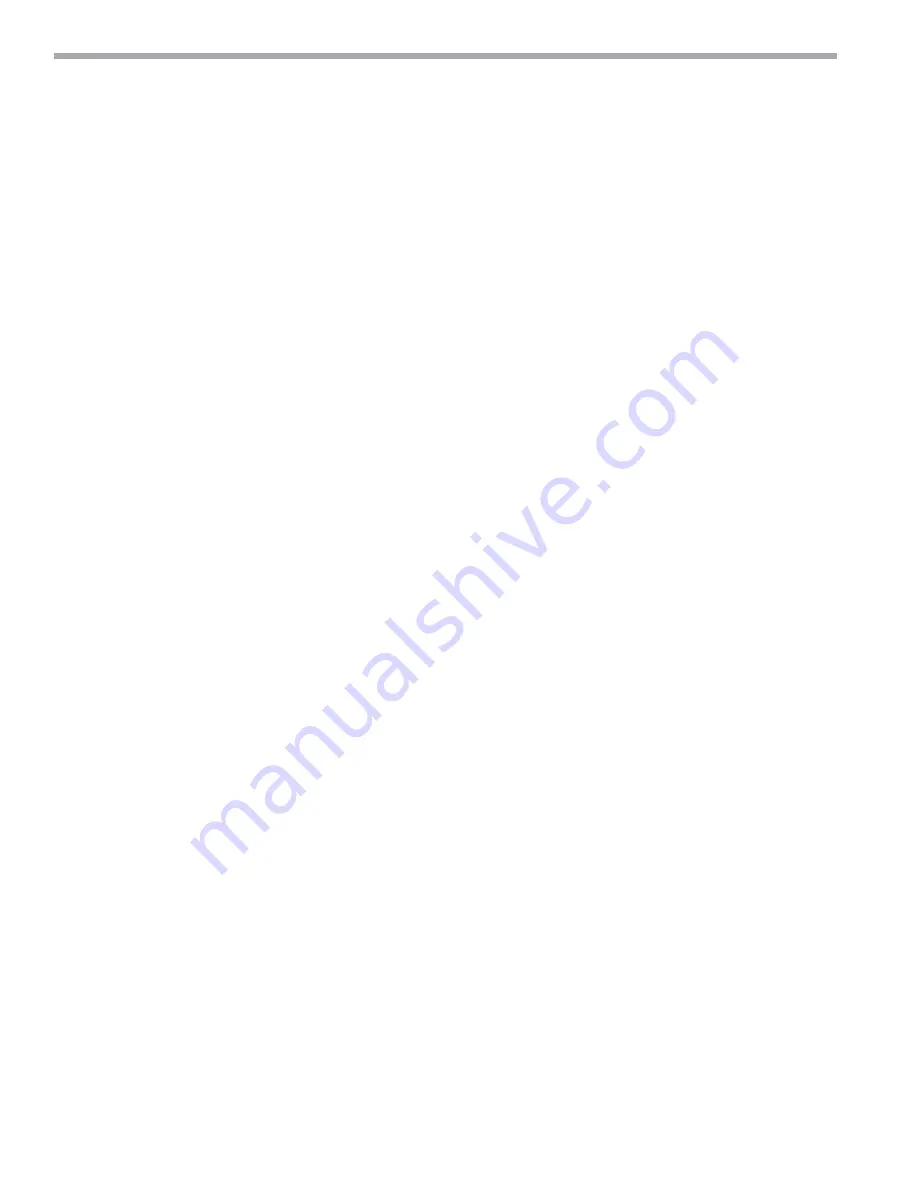
C L I M AT E M A S T E R W AT E R - S O U R C E H E AT P U M P S
C o n s o l e s
R e v. : 5 N o v. , 2 0 0 9 B
18
C l i m a t e M a s t e r W a t e r- S o u r c e H e a t i n g a n d C o o l i n g S y s t e m s
Open Loop - Ground Water Systems
Shut off valves should be included for ease of servicing.
Boiler drains or other valves should be “tee’d” into the
lines to allow acid
fl
ushing of the heat exchanger. Shut
off valves should be positioned to allow
fl
ow through
the coax via the boiler drains without allowing
fl
ow into
the piping system. P/T plugs should be used so that
pressure drop and temperature can be measured. Piping
materials should be limited to copper or PVC SCH80.
