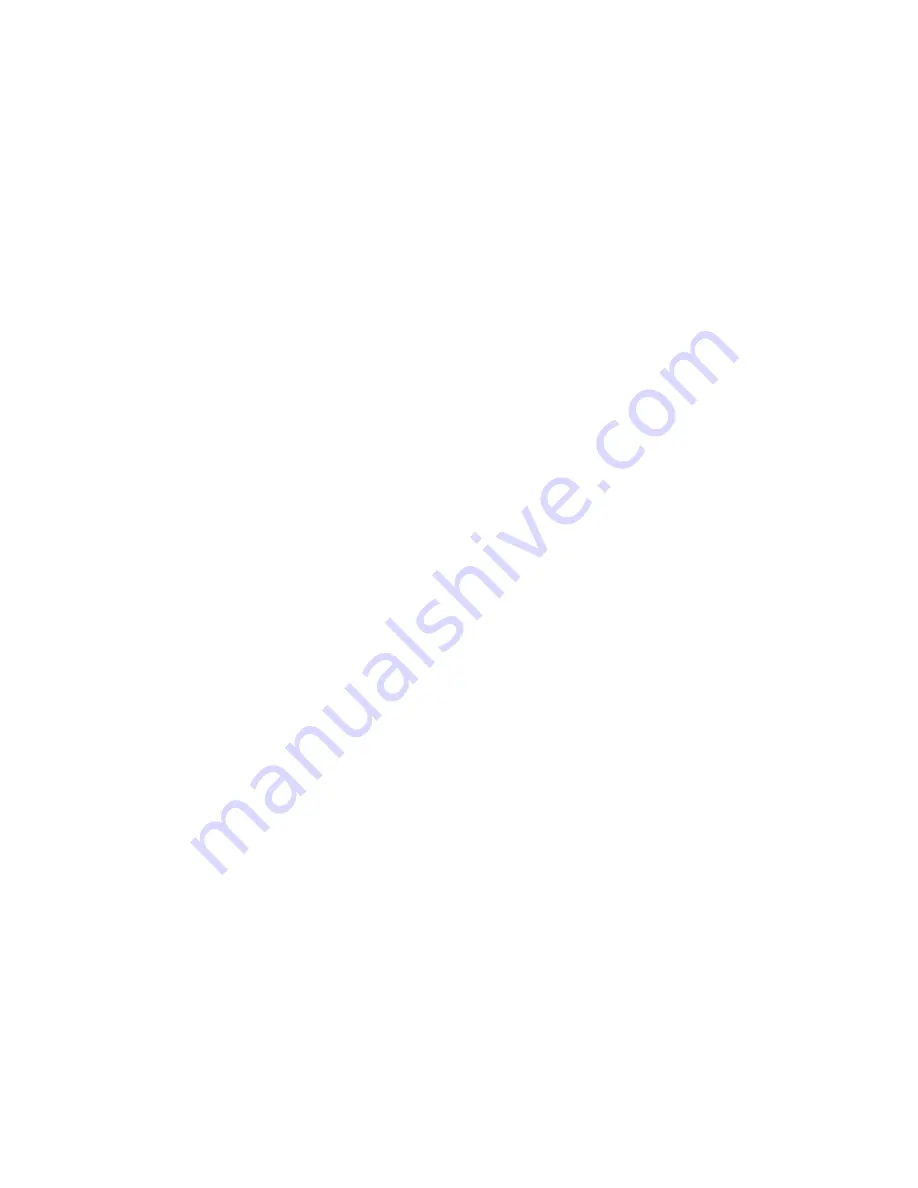
9
3-A Burn protection
Comply with precautions in 2. The welding arc is intense and visibly bright. Its radiation
can damage eyes, penetrate lightweight clothing, reflect from light coloured surfaces,
and burn the skin and eyes. Skin burns resemble acute sunburn, those from gas -
shielded arcs are more severe and painful.
DON’T GET BURNED! COMPLY WITH PRECAUTIONS!
(I) Protective clothing
Wear long sleeved clothing (particularly for gas shielded arc) in addition to gloves,
hat and shoes (2-A). As necessary, use additional protective clothing such as
leather jacket or sleeves, flameproof apron, and fire-resistant leggings. Avoid outer
garments of untreated cotton. Protect
bare skin. Wear dark substantial clothing.
