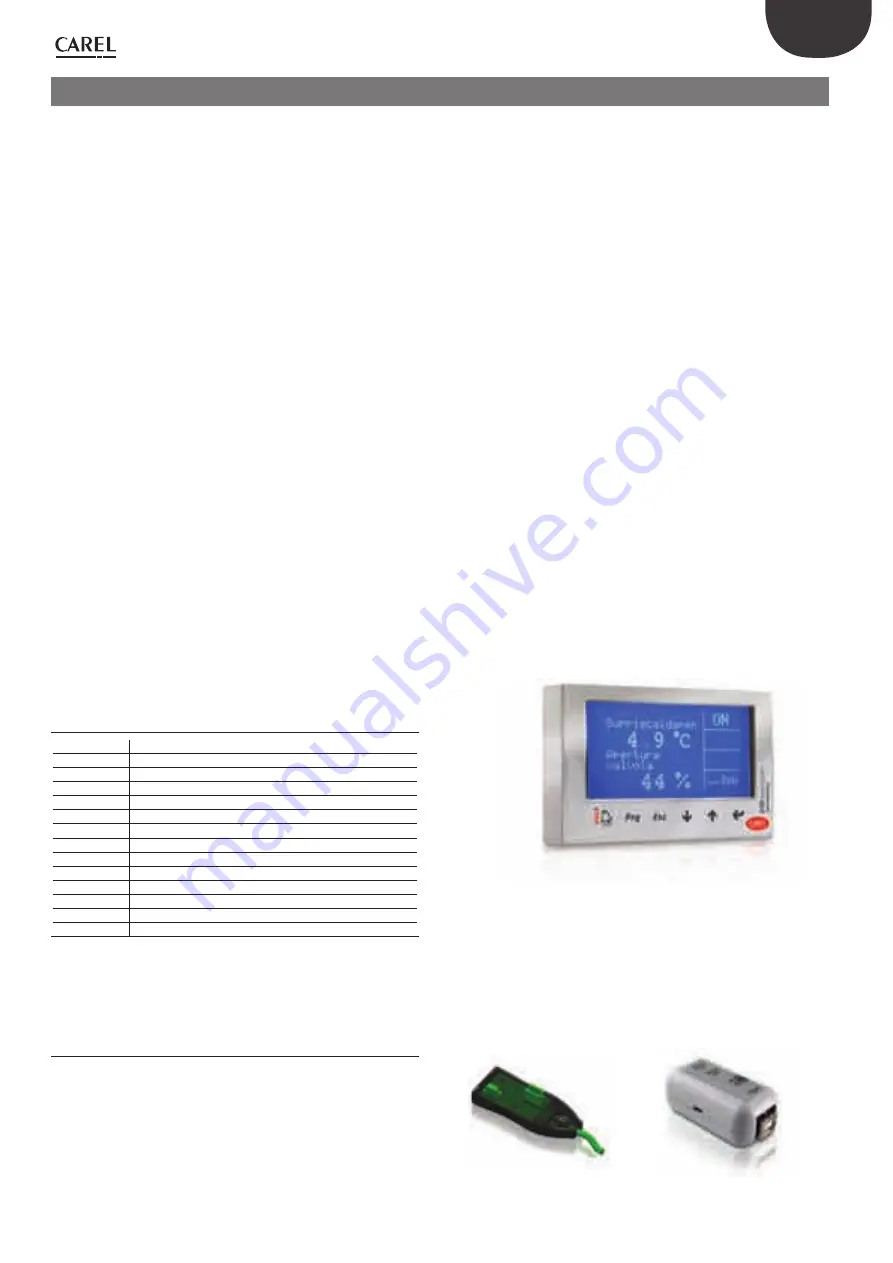
7
ENG
“EVD evolution” +030222041 - rel. 1.0 - 01.06.2008
INTRODUCTION
1.
EVD evolution is a driver for double pole stepper motors designed for to
control the electronic expansion valve in refrigerant circuits. It is designed
for DIN rail assembly and is fi tted with plug-in screw terminals. It controls
refrigerant superheat and optimises the effi ciency of the refrigerant circuit,
guaranteeing maximum fl exibility, being compatible with various types
of refrigerants and valves, in applications with chillers, air-conditioners
and refrigerators, the latter including subcritical and transcritical CO2
systems. It features low superheat, high evaporation pressure (MOP), low
evaporation pressure (LOP) and high condensing temperature protection,
and can manage, as an alternative to superheat control, special functions
such as the hot gas bypass, the evaporator pressure control (EPR) and
control of the valve downstream of the gas cooler in transcritical CO2
circuits. Together with superheat control, it can manage an auxiliary
control function selected between condensing temperature protection
and “modulating thermostat”. As regards network connectivity, the driver
can be connected to either of the following:
a pCO programmable controller to manage the driver via pLAN;
•
a pCO programmable controller or PlantVisorPRO supervisor for
•
supervision only, via tLAN or RS485/Modbus® respectively. In this case,
On/Off control is performed via digital input 1.
