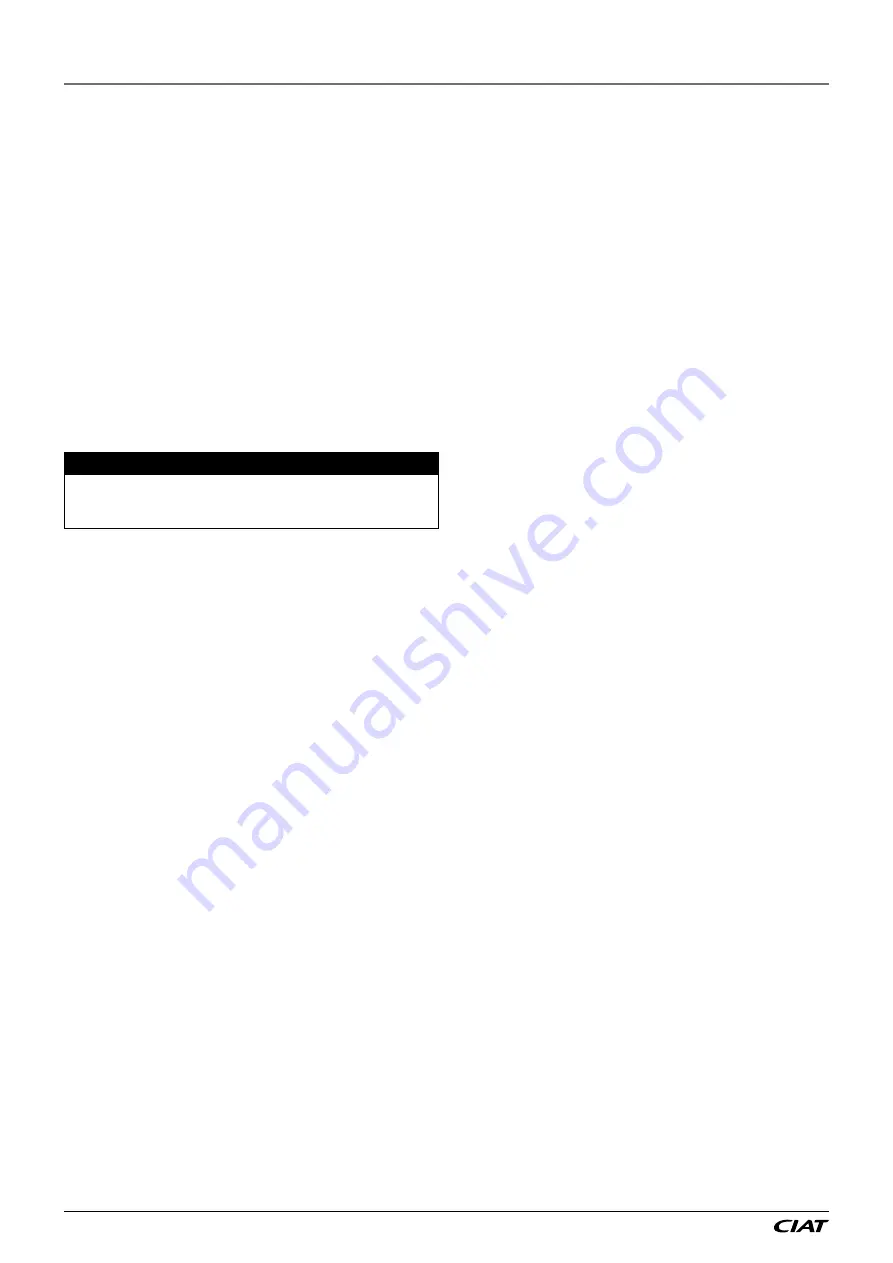
4.1
Control boards
The electrical box includes all boards controlling the unit as well
as the CONNECT TOUCH user interface.
Each circuit is by default fitted with one SIOB board used to
manage all major inputs and outputs of the controller.
Options such as energy management module or free cooling
(dry cooler management) require the installation of additional
boards, i.e. EMM SIOB board for energy management module
and FC dry cooler board for free cooling. Additionally, units with
seven or eight fixed speed fans are fitted with an additional
auxiliary 2 board “AUX2 board”.
