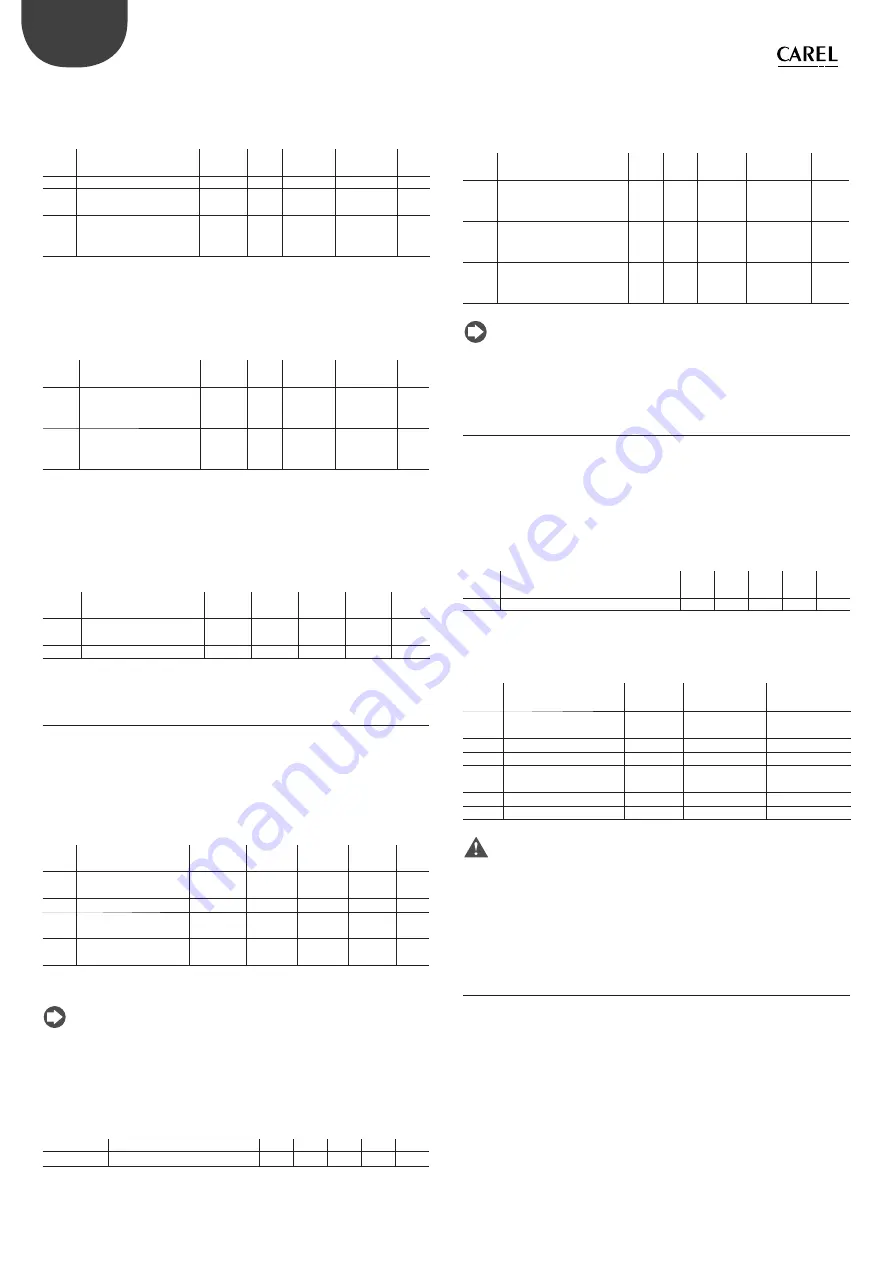
ENG
“Power+” +0300050EN - rel. 2.3 - 08.06.2012
20
Motor start-up
These parameters optimise the initial start-up phase of the motor and the
relative estimate of the position and the rotor speed. It is recommended to use
the values indicated by CAREL depending on the motors/compressors available.
Mod.
add.
Description
Def
Min
Max
U.M.
R/W
51
Magnetizing time
100
0
30000
ms
R/W
57
Starting current
200
(20.0%)
0
1000
(100.0%)
0.1%
R/W
58
Maximum frequency
for starting current
0
0
1000
(100.0%)
0.1%
Motor base
frequency
R/W
Tab. 4.o
Motor control in regenerative functioning mode
It is recommended to use the default values. Typically in the applications with
compressors, the regenerative functioning mode never occurs. For particular
applications, consult CAREL.
Mod.
add.
Description
Def
Min
Max
U.M.
