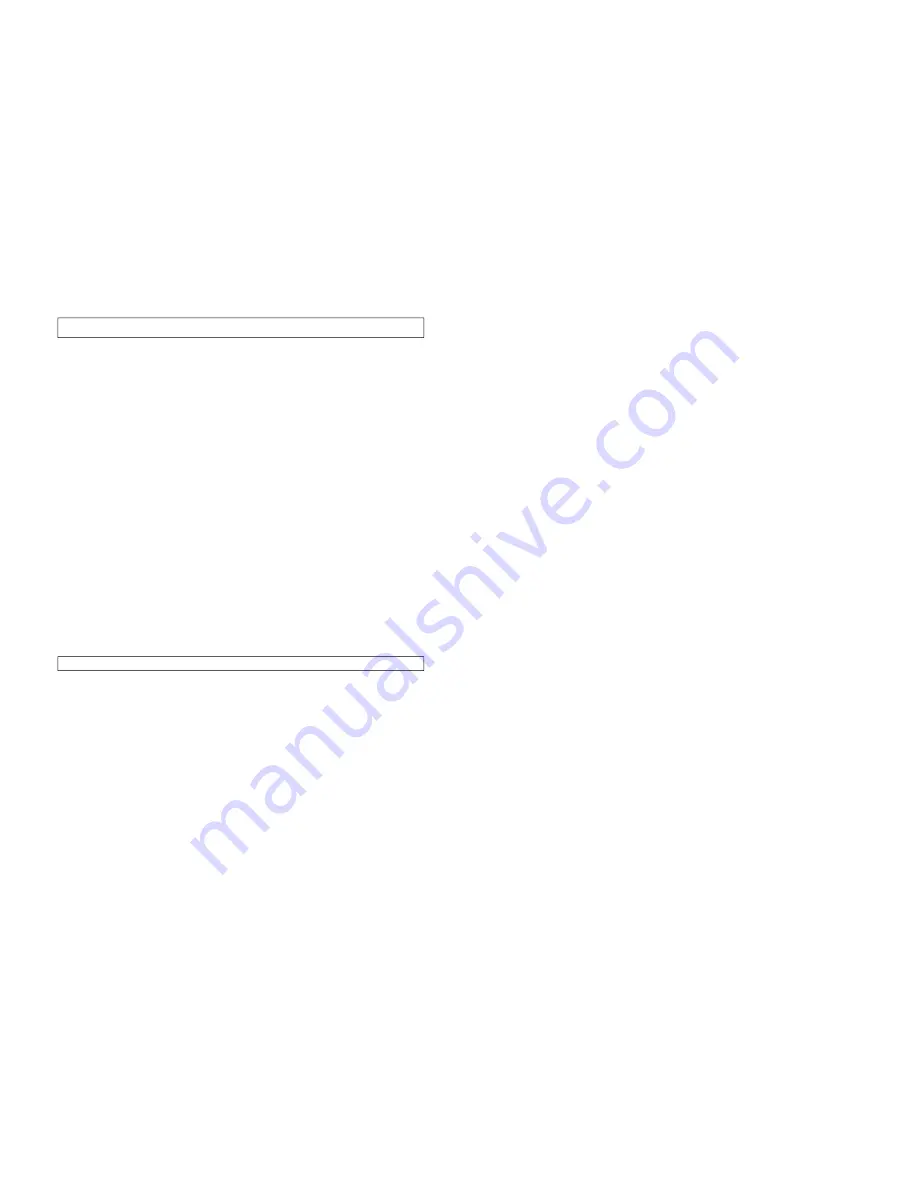
5
1. ASSESSMENT OF AREA
Before installing welding equipment the user shall make an assessment of potential
electromagnetic problems in the surrounding area. Avoid using your welder in the
vicinity of:
a)
Other supply cables, control cables, signalling and telephone cables; above, below
and adjacent to the welding equipment;
b)
Radio and television transmitters and receivers;
c)
Computer and other control equipment;
d)
Safety critical equipment, e.g. guarding of industrial equipment;
e)
Pacemakers and hearing aids etc;
f)
Equipment used for calibration or measurement;
g)
Other equipment in the environment. The user shall ensure that other equipment
being used in the environment is compatible. This may require additional protection
measures;
It may be possible to avoid the above by changing the time of day that welding or
other activities are to be carried out.
