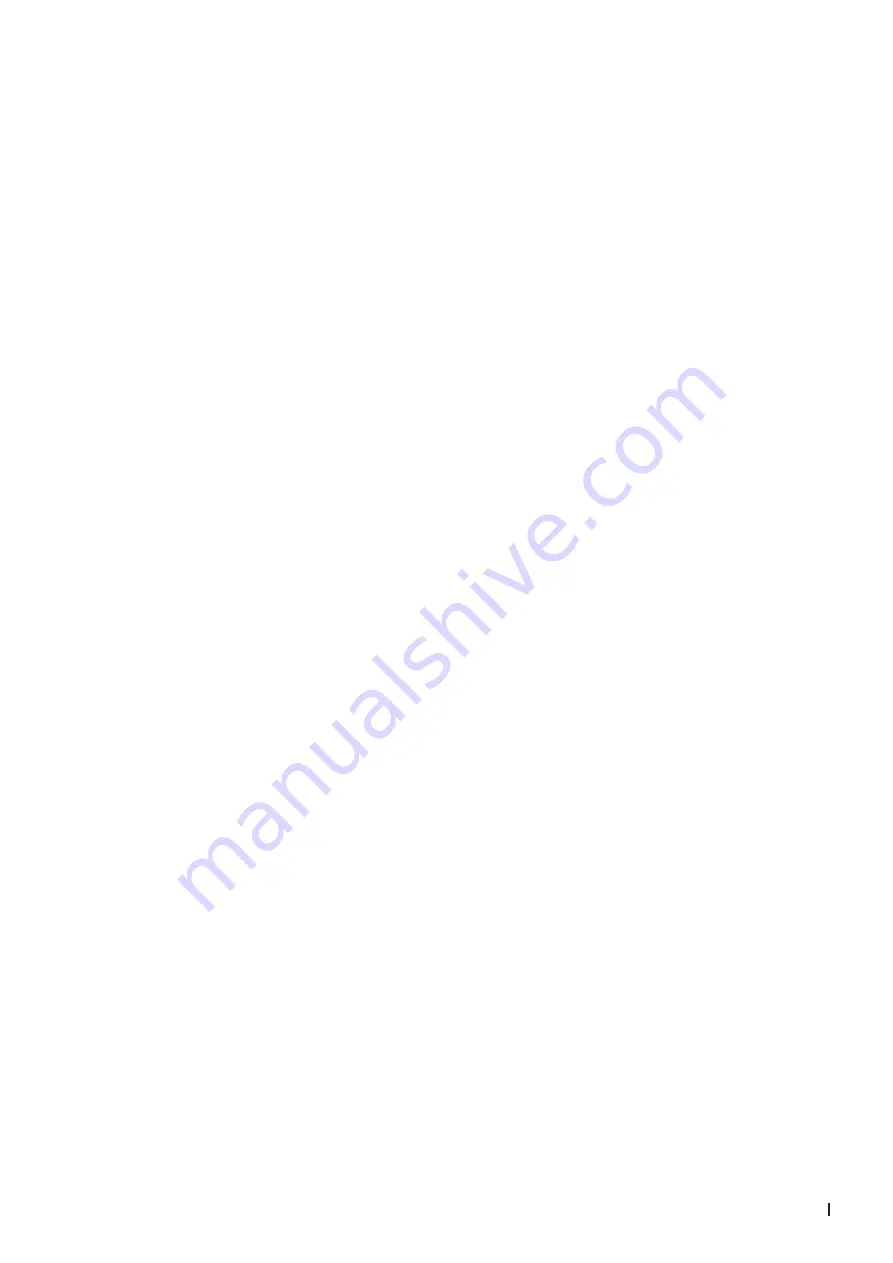
29
8.3.2
Maintenance log
After the work has been completed, the operator is informed of the maintenance result in the
form of a report. In particular, this refers to deviations from the setpoint or changes that have
been made in order to restore a safe operating state of the system.
8.3.3
Recommendations
To ensure optimal performance, we recommend changing the resin every 7 years.*
To ensure that the system is operated hygienically, we recommend disinfecting the resin during
each decommissioning as well as each recommissioning.*
*Additional work not included in the maintenance and carried out and invoiced in consultation
with the operator.
The replacement of defective parts is carried out in consultation with the operator. Spare and
wear parts will be charged for separately.
Logging, maintenance, servicing
Содержание CONDAIR SOFT
Страница 31: ...31 Appendix 9 3 Electrical connection...
Страница 48: ...48 9 5 1 Soft 60 System drawing Appendix...
Страница 49: ...49 9 5 2 Soft 120 System drawing Appendix...
Страница 50: ...50 9 5 3 Soft 200 System drawing Appendix...
Страница 51: ...51 9 5 4 Soft 320 System drawing Appendix...
Страница 52: ...52 9 5 5 Soft 400 System drawing Appendix...
Страница 54: ...54 Notes...
Страница 55: ...55 Notes...