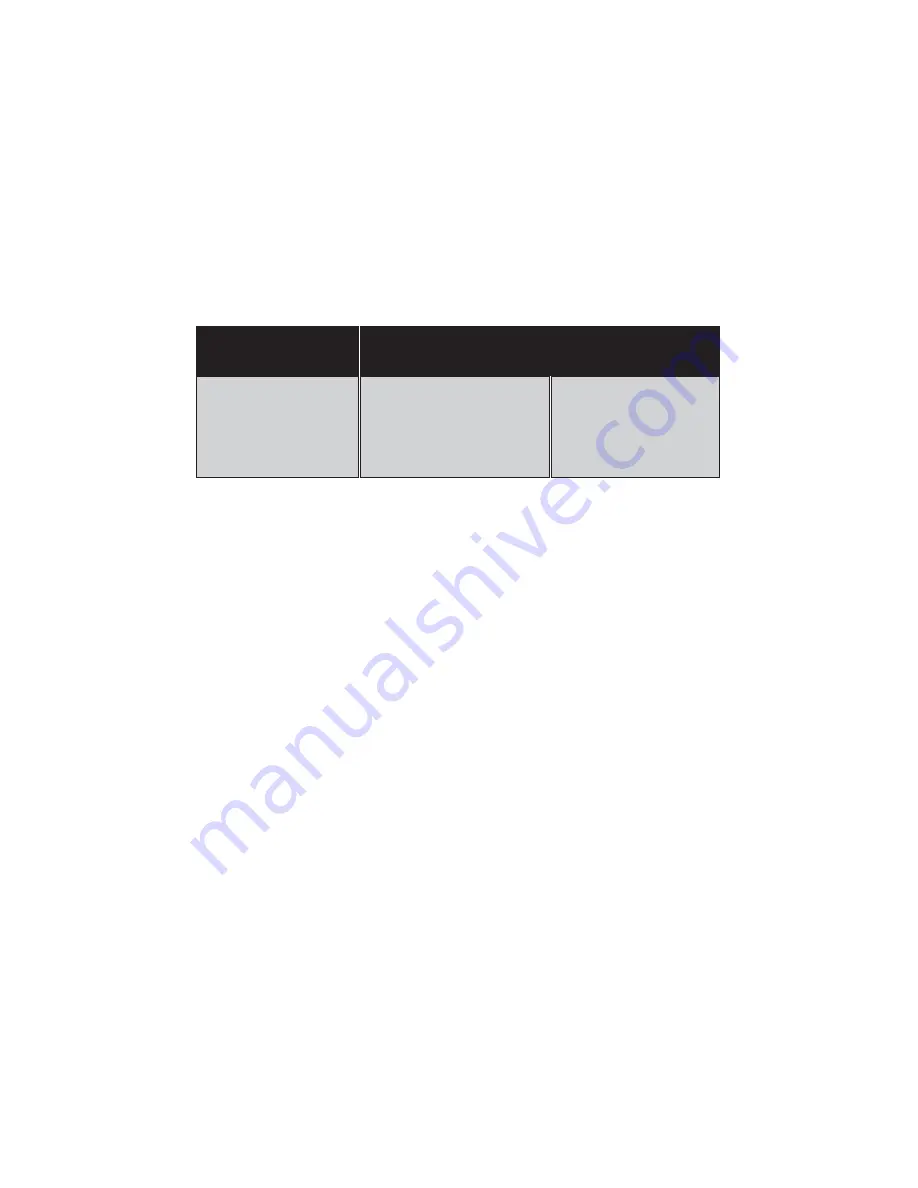
18
3. An appropriate current must then be set by turning the Welding Current Selector
located on the front panel o the machine. With practice you will gain a feel for the
correct current setting for different welding rod thicknesses.
The size (diameter) of welding rod should be approximately the same as the
thickness of metal to be welded.
For beginners, the following table gives some useful guidelines.
SIZE OF
THICKNESS
CURRENT
WELDING ROD
OF WORKPIECE
SETTING (AMPS)
1.5mm
16 SWG - 1.5 MM.
30 - 40
2.0mm
14 SWG - 2.0 MM.
50 - 65
2.5mm
12 SWG - 2.5 MM.
70 - 100
3.0mm
10 SWG - 3.25MM
100 - 130
4.
Switch ON using the switch located on the rear panel. The green light on the
front panel should glow, indicating the machine is ON.
Note: If the machine stops at any time and the amber light comes ON the
thermal overload has intervened
5. The most difficult aspect of the arc welding process, particularly for beginners,
is that of striking an arc. We strongly recommend that you practice on some
pieces of scrap metal to get the feel of the operation, before you start on an
actual welding job.
6. Hold the electrode about 10mm. from the work and at an angle of about
70
°
to 80
°
to the work surface; take care not to accidentally touch the workpiece
until you are ready to commence.
7. Holding the welding mask close-up to the face, give a short stroke with the
electrode on the workpiece. As soon as the arc is primed, withdraw the
electrode from the workpiece to leave a tiny gap of around 1.5mm (1/16").
The current will flow across the gap with a crackling noise and brilliant arc.
Continue to weld in one direction, maintaining the small gap as you go. At
the end of the run just withdraw the electrode fully from the workpiece.
Note: When you prime the arc be sure to withdraw the electrode fairly swiftly
to leave the 1.5mm. gap, otherwise the electrode will weld itself to the
workpiece. Should this occur give the electrode a short sharp jerk to free it
and, if necessary prime the arc again. If you cannot free the electrode, switch
the machine off immediately, and free it off.
8. Inspect the job carefully. With a correct combination of rod size and current
setting, the area of the weld should be a complete fusion of the electrode
metal with the metals being joined. Slag forming on the surface should be
chipped away with a chipping hammer or pick. ALWAYS wear your safety
goggles when chipping away slag.
Содержание 6012200
Страница 23: ...PARTS DIAGRAM ARC TIG 85 110 23...
Страница 24: ...PARTS DIAGRAM ARC TIG155 24...
Страница 25: ...25 WIRING DIAGRAM ARC TIG155 ARC TIG 85 110...
Страница 28: ......