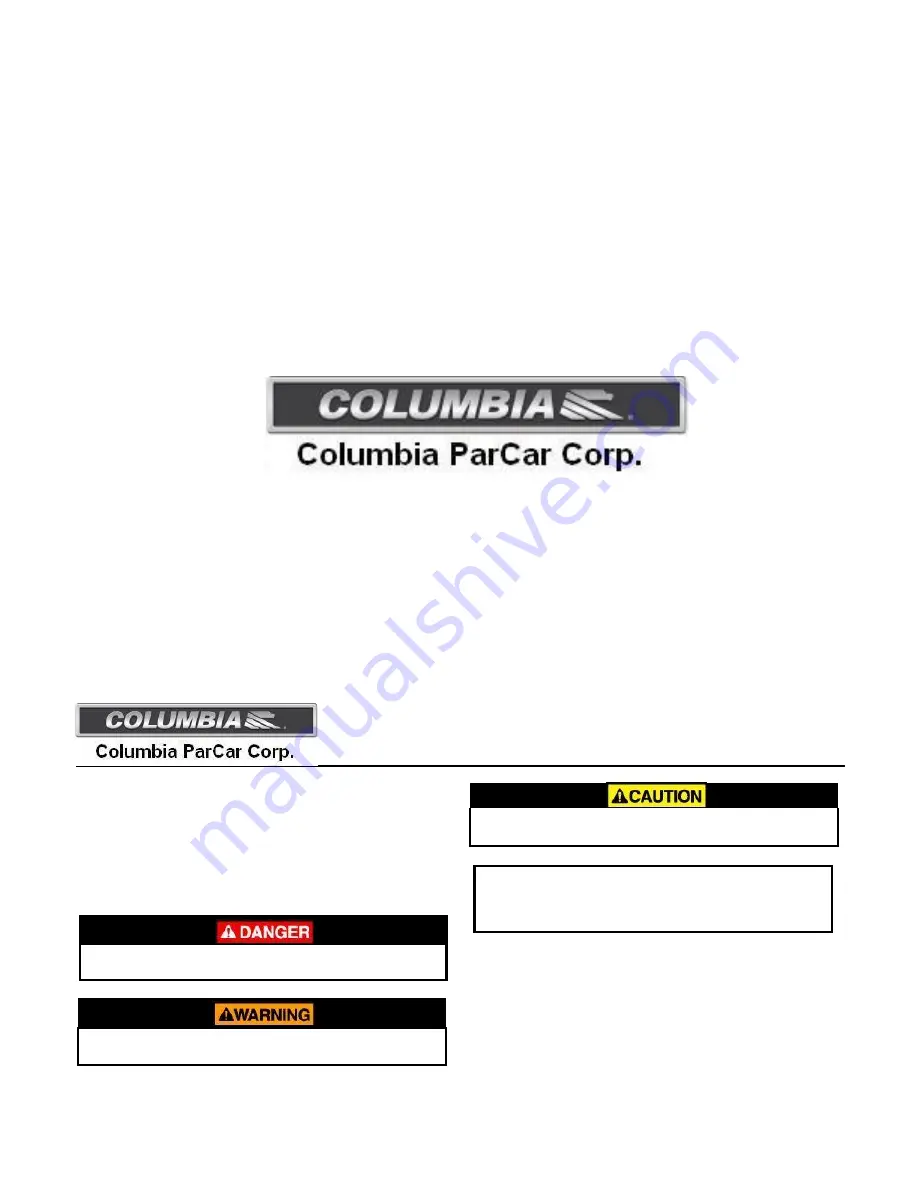
Service Manual
Section 1
Safety
OVERVIEW
Statements in this manual preceded by the words
DANGER,
WARNING, CAUTION or NOTICE
and words printed in
bold
face
are very important. We recommend you take special
notice of these items.
Danger indicates a hazardous situation which, if not
avoided, will result in death or serious injury.
Warning indicates a hazardous situation which, if not
avoided, could result in death or serious injury.
Caution indicates a hazardous situation which, if not
avoided, could result in minor or moderate injury.
NOTICE: Notices are messages not related to personal
injury. They will provide key information to prevent
property damage and to assure procedures are more
easily understood or implemented.
It is important to note that some warnings against the use of
specific service methods, which could damage the vehicle or
render it unsafe, are stated in this service manual. However,
please remember that these warnings are not all inclusive.
Since Columbia ParCar Corporation could not possibly know,
evaluate and advise servicing personnel of all possible ways in
which service might be performed or of the possible hazardous
Section 1 - Safety
Содержание Expediter EX21-24A
Страница 1: ...Columbia ParCar Corp SERVICE MANUAL Expediter EX21 24S EX21 24A EX21 48A 2013...
Страница 8: ...Service Manual Section 2 General Information...
Страница 13: ...Section 2 General Information...
Страница 27: ...Section 4 Troubleshooting Figure 4 7...
Страница 35: ...Section 5 Accelerator Brake System Figure 5 1 Figure 5 2...
Страница 44: ...Section 6 Front wheels Fork Steering 6 Install steering column guard...
Страница 45: ...Section 6 Front wheels Fork Steering Figure 6 5...
Страница 46: ...Section 6 Front wheels Fork Steering 6 4...
Страница 50: ...Section 6 Front wheels Fork Steering Service Manual Section 7 Rear Wheels Rear Suspension Axle Assembly...
Страница 51: ...Section 6 Front wheels Fork Steering 2013 EX 21 Service Manual...
Страница 56: ...Section 7 Rear Wheels Rear Suspension Axle Assembly Figure 7 4...
Страница 57: ...Section 7 Rear Wheels Rear Suspension Axle Assembly Figure 7 6...
Страница 60: ...Section 7 Rear Wheels Rear Suspension Axle Assembly...
Страница 67: ...Section 7 Rear Wheels Rear Suspension Axle Assembly...
Страница 70: ......
Страница 72: ...Figure 8 6 8 2...
Страница 83: ...Section 9 Battery and Battery Charger...
Страница 84: ...Service Manual Section 10 Traction Drive System TRACTION MOTOR MAINTENANCE...
Страница 89: ...Section 10 Traction Drive System Figure 10 10...
Страница 90: ...Section 10 Traction Drive System...