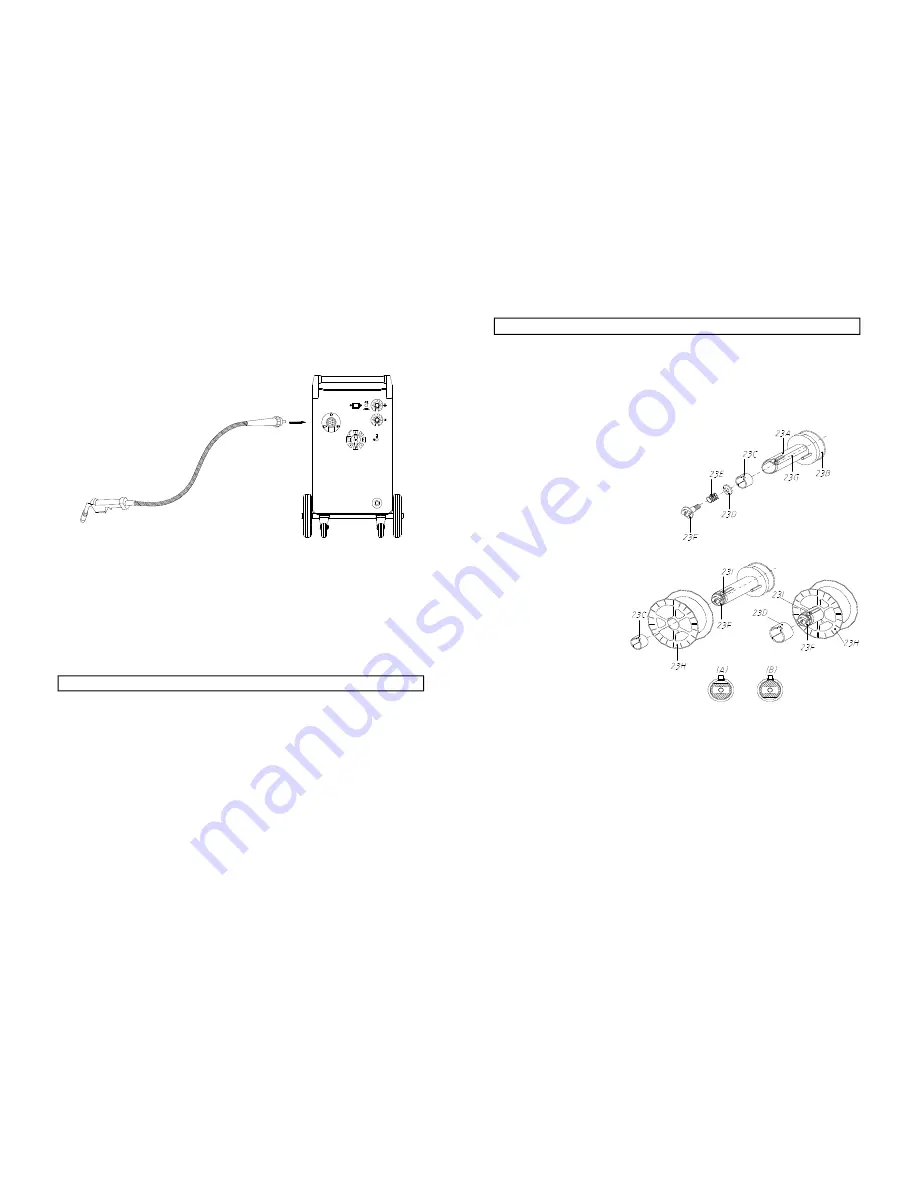
17
LOADING WIRE
NOTE:
These machines are designed to accept either 5Kg or 15Kg wire spools of
mild steel, stainless steel or aluminium according to the type of metal you wish to
weld. Wire spools ARE NOT supplied with the unit and must be purchased separately.
1 Ensure the gas and electrical supplies are disconnected;
2 (Ref. Fig. 3) Turn the plastic knob (23F), 180°.
3 Take off the plastic cover of the wire spool;
FIG.3
4 To fit the wire spool (23H)
into the hub (23A) push the
button (23I), insert the wire
spool, followed by the collar
(23C)(it must be used only
with 5Kg wire spools) .
5 Turn the plastic knob (23F)
by 180° again.
6 Loosen the plastic knob by
turning it anti-clockwise,
(this maintains pressure on
the wire via the roller). Pull,
on the plastic knob, so that
the screw rod comes out
of its slot, thereby
releasing the pivoted roller
bracket. Raise the bracket
together with the pressure
roller, and pullout any wire
that has been left in the
hose.
7 If you are changing the size of wire, you must also select the appropriate groove
on the feed roller. To change to the other groove, undo the Hex. Socket Screw and
remove the roller from its shaft. Turn it through 180°, replace it on the shaft, and
adjust so that the groove is directly in line with the Wire Liner. Firmly secure it in
that position with the Hex. Socket Screw.
8 Clip the end of the wire, on the spool, cleanly, ensuring there are no burrs or sharp
edges, and, ensuring it is straight, feed it through the guide tube , over the channel
on the roller and into the wire liner, by approx. 10 - 15cm.
FACE MASK
To assemble the face mask, first place the dark glass window and the clear glass
window together in the recessed window area of the body.
IMPORTANT: the clear glass window should be placed on the outside of the
mask.
Secure in place using the screws and nuts provided. Bend the sides of the mask into
shape and fix together using the screws and nuts provided, and finally, fit the handle
to the shield body also using the screws and nuts provided.
ATTACHING THE GAS BOTTLE AND REGULATOR
1.
The bottle (not supplied) should be located at the rear of the welder,
securely held in position by the chain provided.
2.
For safety, and economy, ensure that the regulator is fully closed, (turned
anti-clockwise) when not welding and when fitting or removing the gas cylinder.
3.
Connect the gas hose to the regulator securing with clip/nut provided.
4.
Screw the gas regulator fully down on the gas bottle valve, and fully tighten.
5.
Turn the power on, open the cylinder valve, then set the gas flow to approx. 8l/
min. on the regulator. Operate the torch trigger to ensure that the gas is flowing
through the torch.
TORCH LEAD ASSEMBLY INSTRUCTIONS
Plug the troch hose into the socket on the front of the welder and secure by hand
screwing in the threaded connection.
FIG.2
Содержание Weld 215TE
Страница 1: ...1 Model Nos 215TE 250TE 260TE OPERATING MAINTENANCE INSTRUCTIONS 0100...
Страница 16: ...31 WIRING DIAGRAM MIG 260TE Part No 6010390...
Страница 17: ......