The second digital input is available for optimised defrost management.
Another possibility involves operation as a simple positioner with 4 to 20
mA or 0 to 10 Vdc analogue input signal. EVD evolution comes with a LED
board to indicate the operating status, or a graphic display (accessory) that
can be used to perform installation, following a guided commissioning
procedure involving setting just 4 parameters: refrigerant, valve, pressure
sensor, type of main control (chiller, showcase, etc.). The procedure can
also be used to check that the sensor and valve motor wiring is correct.
Once installation is complete, the display can be removed, as it is not
necessary for the operation of the driver, or alternatively kept in place to
display the signifi cant system variables, any alarms and when necessary
set the control parameters. The driver can also be setup using a computer
via the service serial port. In this case, the VPM program (Visual Parameter
Manager) needs to be installed, downloadable from http://ksa.carel.com,
and the USB-tLAN converter EVDCNV00E0 connected.
Models
1.1
Code
Description
EVD0000E00
EVD evolution - tLAN
EVD0000E10
EVD evolution - pLAN
EVD0000E20
EVD evolution - RS485/Modbus®
EVD0000E01
EVD evolution - tLAN, multiple pack of 10 pcs (*)
EVD0000E11
EVD evolution - pLAN, multiple pack of 10 pcs (*)
EVD0000E21
EVD evolution - RS485/Modbus®, multiple pack of 10 pcs (*)
EVDIS00DE0
Display for EVD evolution, German
EVDIS00EN0
Display for EVD evolution, English
EVDIS00ES0
Display for EVD evolution, Spanish
EVDIS00FR0
Display for EVD evolution, French
EVDIS00IT0
Display for EVD evolution, Italian
EVDIS00PT0
Display for EVD evolution, Portuguese
EVDCON0021 EVD evolution, connector kit (10 pcs) for multiple pack (*)
Tab. 1.a
(*)The codes with multiple packages are sold without connectors,
available separately in code EVDCON0021.
Functions and main characteristics
1.2
In summary:
electrical connections by plug-in screw terminals;
•
serial card incorporated in the driver, based on the model (tLAN, pLAN,
•
RS485/Modbus®);
compatibility with various types of valves and refrigerants;
•
activation/deactivation of control via digital input 1 or remote control
•
via pLAN, from pCO programmable controller;
superheat control with protection functions for low superheat, MOP,
•
LOP, high condensing temperature;
confi guration and programming by display (accessory), by computer
•
using the VPM program or by PlantVisor/PlantVisorPro supervisor and
pCO programmable controller;
commissioning simplifi ed by display with guided procedure for setting
•
the parameters and checking the electrical connections;
multi-language graphic display, with “help” function on various
•
parameters;
management of diff erent units of measure (metric/imperial);
•
parameters protected by password, accessible at a service (installer)
•
and manufacturer level;
copy the confi guration parameters from one driver to another using
•
the removable display;
ratiometric or electronic 4 to 20 mA pressure transducer, the latter
•
can be shared between a series of driver, useful for multiplexed
applications;
possibility to use S3 and S4 as backup sensors in the event of faults on
•
the main sensors S1 and S2;
4 to 20 mA or 0 to 10 Vdc input to use the driver as a positioner
•
controlled by an external signal;
management of power failures with valve closing (if the EVBAT200/
•
EVBAT300 accessory is fi tted);
advanced alarm management.
•
Series of accessories for EVD evolution
Display (code EVDIS00**0)
Easily applicable and removable at any time from the front panel of
the driver, during normal operation displays all the signifi cant system
variables, the status of the relay output and recognises the activation of
the protection functions and alarms. During commissioning, it guides
the installer in setting the parameters required to start the installation
and, once completed, can copy the parameters to other drivers. The
models diff er in the fi rst settable language, the second language for all
models is English. EVDIS00**0 can be used to confi gure and monitor all
the control parameters, accessible via password at a service (installer) and
manufacturer level.
Fig. 1.a
USB/tLAN converter (code EVDCNV00E0)
The USB-tLAN converter is connected, once the LED board cover has been
removed, to the service serial port underneath. Fitted with cables and
connectors, it can connect EVD evolution directly to a computer, which,
using the VPM program, can confi gure and program the driver. VPM can
also be used to update the driver and display fi rmware. See appendix I.
Fig. 1.b