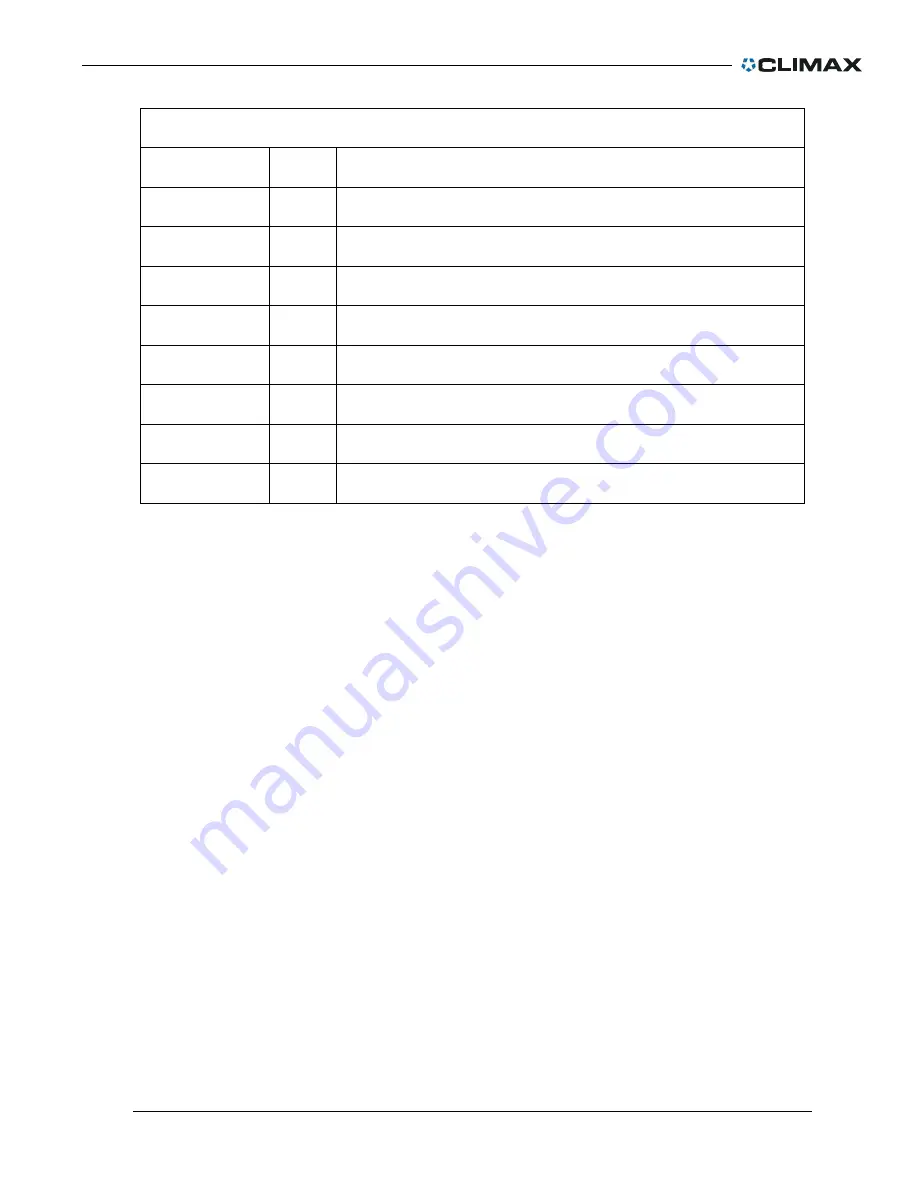
P/N 35425, Rev. 2
Page 29
35542 ASSY DRIVE PNEUMATIC FF4000
BALLOON No PART DESCRIPTION
1
18468 MOTOR AIR INGERSOLL 1.45HP 120 RPM @ MAX HP
2
33691 MUFFLER FF4000
3
36825 VALVE BALL 1/2 OVAL HANDLE ASSY W/ LABEL
4
35670 FTG SWIVEL 1/2 NPTM X 1/2 NPTF
5
13209 FTG QUICK COUPLER 1/2B 1/2 NPTM MALE AIR
NOT SHOWN 34866 AIRTOOL OIL COMPLETE
NOT SHOWN 13208 FTG QUICK COUPLER 1/2B 1/2 NPTF FEMALE AIR
NOT SHOWN 28826 PNEUMATIC CONDITIONING UNIT 1/2 IN
Содержание FF4000
Страница 2: ......
Страница 4: ...Page B FF4000 Operating Manual CLIMAX GLOBAL LOCATIONS ...
Страница 6: ...Page D FF4000 Operating Manual CE DOCUMENTATION LACEHOLDER FOR CE DECLARATION OF INCORPORATION ...
Страница 8: ...Page F FF4000 Operating Manual This page is intentionally left blank ...
Страница 34: ...Page 26 FF4000 Operating Manual FF4000 MAIN AS S EMBL Y ...
Страница 35: ...P N 35425 Rev 2 Page 27 ...
Страница 36: ...Page 28 FF4000 Operating Manual ...
Страница 38: ...Page 30 FF4000 Operating Manual ...
Страница 40: ...Page 32 FF4000 Operating Manual ...
Страница 43: ...P N 35425 Rev 2 Page 35 34936 FACING HEAD ASSEMBLY ...
Страница 45: ...P N 35425 Rev 2 Page 37 ...
Страница 46: ...Page 38 FF4000 Operating Manual ...
Страница 49: ......
Страница 50: ......