R/W
53
Regeneration current
limit
1000
(100.0%)
0
2000
(200.0%)
0.1%
Motor rated
current
R/W
54
Overvoltage control
current limit
100
(10.0%)
0
2000
(200.0%)
0.1%
Motor rated
current
R/W
Tab. 4.p
P
I parameters for speed regulation
In applications with slow acceleration and deceleration times, as with
compressors, it is recommended to use default values or the values indicated
by CAREL depending on the motors/compressors available. For particular
applications, consult CAREL.
Mod.
add.
Description
Def
Min
Max
U.M.
R/W
55
Speed loop: Kp
250
(25.0%)
1
(0.1%)
2000
(200.0%)
0.1%
R/W
56
Speed loop: Ti
500
1
1000
ms
R/W
Tab. 4.q
4.4 C - Asynchronous motor with V/f control
Motor data plate
Frequency/voltage/rated current/power factor
The base frequency is the frequency at which the maximum voltage is applied.
The rated voltage is the maximum voltage applied to the motor. If current
peaks are necessary, the rated current of the motor must be lower enough that
the drive rated current. The Power factor is the rated cos
of the motor.
Mod.
add.
Description
Def
Min
Max
U.M.
R/W
1
Motor base frequency
500
(50.0Hz)
250
(25.0Hz)
5000
(500.0Hz)
0.1Hz
R/W
2
Motor base voltage
230/400
25
250/500
V
R/W
3
Motor rated current
Rated
current (*)
(*)
(*)
0.1A
R/W
4
Motor power factor
(cos
100
(1.00)
0/50
(0.5)
100
(1.00)
0.01
R/W
Tab. 4.r
(*) Values are model dependent. See chapter 7 “PARAMETERS TABLE”.
Note
: see the Appendix for the frequency to the revolution speed
conversion formulas, related to the number of motor poles.
Motor electric data
No parameter has to be set. If Autotuning is performed, the “stator resistance”
parameter is set automatically at the end of the Autotuning procedure on the
basis of the measurements detected, also if its value is not used.
Mod. add. Description
Def
Min
Max
U.M.
R/W
46
Stator resistance
0
0
38500 mΩ
R/W
Tab. 4.s
Motor start-up
These parameters optimise the initial start-up phase of the motor by adapting
the V/f feature on the basis of the particular application, in order to improve
performance at low speeds.
Mod.
add.
Description
Def
Min
Max
U.M.
R/W
35
V/f boost voltage
0
0
250
(25.0%)
0.1%
Motor base
voltage
R/W
36
V/f frequency adjustment
0
0
1000
(100.0%)
0.1%
Motor base
frequency
R/W
37
V/f voltage adjustment
0
0
1000
(100.0%)
0.1%
Motor base
voltage
R/W
Tab. 4.t
Note
: In the case of asynchronous motor with V/f control, the parameters
loose meaning for the control of the motor in regenerative functioning mode
and the PI parameters for the speed control.
4.5 Autotuning
Autotuning consists in a measurement cycle, which can last about 1
minute, at the end of which the electric data of the motor are measured
and memorised in the respective parameters. To perform Autotuning, set
the “Autotuning” parameter at 1. At the end, the parameter is automatically
zeroed. The type of measure and the values memorised depend on the type
of motor control selected. See the following tables. If this is unsuccessful,
check the alarm 15. It is therefore necessary to repeat the procedure or search
for the data requested in order to introduce them directly.
Mod.
add.
Description
Def
Min
Max
U.M.
R/W
103
Autotuning 0/1=not active/start
0
0
1
-
R/W
Tab. 4.u
Below a summary table with the electric data estimated according to the
type of motor. Where indicated at the end of the procedure, the parameters
are set at zero (0).
Mod.
add.
Description
PM
Brushless
Asynchronous
vect.
Asynchronous
V/f
45
Motor magnetizing
current
NO(0)
YES
NO
46
Stator resistance
YES
YES
YES
47
Rotor resistance
NO(0)
YES
NO
48
Ls stator inductance or
Ld inductance
YES, Ld
YES, Ls
NO
49
Leakage factor
NO(0)
YES
NO
50
Lq inductance
YES
NO(0)
NO
Tab. 4.v
Important
:
•
Autotuning can only be performed when a motor is connected. At the
start of the procedure, the motor must be at a standstill;
•
the end of the Autotuning procedure is signalled by the “Autotuning”
parameter and from bit7 of the “Status register”, which are automatically
taken back to 0.
4.6 Controls before commissioning
Before commissioning, check that:
•
the drive output current is greater than or equal to the rated current or the
maximum envisioned for the motor;
•
the work voltage range is correct
•
the section of the power supply cables is correct;
•
the maximum section and length of the motor cables is correct and that
they are connected in compliance with the wiring diagrams;
•
all of the control inputs are connected correctly.
Содержание Power+
Страница 2: ......
Страница 4: ......
Страница 6: ...ENG Power 0300050EN rel 2 3 08 06 2012 6 ...
Страница 35: ......