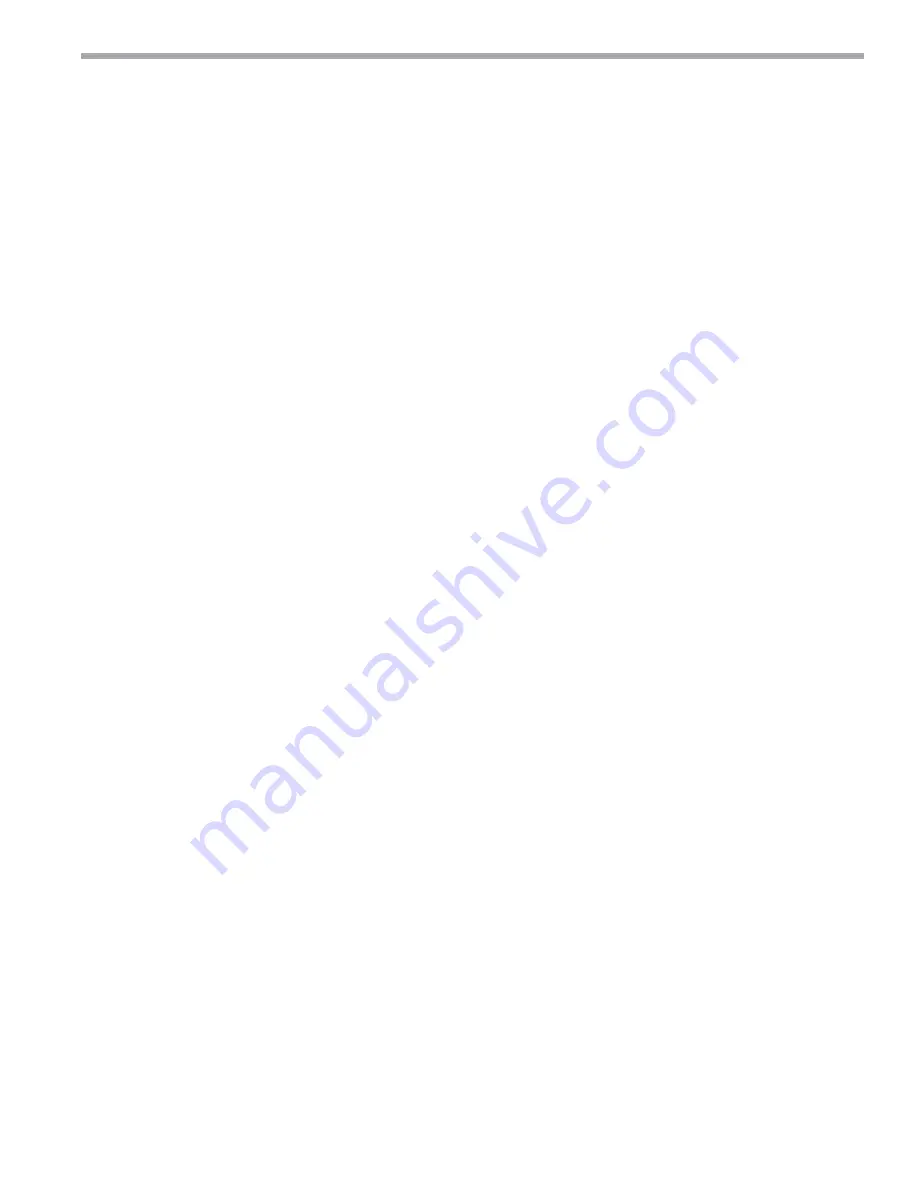
43
T H E S M A R T S O L U T I O N F O R E N E R G Y E F F I C I E N C Y
C o n s o l e s
R e v. : 5 N o v. , 2 0 0 9 B
c l i m a t e m a s t e r. c o m
Preventive Maintenance
Water Coil Maintenance
(Direct ground water applications only)
If the system is installed in an area with a known high
mineral content (125 P.P.M. or greater) in the water, it is
best to establish a periodic maintenance schedule with
the owner so the coil can be checked regularly. Consult
the well water applications section of this manual for
a more detailed water coil material selection. Should
periodic coil cleaning be necessary, use standard coil
cleaning procedures, which are compatible with the heat
exchanger material and copper water lines. Generally,
the more water
fl
owing through the unit, the less chance
for scaling. Therefore, 1.5 gpm per ton [2.0 l/m per kW]
is recommended as a minimum
fl
ow. Minimum
fl
ow rate
for entering water temperatures below 50°F [10°C] is 2.0
gpm per ton [2.6 l/m per kW].
Water Coil Maintenance
(All other water loop applications)
Generally water coil maintenance is not needed for
closed loop systems. However, if the piping is known to
have high dirt or debris content, it is best to establish a
periodic maintenance schedule with the owner so the
water coil can be checked regularly. Dirty installations
are typically the result of deterioration of iron or
galvanized piping or components in the system. Open
cooling towers requiring heavy chemical treatment and
mineral buildup through water use can also contribute
to higher maintenance. Should periodic coil cleaning be
necessary, use standard coil cleaning procedures, which
are compatible with both the heat exchanger material
and copper water lines. Generally, the more water
fl
owing through the unit, the less chance for scaling.
However,
fl
ow rates over 3 gpm per ton (3.9 l/m per kW)
can produce water (or debris) velocities that can erode
the heat exchanger wall and ultimately produce leaks.
Filters
Filters must be clean to obtain maximum performance.
Filters should be inspected every month under normal
operating conditions and be replaced when necessary.
Units should never be operated without a
fi
lter.
Washable, high ef
fi
ciency, electrostatic
fi
lters, when dirty,
can exhibit a very high pressure drop for the fan motor
and reduce air
fl
ow, resulting in poor performance. It is
especially important to provide consistent washing of
these
fi
lters (in the opposite direction of the normal air
fl
ow) once per month using a high pressure wash similar
to those found at self-serve car washes.
Condensate Drain
In areas where airborne bacteria may produce a “slimy”
substance in the drain pan, it may be necessary
to treat the drain pan chemically with an algaecide
approximately every three months to minimize the
problem. The condensate pan may also need to be
cleaned periodically to insure indoor air quality. The
condensate drain can pick up lint and dirt, especially
with dirty
fi
lters. Inspect the drain twice a year to avoid
the possibility of plugging and eventual over
fl
ow.
Compressor
Conduct annual amperage checks to insure that amp
draw is no more than 10% greater than indicated on the
serial plate data.
Fan Motors
All units have lubricated fan motors. Fan motors should
never be lubricated unless obvious, dry operation
is suspected. Periodic maintenance oiling is not
recommended, as it will result in dirt accumulating in the
excess oil and cause eventual motor failure. Conduct
annual dry operation check and amperage check to
insure amp draw is no more than 10% greater than
indicated on serial plate data.
Air Coil
The air coil must be cleaned to obtain maximum
performance. Check once a year under normal operating
conditions and, if dirty, brush or vacuum clean. Care
must be taken not to damage the aluminum
fi
ns while
cleaning. CAUTION: Fin edges are sharp.
Cabinet
Do not allow water to stay in contact with the cabinet
for long periods of time to prevent corrosion of the
cabinet sheet metal. The cabinet can be cleaned using a
mild detergent.
Refrigerant System
To maintain sealed circuit integrity, do not install service
gauges unless unit operation appears abnormal.
Reference the operating charts for pressures and
temperatures. Verify that air and water
fl
ow rates are at
proper levels before servicing the refrigerant circuit.