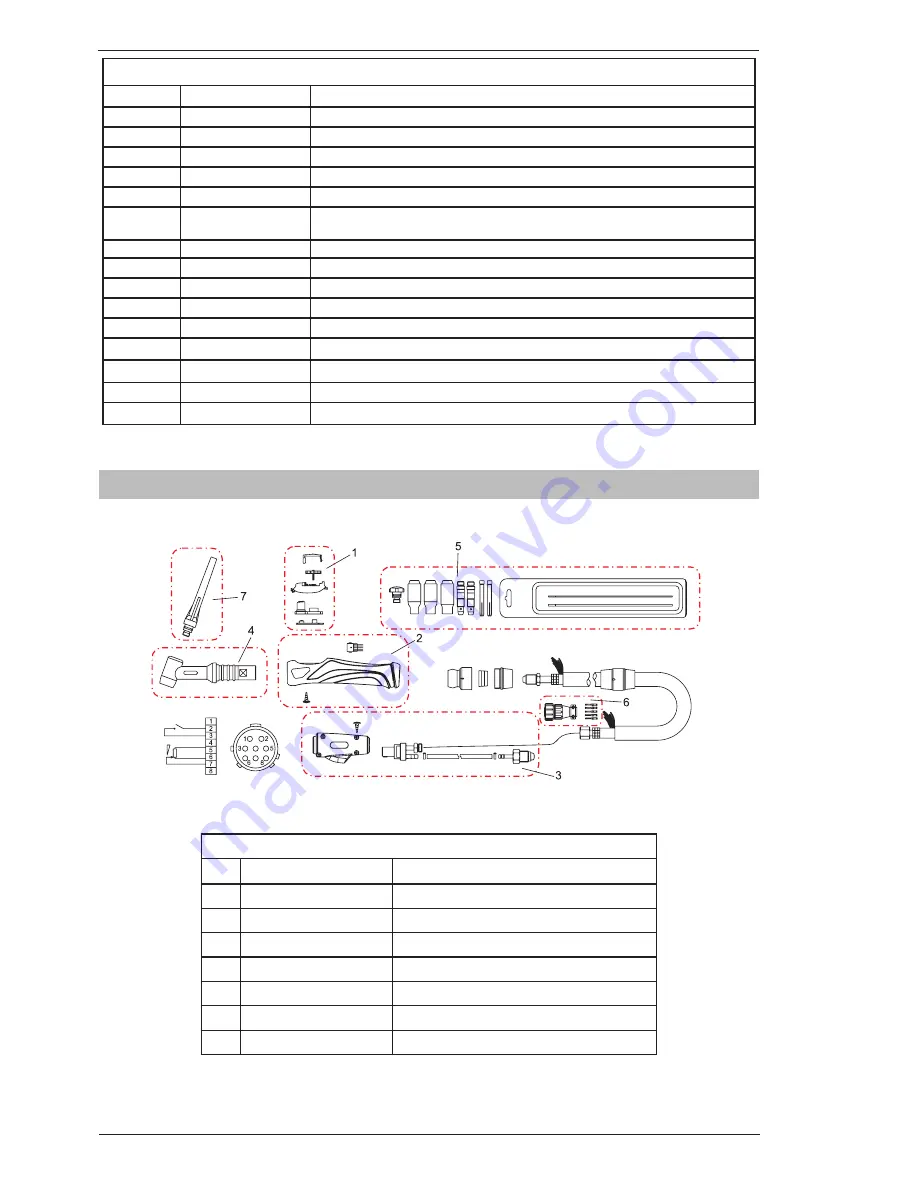
TRANSARC 170i
KEY SPARE PARTS
9-2
Manual 0-5280
TRANSARC 170i POWER SOURCE SPARE PARTS
ITEM
PART NUMBER
DESCRIPTION
1
W7005800
PCB Power
2
W7005801
PCB Control
3
W7005803
PCB Front Panel (Display) 170i
4
W7005805
Knob Control
5
W7004909
Dinse Socket 50mm
2
6
W7005811
Control Socket 8 pin (Note that 8 pin control plug is part number
UOA706900)
7
W7005812
Shielding Gas Outlet 5/8-18
8
W7005814
CT Output
9
W7004908
Shielding Gas Solenoid Valve Assembly
10
W7005605
Shielding Gas Inlet Quick Connect
11
W7005813
Input Supply On/Off Switch
12
W7004913
Shielding Gas Hose Assembly (not supplied)
13
W7005806
Fan Assembly
14
W7003010
Input Rectifier (Shown mounted to PCB Power, item 1)
15
704461
Dinse Plug Male 50mm
2
(not shown)
Table 9-1
9.02 TIG Torch W4014604 (where supplied)
TIG Torch W4014604 spare parts diagram
A-11669
Figure 9-2
TIG TORCH SPARE PARTS
ITEM
PART NO.
DESCRIPTION
1
W7005900
Trigger assembly for 26F torch
2
W7005901
Handle assembly for 26F torch
3
W7005902
Dinse 50mm for 26F torch
4
W7005903
Flex head for 26F torch
5
BGSAK2
Tig accessory Kit
6
UOA706900
Cable Plug 8 pin
7
BG57Y02/R
Back Cap (Long)
Table 9-2
Содержание TRANSarc 130i
Страница 6: ......
Страница 18: ...INTRODUCTION 2 2 Manual 0 5280 transarc 170i Notes...
Страница 42: ...Theory of Operation 5 2 Manual 0 5280 TRANSARC 170i Notes...
Страница 68: ...TRANSARC 170i DISASSEMBLY PROCEDURE 7 8 Manual 0 5280 Notes...
Страница 76: ...ASSEMBLY PROCEDURES 8 8 Manual 5280 TRANSARC 170i Notes...
Страница 80: ...TRANSARC 170i KEY SPARE PARTS 9 4 Manual 0 5280 Notes...