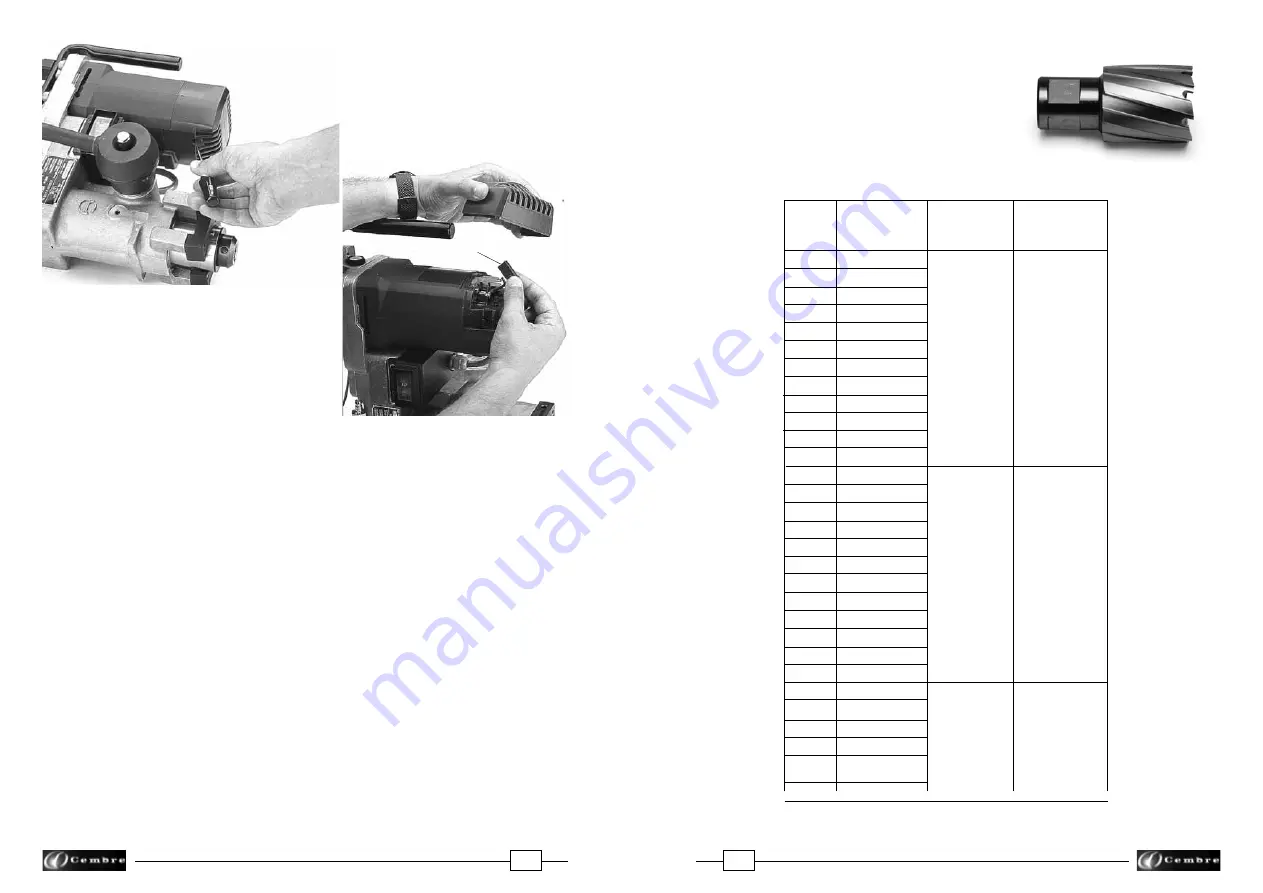
8
27
All the broach cutters allow automatic cooling by means of the SR5000 unit supplied with
the drills.
3.7) BROACH CUTTERS
These cutters rapidly produce high quality, accurate
holes in a single pass. The automatic lubrocooling
system reduces friction and eliminates heat build up
during the drilling operation. Under standard conditions
a broach cutter can drill 40-50 holes, depending on
the hardness of the rail.
15128
15130
15132
15234
TSC 1 1/8"
15138
TSC 1 1/4"
TSC 1 5/16"
15144
15146
TSC 1 1/2"
TSC 3/4"
01354
01355
01356
01357
01358
01359
01360
01361
01362
01363
01364
12218
3-12224
3-12226
3-12228
3-12230
3-12232
3-12236
BROACH
CUTTER
PILOT
BIT
HOLE
DIAME-
TER
(inches)
7/8"
15/16"
1"
1 1/16"
1 1/8"
1 3/16"
1 1/4"
1 5/16"
1 3/8"
1 7/16"
1 1/2"
3/4"
7/8"
15/16“
1“
1 1/16"
1 1/8"
1 3/16“
1 1/4"
1 5/16“
1 3/8"
1 7/16"
1 1/2"
9/16"
3/4"
13/16"
7/8"
15/16"
1"
1 1/8"
MAX.
DEPTH OF CUT
(inches)
Ref. PPC 2
Ref. PPL 2
3-10528
2 "
7/8 "
3 "
APPENDIX “A”
Factors which infl uence the number of holes that can be made according to the
tool used.
– Hardness of the material to be drilled.
– Thickness to be drilled.
– Stability of the drill clamp and correct assembly of the cutter/bit.
– Suitable lubrocooling (lubrication/cooling) to keep the temperature of the tool low so
as not to compromise the effi ciency of the cutting edges, whilst at the same time facilitating
the removal of the swarf.
– Contact time of the cutting edges of the cutter/bit with the material to be drilled;
bear in mind that the faster the hole is made the greater the effi ciency.
– Observance:
1) Commence drilling by exerting light pressure on the advancing lever, progres-
sively increasing and then relaxing it when the tool is in the exit phase.
2) Avoid pressure jolts and only advance according to the drilling diameter to avoid scratch-
ing the material or damaging the cutting edges of the cutter/bit.
3) Remember that a tool with effi cient cutting edges requires a pressure lower than that
applied to one with which a certain number of holes have already been made.
4) When holes are made close to raised lettering on the rails, commence drilling
with very light pressure until the lettering disappears, to avoid possible breakage of the
tool.
5) Bear in mind that when operating on very hard rails, as in the case of quality 1100 steel,
it is advisable to increase the lubrocoolant fl ow rate.
FIG. 26 – CHANGING THE BRUSHES
Brush