Note: Due to the pressure and temperature extremes,
PVC SCH40 is not recommended.
Water quantity should be plentiful and of good quality.
Consult table 3 for water quality guidelines. The unit can
be ordered with either a copper or cupro-nickel water
heat exchanger. Consult Table 3 for recommendations.
Copper is recommended for closed loop systems and
open loop ground water systems that are not high
in mineral content or corrosiveness. In conditions
anticipating heavy scale formation or in brackish water,
a cupro-nickel heat exchanger is recommended. In
ground water situations where scaling could be heavy
or where biological growth such as iron bacteria will
be present, an open loop system is not recommended.
Heat exchanger coils may over time lose heat exchange
capabilities due to build up of mineral deposits. Heat
exchangers must only be serviced by a quali
fi
ed
technician, as acid and special pumping equipment
is required. Desuperheater coils can likewise become
scaled and possibly plugged. In areas with extremely
hard water, the owner should be informed that the
heat exchanger may require occasional acid
fl
ushing.
In some cases, the desuperheater option should not
be recommended due to hard water conditions and
additional maintenance required.
Water Quality Standards
Table 3 should be consulted for water quality
requirements. Scaling potential should be assessed
using the pH/Calcium hardness method. If the pH
<7.5 and the calcium hardness is less than 100 ppm,
scaling potential is low. If this method yields numbers
out of range of those listed, the Ryznar Stability and
Langelier Saturation indecies should be calculated.
Use the appropriate scaling surface temperature for the
application, 150°F [66°C] for direct use (well water/open
loop) and DHW (desuperheater); 90°F [32°F] for indirect
use. A monitoring plan should be implemented in these
probable scaling situations. Other water quality issues
such as iron fouling, corrosion prevention and erosion
and clogging should be referenced in Table 3.
Expansion Tank and Pump
Use a closed, bladder-type expansion tank to minimize
mineral formation due to air exposure. The expansion
tank should be sized to provide at least one minute
continuous run time of the pump using its drawdown
capacity rating to prevent pump short cycling. Discharge
water from the unit is not contaminated in any manner
and can be disposed of in various ways, depending on
local building codes (e.g. recharge well, storm sewer,
drain
fi
eld, adjacent stream or pond, etc.). Most local
codes forbid the use of sanitary sewer for disposal.
Consult your local building and zoning department to
assure compliance in your area.
Water Control Valve
Always maintain water pressure in the heat exchanger
by placing the water control valve(s) on the discharge
line to prevent mineral precipitation during the off-cycle.
Pilot operated slow closing valves are recommended
to reduce water hammer. If water hammer persists, a
mini-expansion tank can be mounted on the piping
to help absorb the excess hammer shock. Insure that
the total ‘VA’ draw of the valve can be supplied by the
unit transformer. For instance, a slow closing valve can
draw up to 35VA. This can overload smaller 40 or 50
VA transformers depending on the other controls in the
circuit. A typical pilot operated solenoid valve draws
approximately 15VA..
Flow Regulation
Flow regulation can be accomplished by two methods.
One method of
fl
ow regulation involves simply adjusting
the ball valve or water control valve on the discharge
line. Measure the pressure drop through the unit heat
exchanger, and determine
fl
ow rate. Since the pressure is
constantly varying, two pressure gauges may be needed.
Adjust the valve until the desired
fl
ow of 1.5 to 2 gpm per
ton [2.0 to 2.6 l/m per kW] is achieved. A second method
of
fl
ow control requires a
fl
ow control device mounted
on the outlet of the water control valve. The device is
typically a brass
fi
tting with an ori
fi
ce of rubber or plastic
material that is designed to allow a speci
fi
ed
fl
ow rate.
On occasion,
fl
ow control devices may produce velocity
noise that can be reduced by applying some back
pressure from the ball valve located on the discharge line.
Slightly closing the valve will spread the pressure drop
over both devices, lessening the velocity noise.
NOTE:
When EWT is below 50°F [10°C], 2 gpm per ton (2.6
l/m per kW) is required.
Ground-Water Heat Pump Applications