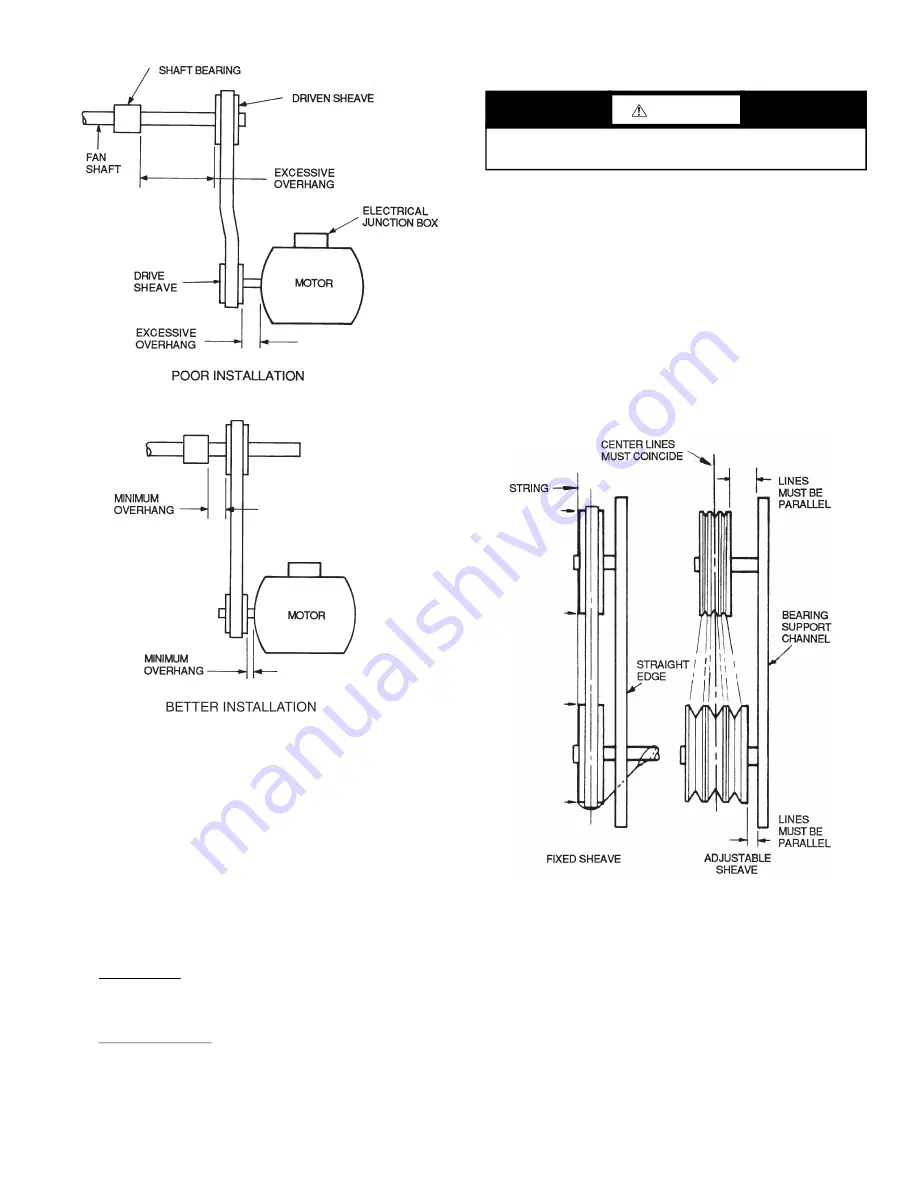
111
ALIGNMENT
Make sure that fan shafts and motor shafts are parallel and level.
The most common causes of misalignment are nonparallel shafts
and improperly located sheaves. Where shafts are not parallel,
belts on one side are drawn tighter and pull more than their share
of the load. As a result, these belts wear out faster, requiring the
entire set to be replaced before it has given maximum service. If
misalignment is in the sheave, belts enter and leave the grooves at
an angle, causing excessive belt and sheave wear.
1. Shaft alignment can be checked by measuring the distance
between the shafts at 3 or more locations. If the distances are
equal, then the shafts are parallel.
2. Sheave Alignment:
Fixed sheaves — To check the location of the fixed sheaves
on the shafts, a straightedge or a piece of string can be used. If
the sheaves are properly aligned, the string will touch them at
the points indicated by the arrows in Fig. 55.
Adjustable sheaves — To check the location of adjustable
sheave on shaft, make sure that the centerlines of both
sheaves are in line and parallel with the bearing support chan
-
nel. See Fig. 55. Adjustable pitch drives are installed on the
motor shaft. Carrier recommends that adjustable sheaves
should only be used for initial balancing and should be
replaced with fixed pitch sheaves by the air balancer prior to
the final system air balance.
3. Rotate each sheave one-half revolution to determine whether
the sheave is wobbly or the drive shaft is bent. Correct any
misalignment.
4. With sheaves aligned, tighten cap screws evenly and
progressively.
NOTE: There should be a
1
/
8
-in. to
1
/
4
-in. gap between the mating
part hub and the bushing flange. If gap is closed, the bushing is
probably the wrong size.
5. With taper-lock bushed hubs, be sure the bushing bolts are
tightened evenly to prevent side-to-side pulley wobble.
Check by rotating sheaves and rechecking sheave alignment.
When substituting field-supplied sheaves for factory-supplied
sheaves, consider that fan shaft sheave has been factory bal
-
anced with fan and shaft as an assembly. For this reason, sub
-
stitution of motor sheave is preferable for final speed
adjustment.
V-Belts
When installing or replacing belts, always use a complete set of
new belts. Mixing old and new belts will result in the premature
wear or breakage of the newer belts. See Fig. 56.
Refer to label on inside of fan access door for information on
factory-supplied drive.
1. Always adjust the motor position so that V-belts can be
installed without stretching over grooves. Forcing belts can
result in uneven stretching and a mismatched set of belts.
2. Do not allow belt to bottom out in sheave.
3. Tighten belts by turning motor-adjusting jackscrews. Turn
each jackscrew an equal number of turns.
Fig. 54 —
Determining Sheave-Shaft Overhang
A39-376tf
CAUTION
Do not exceed maximum fan speed rpm with adjustable
sheave. Equipment damage may result.
Fig. 55 —
Determining Sheave-Shaft Alignment
A39-137tf