All boards communicate via an internal bus.
4.2
Power supply to boards
All boards are supplied from a common 24 VAC supply referred
to earth.
CAUTION
Maintain correct polarity (and grounded 0V) when
connecting the power supply to the boards, otherwise
the boards may be damaged.
In the event of a power supply interrupt, the unit restarts
automatically without the need for an external command. However,
any faults active when the supply is interrupted are saved and may
in certain cases prevent a given circuit or the unit from restarting.
The main board continuously monitors the information received
from various pressure and temperature probes and accordingly
starts the program that controls the unit.
The number of boards available in the electrical box depends on
the number of selected options.
4.3
Light Emitting Diodes on boards
All boards continuously check and indicate the proper operation
of their electronic circuits. A light emitting diode (LED) lights on
each board when it is operating properly.
●
The red LED flashing for a two-second period indicates
correct operation. A different rate indicates a board or a
software failure.
●
The green LED flashes continuously on all boards to show
that the board is communicating correctly over its internal
bus. If the green LED is not flashing, this indicates the
internal bus wiring problem or a configuration issue.
4.4
Pressure transducers
Three types of transducers (high pressure, low pressure, water
pressure) are used to measure various pressures in each circuit.
These transducers deliver 0 to 5 VDC. They are connected to
SIOB boards (circuit A and circuit B).
Discharge pressure transducers (high pressure type)
These transducers measure the discharge pressure in each
circuit. They are used to control condensing pressure or high
pressure load shedding. Discharge pressure sensors are
mounted on the discharge line piping of each circuit.
Suction pressure transducers (low pressure type)
These transducers measure the suction pressure in each circuit.
They are used to control EXV, evaporating pressure (in heating
mode) and monitor suction pressure safeties related to the
compressor operating envelope. Suction pressure sensors are
located on the common suction piping of each circuit.
Pump inlet/outlet water pressure transducers (water
pressure type, hydronic kit option)
These transducers measure the hydronic kit pump inlet/outlet
water pressure and monitor the water flow. Pump inlet/outlet
water pressure sensors are mounted on the optional hydronic kit.
4.5
Temperature sensors
Temperature sensors constantly measure the temperature of
various components of the unit, ensuring the correct operation
of the system.
Water heat exchanger entering and leaving water
temperature sensors
The water heat exchanger entering and leaving water temperature
sensors are used for capacity control and safety purposes.
Outdoor air temperature sensor
This sensor measuring the outdoor air temperature is used for
start-up, setpoint temperature reset and frost control.
Suction gas temperature sensors
These sensors measure the suction gas temperature. They are
used for the EXV control. Suction gas temperature sensors are
located at the suction side of each circuit.
Master/slave water sensor (optional)
This sensor measures the common water temperature in the
master/slave system capacity control. It is installed only in the
case of master/slave units.
Defrost temperature sensors (heat pumps)
These sensors are used to determine the end of the defrost
cycle for a given circuit.
Temperature setpoint reset sensor (Energy Management
Module)
This sensor measures the space (room) temperature for the
purpose of setpoint reset.
4.6 Actuators
Electronic expansion valve
The electronic expansion valve (EXV) is used to adjust the
refrigerant flow to changes in the operating conditions of the
machine. The high degree of accuracy with which the piston is
positioned provides precise control of the refrigerant flow and
suction superheat.
Water flow switch
For units without internal pumps, a flow switch is mounted
to ensure that the minimum flow rate required for the correct
operation and protection of the system is maintained.
The minimum flow rate threshold depends on the unit size and
is configured automatically at the start-up. If the flow switch
fails, the alarm condition shuts off the unit.
Water heat exchanger pumps (optional)
The controller can regulate one or two fixed speed or variable
speed water heat exchanger pumps and takes care of the
automatic changeover between these pumps.
Four-way valve (heat pumps)
The control actuates the four-way valve for cooling / heating
mode and defrosts' sessions.
4 - HARDWARE
AQUACIAT
POWER
EN-8
Содержание AQUACIATPOWER ILD-HE Series
Страница 1: ...Instruction manual 05 2021 10536 CONNECT TOUCH AQUACIAT POWER I LD ST HE 602 2000...
Страница 2: ......