Button collar to protect chest and neck and button pockets to prevent entry of
sparks.
(II) Eye and head protection
Protect eyes from exposure to arc. NEVER look at an electric arc without
protection. Welding helmet or shield containing a filter plate shade no. 12
or denser must be used when welding. Place over face before striking arc.
Protect filter plate with a clear cover plate. Cracked or broken helmet or
shield should NOT be worn; radiation can pass through to cause burns.
Cracked, broken, or loose filter plates must be replaced IMMEDIATELY.
Replace clear cover plate when broken, pitted, or spattered. WE
SUGGEST to wear flash goggles with side shields under the helmet, to give
some protection to the eyes should the helmet not be lowered over the
face before an arc is struck. Looking at an arc momentarily with
unprotected eyes (particularly a high intensity gas-shielded arc) can
cause a retinal burn that may leave a permanent dark area in the field of
vision. Before welding whilst wearing contact lenses, seek advice from
your optician.
(III) Protection of Nearby Personnel
For production welding, a separate room or enclosed bay is best. In open
areas, surround the operation with low reflective, non-combustible
screens or panels. Allow for free air circulation, particularly at floor level.
Provide face shields for all persons who will be looking directly at the weld.
Others working in the area should wear flash goggles. Before starting to
weld, make sure that screen or bay doors are closed.
3-B Toxic Fume Prevention
Comply with precautions in 2-B. Generator engine exhaust must be
vented to the outside air. Carbon monoxide can kill.
2-C Fire and explosion prevention
Causes of fire and explosion are: combustibles reached by the arc, flame, flying
sparks, hot slag or heated material; misuse of compressed gases and cylinders;
and short circuits. BE AWARE THAT flying sparks or falling slag can pass through
cracks, along pipes, through windows or doors, and through wall or floor openings,
out of sight of the goggled operator. Sparks and slag can fly 10m. To prevent fires and
explosion: keep equipment clean and operable, free of oil, grease, and (in electrical
parts) of metallic particles that can cause short circuits. If combustibles are in area,
do NOT weld or cut. Move the work if practicable, to an area free of combustibles.
Avoid paint spray rooms, dip tanks, storage areas, ventilators. If the work cannot be
moved, move combustibles at least 10m. away out of reach of sparks and heat; or
protect against ignition with suitable and snug fitting, fire- resistant covers or shields.
Walls touching combustibles on opposite sides should not be welded on (or cut).
Walls, ceilings, and floor near work should be protected by heat resistant covers or
shields. Fire watcher must be standing by with suitable fire extinguishing equipment
during and for some time after welding or cutting if:
a)
appreciable combustibles (including building construction) are within 10m.
b)
appreciable combustibles are further than 10m but can be ignited by sparks.
c)
openings (concealed or visible) in floors or walls within 10m can expose
combustibles to sparks.
d)
combustibles adjacent to walls, ceilings, roofs or metal partitions can be ignited
by radiant or conducted heat.
After work is done, check that area is free of sparks, glowing embers, and flames. An
empty container that held combustibles, or that can produce flammable or toxic
vapours when heated, must never be welded on or cut, unless container has first
been cleaned. This includes: a thorough steam or caustic cleaning (or a solvent or
water washing, depending on the combustible’s solubility) followed by purging and
inerting with nitrogen or carbon dioxide, and using protective equipment. Water filling
just below working level may substitute for inerting. A container with unknown contents
should be cleaned (see paragraph above), do NOT depend on sense of smell or sight
to determine if it is safe to weld or cut. Hollow castings or containers must be vented
before welding or cutting -they can explode. In explosive atmospheres, never weld or
cut where the air may contain flammable dust, gas, or liquid vapours (such as gasoline).
3.0 Electric arc (Mig, Tig) welding
Comply with precautions in 1, 2 and this section. Arc welding, properly
done, is a safe process, but a careless operator invites trouble. The
equipment carries high currents at significant voltages. The arc is very
bright and hot. Sparks fly, fumes rise, ultraviolet and infrared energy
radiates, weldments are hot. The wise operator avoids unnecessary risks
and protects himself and others from accidents.
Содержание Weld 215TE
Страница 1: ...1 Model Nos 215TE 250TE 260TE OPERATING MAINTENANCE INSTRUCTIONS 0100...
Страница 16: ...31 WIRING DIAGRAM MIG 260TE Part No 6010390...
Страница 17: ......