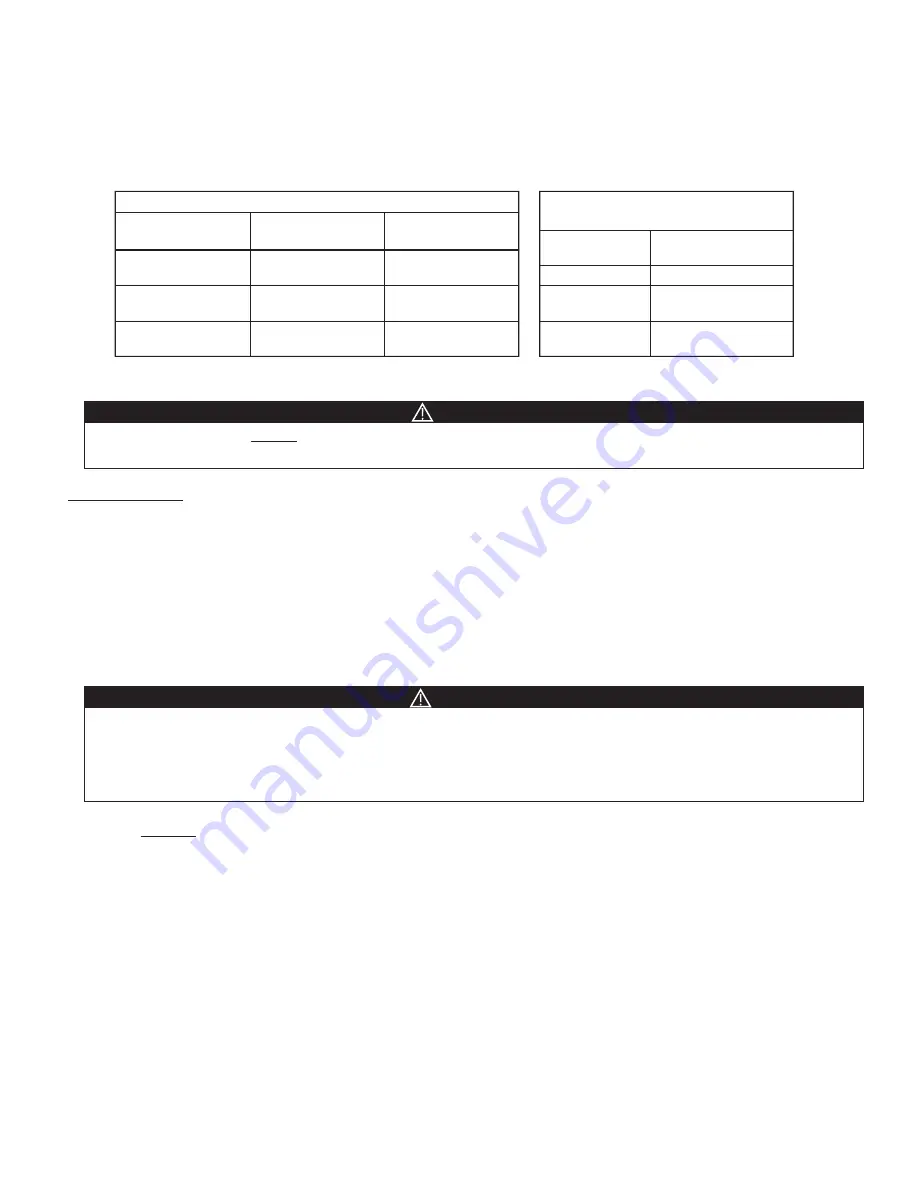
OMM-23-1009-page 5
F. Set Screw and Taper-lock Bushing Torque Values:
All blower wheel set screws are tightened to the proper torque prior to shipment. Some wheels may have taper-lock
hubs and split, taper-lock bushings to secure the wheel to the motor shaft.
NOTE:
Check all set screw or taper-lock bushing torques. Forces encountered during shipment, handling, rigging
and temperature can affect factory settings. For correct torque values, see
Tables 1
and
2
below.
Set screws should NEVER be used more than once. If the set screws are loosened, they MUST be replaced.
Use only knurled, cup-point, set screws with a nylon locking patch.
CAUTION
ALL WIRING CONNECTIONS, INSPECTION AND MAINTENANCE OF ANY MOTOR MUST BE PERFORMED BY A
LICENSED ELECTRICIAN IN ACCORDANCE WITH THE MOTOR MANUFACTURERS RECOMMENDATIONS, ALL
ELECTRICAL CODES AND OSHA REGULATIONS. FAILURE TO PROPERLY INSTALL, MAKE WIRING
CONNECTIONS, INSPECT OR PERFORM ANY MAINTENANCE TO A MOTOR CAN RESULT IN
MOTOR FAILURE, PROPERTY DAMAGE, EXPLOSION, ELECTRICAL SHOCK AND DEATH.
DANGER
III. ELECTRICAL
A. Disconnect Switches:
All blower motors should have an independent disconnect switch located in close visual proximity to turn off the elec-
trical service to the blower motor.
Disconnects must be locked out in accordance with OSHA “lock out-tag out”
procedures any time inspection or maintenance is being performed on the blower and/or motor assembly.
The “lock out-tag out” procedure should be performed by a licensed electrician or authorized personnel.
All disconnects should be sized in accordance with the latest NEC codes (National Electric Codes) and any local
codes and should be installed only by a licensed electrician. “Slow blow” or “time delay” fuses or breakers should be
used since the initial start-up time for the blower motor, although rare, can be up to 10 seconds.
B. Motors:
1.
DO NOT connect or operate a motor without reading the motor manufacturers instructions supplied with
the blower.
The basic principle of motor maintenance is:
KEEP THE MOTOR CLEAN AND DRY.
This requires
periodic inspections of the motor. The frequency of the inspections depends on the type of motor, the service and
environment it will be subjected to and the motor manufacturers instructions.
2. Cleaning:
Cleaning should be limited to exterior surfaces only.
Follow motor manufacturers cleaning instruc-
tions.
3. Lubrication:
Most small motors have sealed bearings that are permanently lubricated for the life of the motor.
Some larger motors have grease plugs that should be replaced with grease fittings to perform re-lubrication.
These motors, or any motor with grease fittings, should be lubricated in accordance with the motor manufacturers
recommendations. Lubrication frequency depends on the motor horsepower, speed and service.
BE SURE
you
use compatible grease and
DO NOT
over grease.
4. Location:
If the motor will be outside and subjected to the weather, it is recommended that a weather cover be
installed to keep rain and snow off of the motor. No motors are guaranteed to be “watertight”. Be careful to allow
enough openings between the motor and the motor cover to let the motor ”breath”. If the back end of the motor is
covered, the cover should be no closer than 3” to the back of the motor for proper ventilation.
SET SCREW TORQUE VALUES
TORQUE VALUES FOR
TAPER-LOCK BUSHINGS
Diameter & Number
of Treads/Inch
Hex Wrence Size
(Across Flats)
Required Torque
(Inch Pounds)
1/4-20
5/16-18
3/8-16
7/16-14
1/2-13
5/8-11
1/8”
5/32”
3/16”
7/32”
1/4”
5/16”
65
165
228
348
504
1104
Taper-lock
Bushing Size
Required Torque
(Inch Pounds)
H
B
P
Q
R
95
192
192
350
350
Table 2
Table 1