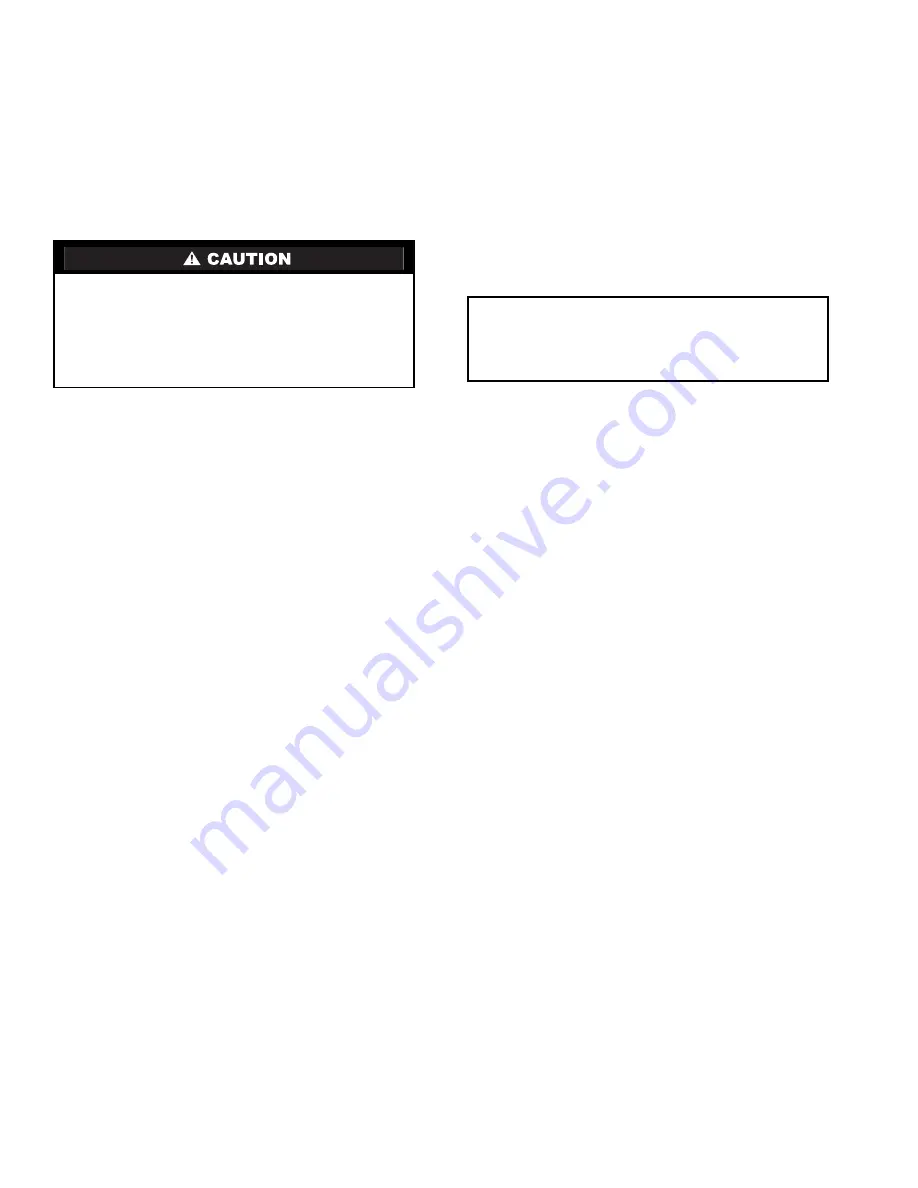
6
PROTECTION — Once the units are properly positioned on
the jobsite, they must be covered with either a shipping carton,
vinyl film, or an equivalent protective covering. Open ends of
pipes stored on the jobsite must be capped. This precaution is
especially important in areas where painting, plastering, or
spraying of fireproof material, etc. is not yet complete. Foreign
material that is allowed to accumulate within the units can pre-
vent proper start-up and necessitate costly clean-up operations.
Before installing any of the system components, be sure to
examine each pipe, fitting, and valve, and remove any dirt or
foreign material found in or on these components.
INSPECT UNIT — To prepare the unit for installation, com-
plete the procedures listed below:
1. Compare the electrical data on the unit nameplate with
ordering and shipping information to verify that the
correct unit has been shipped.
2. Verify that the unit is the correct model for the entering
water temperature of the job.
