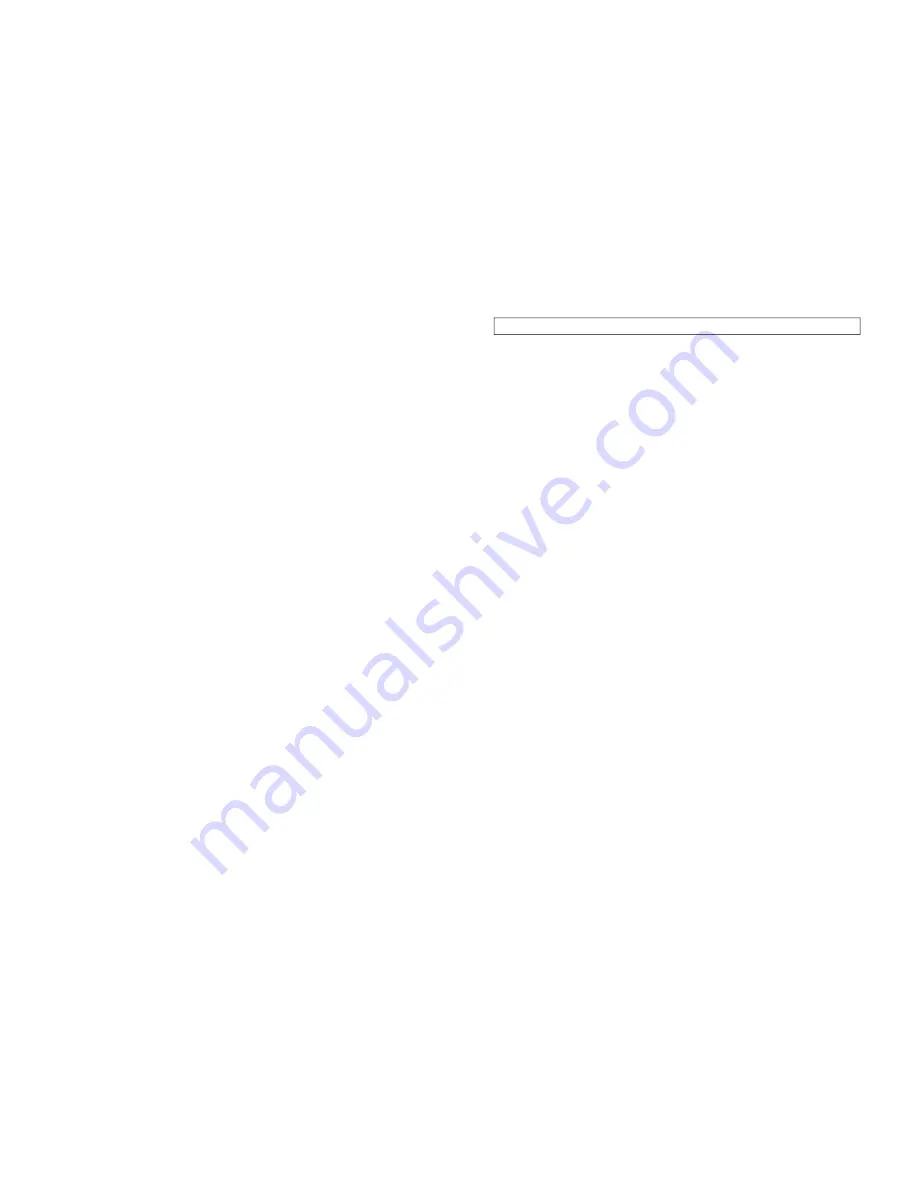
7
SAFETY PRECAUTIONS
1.0 Introduction
Read and understand these safe practices before attempting to install, operate, or
service the equipment. Comply with these procedures as applicable to the particular
equipment used and their instruction manuals, for personal safety and for the safety
of others. Failure to observe these safe practices may cause serious injury or death.
When safety becomes a habit, the equipment can be used with confidence.
2.0 General precautions
2-A Burn prevention
Wear protective clothing - gauntlet gloves designed for use in welding, hat, and protective
shoes. Button shirt collar and pocket flaps, and wear cuffless trousers to avoid entry of
sparks and slag. Wear helmet with safety goggles or glasses with side shields underneath,
appropriate filter lenses or plates (protected by clear cover glass). This is a MUST for
welding or cutting, (and chipping) to protect the eyes from radiant energy and flying
metal. Replace cover glass when broken, pitted, or spattered. Avoid oily greasy clothing.
A spark may ignite them. Hot metal such as electrode stubs and workpieces should
never be handled without gloves. First aid facilities and a qualified first aid person should
be available for each shift unless medical facilities are close by for immediate treatment
of flash burns of the eyes and skin burns. Ear plugs should be worn when working
overhead or in a confined space. A hard hat should be worn when others work overhead.
Flammable hair preparations should not be used by persons intending to weld or cut.
2-B Toxic fume prevention
Severe discomfort, illness or death can result from fumes, vapours, heat, or oxygen
enrichment or depletion that welding (or cutting) may produce. Prevent them with adequate
ventilation. NEVER ventilate with oxygen. Lead-, cadmium-, zinc-, mercury- and beryllium-
, bearing materials, when welded (or cut) may produce harmful concentrations of toxic
fumes. Adequate local exhaust ventilation must be used, or each person in the area as
well as the operator must wear an air- supplied respirator. For beryllium, both must be
used. Metals coated with or containing materials that emit toxic fumes should not be
heated unless coating is removed from the work surface, the area is well ventilated, or
the operator wears an air-supplied respirator. Work in a confined space only while it is
being ventilated and, if necessary, while wearing an air-supplied respirator. Vapours
from chlorinated solvents can be decomposed by the heat of the arc (or flame) to form
PHOSGENE, a highly toxic gas, and other lung and eye irritating products. The ultraviolet
(radiant) energy of the arc can also decompose trichloroethylene and perchlorethylene
vapours to form phosgene. DO NOT WELD or cut where solvent vapours can be drawn
into the welding or cutting atmosphere or where the radiant energy can penetrate to
atmospheres containing even minute amounts of trichloroethylene or perchlorethylene.
2.3Welding cables
The welding cables should be kept as short as possible and should be positioned
close together, running at or close to the floor level.
2.4Equi-potential bonding
Bonding of all metallic components in the welding installation and adjacent to it
should be considered. However, metallic components bonded to the work piece will
increase the risk that the operator could receive a shock by touching these metallic
components and the electrodes at the same time. The operator should be insulated
from all such bonded metallic components.
2.5 Earthing of the workpiece
Where the workpiece is not bonded to earth for electrical safety, nor connected to
earth because of its size and position, e.g. ships hull orn building steelwork, a
connection bonding the workpiece to earth may reduce emissions in some, but not
all instances. Care should be taken to prevent the earthing of the workpiece increasing
the risk of injury to users, or damage to other electrical equipment. Where necessary,
the connection of the workpiece to earth should be made by a direct
connection to the workpiece, but in some countries where direct connection is not
permitted, the bonding should be achieved by suitable capacitance, selected according
to national regulations.
2.6 Screening and shielding
Selective screening and shielding of other cables and equipment in the
surrounding area may alleviate problems of interference. Screening of
the entire welding installation may be considered for special applications.
Содержание Weld 215TE
Страница 1: ...1 Model Nos 215TE 250TE 260TE OPERATING MAINTENANCE INSTRUCTIONS 0100...
Страница 16: ...31 WIRING DIAGRAM MIG 260TE Part No 6010390...
Страница 17: ......