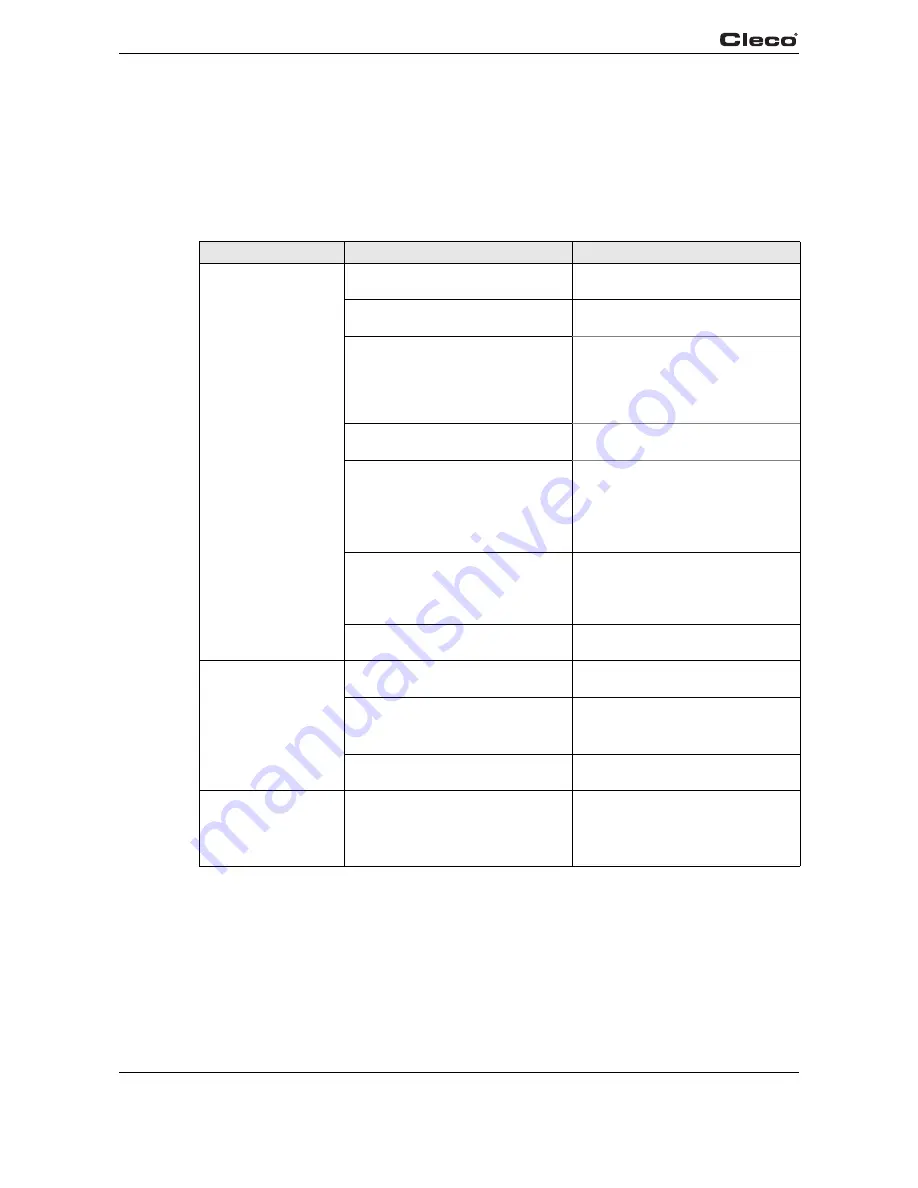
12
P1886E/EN 2008-07
86b_1_5 en bedingt.fm, 24.07.2008
Troubleshooting
5
4.5.3
Measuring the torque
We recommend carrying out a static torque measurement by retightening the rundown.
When carrying out a dynamic measurement using a transducer adapter, also carry out a static
test, for example using a torque wrench (electronic).
5
Troubleshooting
Error
Possible causes
Measures and remedies
Tool
does not shut off
Torque set too high
➔
Reduce the torque setting, see
4.5.1 Setting the torque, page 10.
Speed set too low
➔
Increase the speed, see 4.5.2
Changing the speed, page 11.
Working pressure < 58 psi (400 kPa)
➔
Check the cross section of the
hose and coupling: Inner
diameter 1/2" (ø 12,5 mm), maxi-
mum length 16.4 ft (5 m).
➔
Increase the working pressure.
Reverse button is
not at the detent
➔
Turn the reverse button
to the detent.
Excessive transmission damping due
to extension and worn socket
➔
Increase the speed, see 4.5.2
Changing the speed, page 11.
➔
Use a shorter or more rigid exten-
sion.
➔
Replace the socket.
Insufficient oil in the pulse unit (no
pulse build-up)
➔
See 6.2 Activating the reserve oil,
page 15.
➔
See 6.2 Activating the reserve oil,
page 15.
Screen in the air inlet tube /
muffler is dirty
➔
Clean or replace parts.
Insufficient shut-off
accuracy
Number of pulses too low: < 6
➔
Reduce speed,
number of pulses > 6.
Adapter parts
➔
Replace adapter parts.
➔
Use extension and socket with
guide diameter.
Pressure fluctuations in the air net-
work
➔
Use a pressure controller.
Fastening time too
long: > 4 seconds
Joint too soft; self-locking nuts, drive
screws
➔
Increase the speed.
➔
Use a pulse nutsetter with a
higher capacity.
➔
Use a mechanical screwdriver.