The size of the surrounding area to be considered will depend on the structure of the
building and other activities that are taking place. The surrounding area may extend
beyond the boundaries of the premises.
2. METHODS OF REDUCING EMISSIONS
2.1Mains supply
Welding equipment should be connected to the mains supply according to the
manufacturers recommendations. If interference occurs, it may be necessary to take
additional precautions such as filtering of the mains supply. Consideration should be
given to shielding the supply cable of permanently installed welding equipment, in
metallic conduit or equivalent. Shielding should be electrically continuous throughout
its length. The shielding should be connected to the welding power source so that
good electrical contact is maintained between the conduit and the welding power
source enclosure.
2.2Maintenance of the welding equipment
The welding equipment should be routinely maintained according to the manufacturers
recommendations. All access and service doors and covers should be closed and
properly fastened when the welding equipment is in operation. The welding equipment
should not be modified in any way except for those changes and adjustments covered
in the manufacturers instructions. In particular, the spark gaps of arc striking and
stabilizing devices should be adjusted and maintained according to the manufacturers
recommendations.
SAFETY
Special care is taken during all stages of manufacture to ensure that your Clarke Mig
Welder arrives with you in good condition.
Before using the machine it is in your own interest to read this manual thoroughly,
paying particular attention to the following rules, and the EMC Regulations:
1
Do not open or remove side panels from the machine unless the mains plugs
disconnected.
2
Do not use the machine with any of the panels open or removed.
3
Do not try to attempt any electrical or mechanical repair unless you are a
qualified technician. If you have a problem with your machine contact your
local dealer or CLARKE International Service Dep’t on 020 8988 7400.
4
Remove any flammable materials from the welding area.
5
Do not expose gas cylinder to high temperature, and do not strike an arc near
or on the gas cylinder.
Caution: Gas cylinders are pressurised containers. Do not pierce or burn, even when
empty. Protect from direct sunlight.
6
Make sure you have good ventilation in the welding area since toxic gases are
released during the MIG welding process.
7
Ultra-violet radiation is released by the MIG welding process and it is of the
utmost importance that the operator, and any spectators, protect themselves
by using welding face-shields or helmets with suitable filter lenses. The wearing
of gloves and proper working clothes is also strongly recommended.
8
Never use in a wet or damp environment.
9
If welding outdoors, screens MUST BE USED around the weld site, to protect
the general public from the glare of the arc.
ELECTROMAGNETIC INTERFERENCE (EMC)
Whilst this unit complies with EMC regulations, the user is responsible for installing
and using the welding equipment according to the manufacturers instructions. If
electromagnetic disturbances are detected then it shall be the responsibility of the
user of the welding equipment to resolve the situation. In some cases this remedial
action may be as simple as earthing the welding circuit, see ‘Note’. In other cases it
could involveconstructing an electromagnetic screen enclosing the power source
and the work complete with associated input filters. In all cases electromagnetic
disturbances must be reduced to the point where they are no longer troublesome.
NOTE: The welding circuit may not be earthed for safety reasons. Changing the
earthing arrangements should only be authorised by a person who is competant to
assess whether changes will increase the risk of injury, e.g. by allowing parallel
welding current return paths which may damage the earthing circuits of other
equipment.
Содержание Weld 215TE
Страница 1: ...1 Model Nos 215TE 250TE 260TE OPERATING MAINTENANCE INSTRUCTIONS 0100...
Страница 16: ...31 WIRING DIAGRAM MIG 260TE Part No 6010390...
Страница 17: ......