3. Do not remove the packaging until the unit is ready for
installation.
4. Verify that the refrigerant tubing is free of kinks or dents,
and that it does not touch other unit components.
5. Inspect all electrical connections. Be sure connections are
clean and tight at the terminals.
6. Compressors are internally spring-mounted. Compressors
equipped with external spring vibration isolators must
have bolts loosened and shipping clamps removed.
7. Locate and verify any accessory kit located in compressor
section.
8. Remove any access panel screws that may be difficult to
remove once unit is installed.
Step 3 — Location of Unit —
The following guide-
lines should be considered when choosing a location for
WSHP:
• Units are for indoor use only
• Provide sufficient space for water and electrical
connections
• Locate unit in an area that allows for easy access and
removal of access panels
• Allow enough space for service personnel to perform
maintenance
Step 4 — Mounting the Unit —
Mount unit as shown
in Fig. 2A-4. Rod attachments must be able to support the
weight of the unit. See Table 1 for unit operating weights.
Step 5 — Piping Connections —
Depending on the
application, there are 3 types of WSHP piping systems to
choose from: water loop, ground-water and ground loop. See
Fig. 2A-4. Refer to the Carrier System Design Manual for ad-
ditional information.
All WSHP units utilize low temperature soldered female
pipe thread fittings for water connections to prevent annealing
and out-of-round leak problems which are typically associated
with high temperature brazed connections. When making pip-
ing connections, consider the following:
• A backup wrench must be used when making screw con-
nections to unit to prevent internal damage to piping.
• Insulation may be required on piping to avoid condensa-
tion in the case where fluid in loop piping operates at
temperatures below dew point of adjacent air.
• Piping systems that contain steel pipes or fittings may
be subject to galvanic corrosion. Dielectric fittings may
be used to isolate the steel parts of the system to avoid
galvanic corrosion.
WATER SUPPLY AND QUANTITY — Check water sup-
ply. Water supply should be plentiful and of good quality. See
Table 2 for water quality guidelines.
In all applications, the quality of the water circulated
through the heat exchanger must fall within the ranges listed in
the Water Quality Guidelines table. Consult a local water treat-
ment firm, independent testing facility, or local water authority
for specific recommendations to maintain water quality within
the published limits.
WATER LOOP APPLICATIONS — Water loop applica-
tions usually include a number of units plumbed to a common
piping system. See Fig. 2A and 2B. Maintenance to any of
these units can introduce air into the piping system. Therefore,
air elimination equipment comprises a major portion of the
mechanical room plumbing.
The flow rate is usually set between 2.25 and 3 gpm per ton
of cooling capacity. For proper maintenance and servicing,
pressure-temperature (P/T) ports are necessary for temperature
and flow verification.
In addition to complying with any applicable codes, consid-
er the following for system piping:
• Piping systems utilizing water temperatures below
50 F require
1
/
2
-in. closed cell insulation on all piping
surfaces to eliminate condensation.
• All plastic to metal threaded fittings should be avoided
due to the potential to leak. Use a flange fitted substitute.
• Teflon tape thread sealant is recommended to minimize
internal fouling of the heat exchanger.
• Use backup wrench. Do not overtighten connections.
• Route piping to avoid service access areas to unit.
• The piping system should be flushed prior to operation to
remove dirt and foreign materials from the system.
GROUND-WATER APPLICATIONS — Typical ground-
water piping is shown in Fig. 3. In addition to complying with
any applicable codes, consider the following for system piping:
• Install shut-off valves for servicing.
• Install pressure-temperature plugs to measure flow and
temperature.
• Boiler drains and other valves should be connected using
a “T” connector to allow acid flushing for the heat
exchanger.
• Do not overtighten connections.
• Route piping to avoid service access areas to unit.
• Use PVC SCH80 or copper piping material.
NOTE: PVC SCH40 should not be used due to system high
pressure and temperature extremes.
DO NOT store or install units in corrosive environments or
in locations subject to temperature or humidity extremes
(e.g., attics, garages, rooftops, etc.). Corrosive conditions
and high temperature or humidity can significantly reduce
performance, reliability, and service life. Always move
units in an upright position. Tilting units on their sides may
cause equipment damage.
IMPORTANT: Failure to comply with the above required
water quality and quantity limitations and the closed-
system application design requirements may cause damage
to the tube-in-tube heat exchanger that is not the responsi-
bility of the manufacturer.