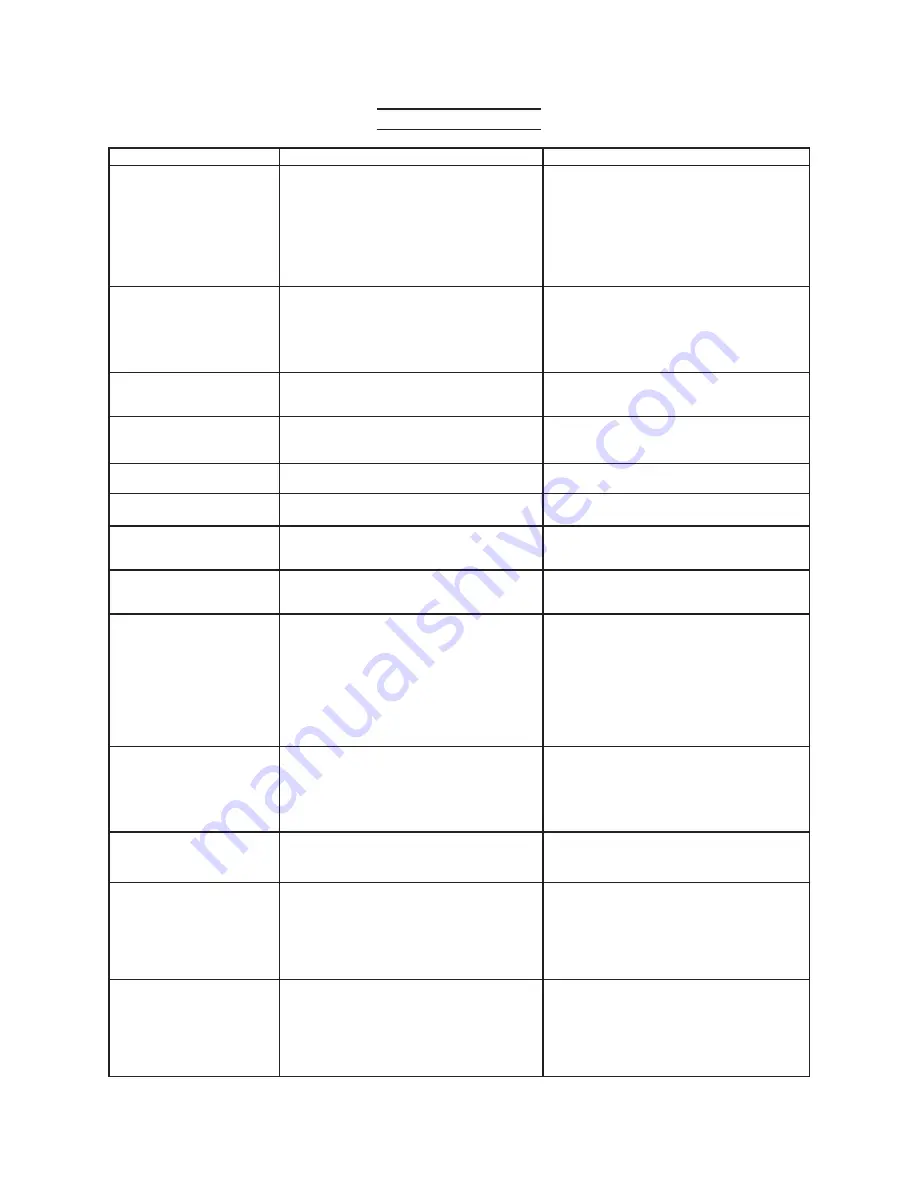
SKU 42933
For technical questions, please call 1-800-444-3353.
Page 20
troubleshooting
pROBLeM
cAuSe
SOLutIOn
Saw will not make a square
crosscut or a good 60° mitre
cut.
Arm is not perpendicular to the rip fence
1.
Too much play between the arm and column
2.
Yoke too loose when clamped to carriage
3.
