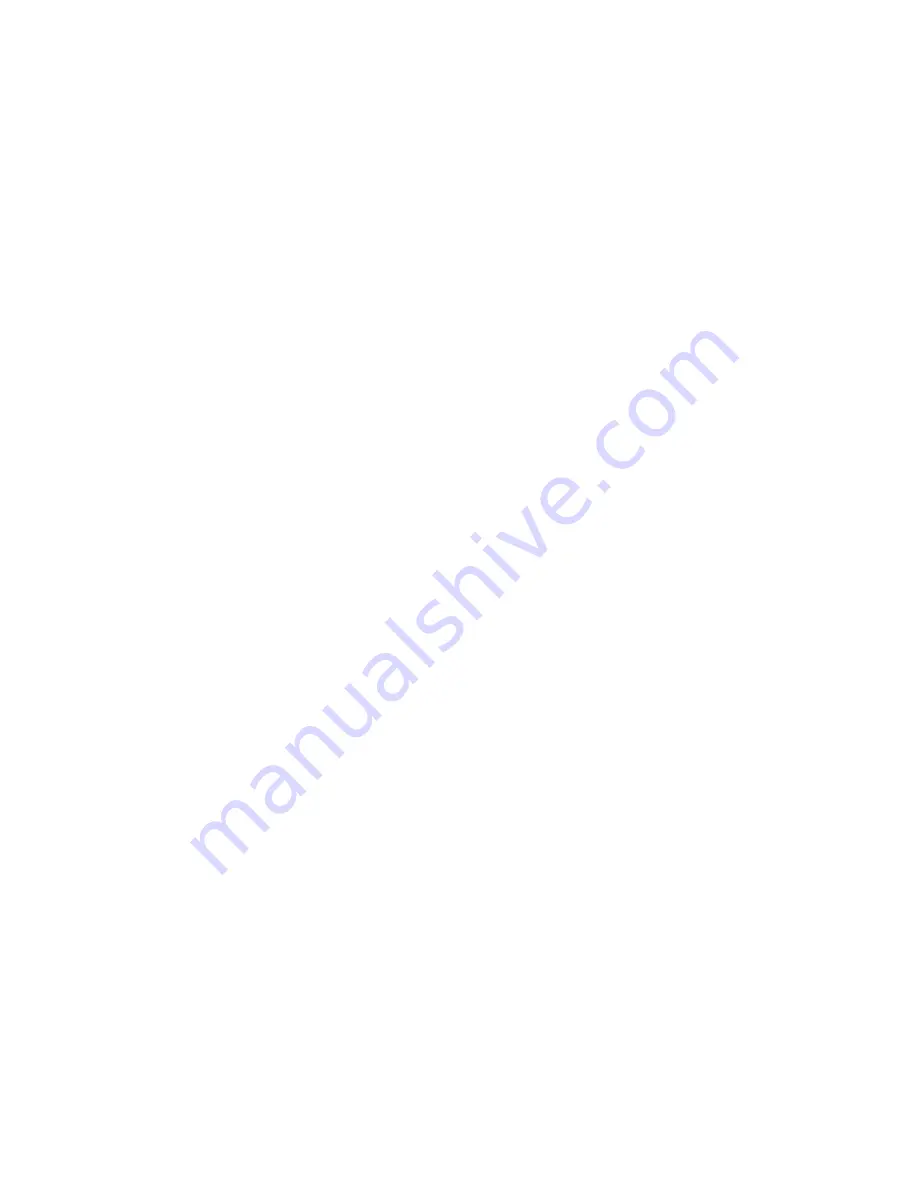
- 2 -
11. Configuration
15.1 Set value S and fixed temperatures F1 to F3 .........................
21
15.2 Adjusting the correction factors (RTA system) ......................
22
15.3 Displaying the operating software version ..............................
24
15.4 Secured mode ......................................................................
24
15.5 Adjusting the LED display contrast .......................................
24
15.6 Resolution of the temperature display ...................................
24
15.7 Adjusting temperature limit values .........................................
25
12. Fault Displays
12.1 Excess temperature .............................................................
26
12.2 Pump or motor overloading ....................................................
26
12.3 Sensor breakage or short circuit ...........................................
26
12.4 Undefined fault ......................................................................
27
12.5 Fault eliminated? ..................................................................
27
13. Testing the Safety Features
13.1 Excess temperature protection .............................................
27
14. Cooling
15. Maintenance
15.1 Cleaning the fins of the liquefier .............................................
29
15.2 Discarding the unit ................................................................
29
16. Technical Specifications
Содержание PolyStat CC1080
Страница 2: ...Blank page...
Страница 13: ...11 4 2 Menu tree...