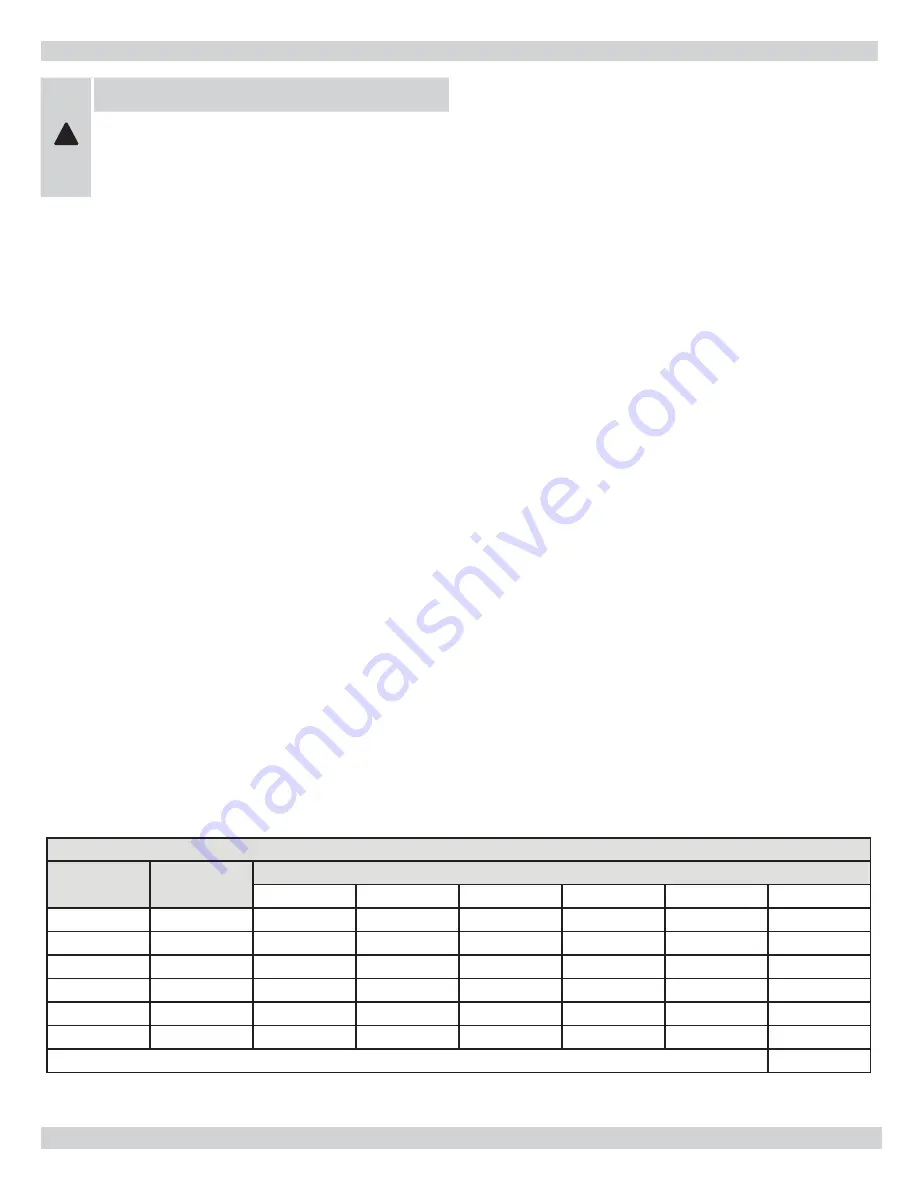
5
VENTILATION & COMBUSTION AIR
!
WARNING
Air openings to combustion area must
not be obstructed. Following instructions
below, adequate combustion air can be
maintained.
Provide combustion air and ventilation air in
accordance with the section “Air for Combustion and
Ventilation,” of the National Fuel Gas Code, ANSI
Z223.1 / NFPA 54, or applicable provisions of local
building codes.
Provide make-up air where exhaust fans, clothes
dryers, and kitchen ventilation equipment interfere
with proper operation.
National Fuel Gas Code recognizes several methods
of obtaining adequate ventilation and combustion air.
Requirements of the authority having jurisdiction may
override these methods.
• Engineered Installations. Must be approved by
authority having jurisdiction.
• Mechanical Air Supply. Provide minimum of
0.35 cfm per Mbh for all appliances located
within space. Additional requirements where
exhaust fans installed. Interlock each appliance
to mechanical air supply system to prevent main
burner operation when mechanical air supply
system not operating.
• All Indoor Air. Calculate minimum volume for all
appliances in space. Use a different method if
minimum volume not available.
A. Standard Method. Cannot be used if known
air in
fi
ltration rate is 0.40 air changes per
hour. See Table 1 for space with boiler only.
Use equation for multiple appliances.
Volume
≥
50 ft
3
x Total Input [Mbh]
B. Known Air In
fi
ltration Rate. See Table 1
for space with boiler only. Use equation
for multiple appliances. Do not use an air
in
fi
ltration rate (ACH) greater than 0.60.
Volume
≥
21 ft
3
⁄
ACH x Total Input [Mbh]
C. Refer to National Fuel Gas Code for opening
requirements between connected indoor
spaces.
• All Outdoor Air. Provide permanent opening(s)
communicating directly or by ducts with outdoors.
A. Two Permanent Opening Method. Provide
opening commencing within 12 inches of top
and second opening commencing within 12
inches of bottom of enclosure.
Direct communication with outdoors or
communicating through vertical ducts.
Provide minimum free area of 1 in² per 4
Mbh of total input rating of all appliances
in enclosure.
Communicating through horizontal ducts.
Provide minimum free area of 1 in² per 2
Mbh of total input rating of all appliances
in enclosure.
B. One Permanent Opening Method. Provide
opening commencing within 12 inches of top
of enclosure. Provide minimum clearance of
1 inch on sides/back and 6 inches on front
of boiler (does not supersede clearance to
combustible materials).
C. Refer to National Fuel Gas Code for additional
requirements for louvers, grilles, screens and
air ducts.
• Combination Indoor and Outdoor Air. Refer
to National Fuel Gas Code for application
information.
Table 1 - Minimum Room Volume, Indoor Air Only*
Input Mbh
Standard
Method
Known Air In
fi
ltration Rate Method (Air Changes Per Hour)
0.1
.02
.03
.04
.05
.06
112.5
5625
23625
11813
7875
5906
4725
3938
150
7500
31500
15750
10500
7875
6300
5250
187
9350
39270
19635
13090
9818
7854
6545
255
11250
47250
23625
15750
11813
9450
7875
262.5
13125
55125
27563
18375
13781
11025
9188
300
15000
63000
31500
21000
15750
12600
10500
* Table values based on boiler only. Add volume for any additional appliances.
Содержание CEG-C
Страница 30: ...30 INSTALLATION NOTES ...
Страница 31: ...31 INSTALLATION NOTES ...
Страница 32: ...COLUMBIA COMPANY Main offices and factory Pottstown PA ...