Dust between stock and rip fence
4.
Table is not parallel with arm
5.
Rip Fence is not straight.
6.
Rear edge of table A not straight
7.
Adjust the crosscut travel with the rip fence
1.
Tighten the column sleeve bolt
2.
Adjust Yoke clamp handle
3.
Clean worktable
4.
Adjust Table A
5.
Replace rip fence.
6.
Sand or replace Table A
7.
60° cut not accurate
Saw Blade not perpendicular to worktable
1.
Too much play between arm and column
2.
Yoke is too loose when clamped to carriage
3.
Bevel Lock Knob is loose
4.
Table is not parallel with arm
5.
Adjust Saw Blade
1.
Tighten column sleeve bolt
2.
Adjust Yoke Clamp Handle
3.
Adjust Bevel Lock Knob
4.
Adjust Table A
5.
Workpiece has a tendency
to walk away from the fence
when ripping
Saw Blade is not parallel with the fence.
1.
Arm is not perpendicular to the rip fence.
2.
Adjust Saw Blade
1.
Adjust cross cut travel with rip fence
2.
Saw Blade tends to advance
over the stock too fast
Dull Saw Blade
1.
Not pulling the Saw Blade properly
2.
Replace or sharpen blade
1.
Draw Saw Blade across stock with a slow
2.
and steady pull
Cut depth varies from one end
to the other
Too much play between the arm and column
Tighten column sleeve bolt
Saw does not travel smoothly
in arm tracks
Dirty tracts
1.
Bad Bearings
2.
Clean tracts
1.
Replace Bearings
2.
Elevating Handle slips when
elevating or lowering the Saw
Blade
Screw loose on Elevating Handle
Tighten Screw
Clamping knobs do not hold
motor assembly to the set
position(s)
Treads stripped on knob(s)
Replace knob(s)
Saw Blade scores workpiece,
not giving a good finished cut
Saw Blade is leaning to one side
1.
Too much play between arm and column
2.
Yoke too loose when clamped to carriage
3.
Saw Blade bent or dull
4.
Not feeding saw properly
5.
Using improper Saw Blade for finish cut
6.
desired
Adjust Saw Blade square to rip fence
1.
Tighten column sleeve bolt
2.
Adjust Yoke Clamp Handle
3.
Replace Saw Blade
4.
Draw the Saw Blade across stock with a
5.
slow and steady pull
Replace Saw Blade
6.
Saw Blade or dado blades
tend to push stock to one side
when cross-cutting
Saw Blade is heeling
1.
Too much play between arm and column
2.
Yoke too loose when clamped to carriage
3.
Rip fence not straight
4.
Dull Saw Blade
5.
Adjust Saw Blade square to the rip fence
1.
Tighten column sleeve bolt
2.
Adjust Yoke Clamp Handle
3.
Replace rip fence
4.
Replace or sharpen Saw Blade
5.
Saw Blade Stalls when ripping
Arbor Nut loose
1.
Dull Saw Blade
2.
Saw Blade not parallel to fence
3.
Tighten
1.
Replace or sharpen
2.
Adjust Saw Blade or fence to parallel
3.
Motor will not reach full speed
or power
Faulty ON/OFF Switch
1.
Circuit overloaded with other appliances
2.
Motor windings burned out
3.
Circuit used is under rated for this
4.
application
Have the Switch unit checked by a qualified
1.
technician
Use a different circuit for the machine
2.
Replace motor
3.
Use a different circuit with sufficient power
4.
for this machine
Motor overheats, stalls, trips
the circuit breakers or fuses
Overloaded motor
1.
Improper cooling caused by excessive
2.
sawdust accumulation around the motor
Motor winding burned out or open
3.
Power source circuit breakers do not have
4.
sufficient power capacity
Feed stock into Saw Blade more slowly
1.
Clean motor housing with compressed air
2.
Replace motor using a qualified technician
3.
Install proper size circuit breakers or change
4.
circuits to one with more capacity