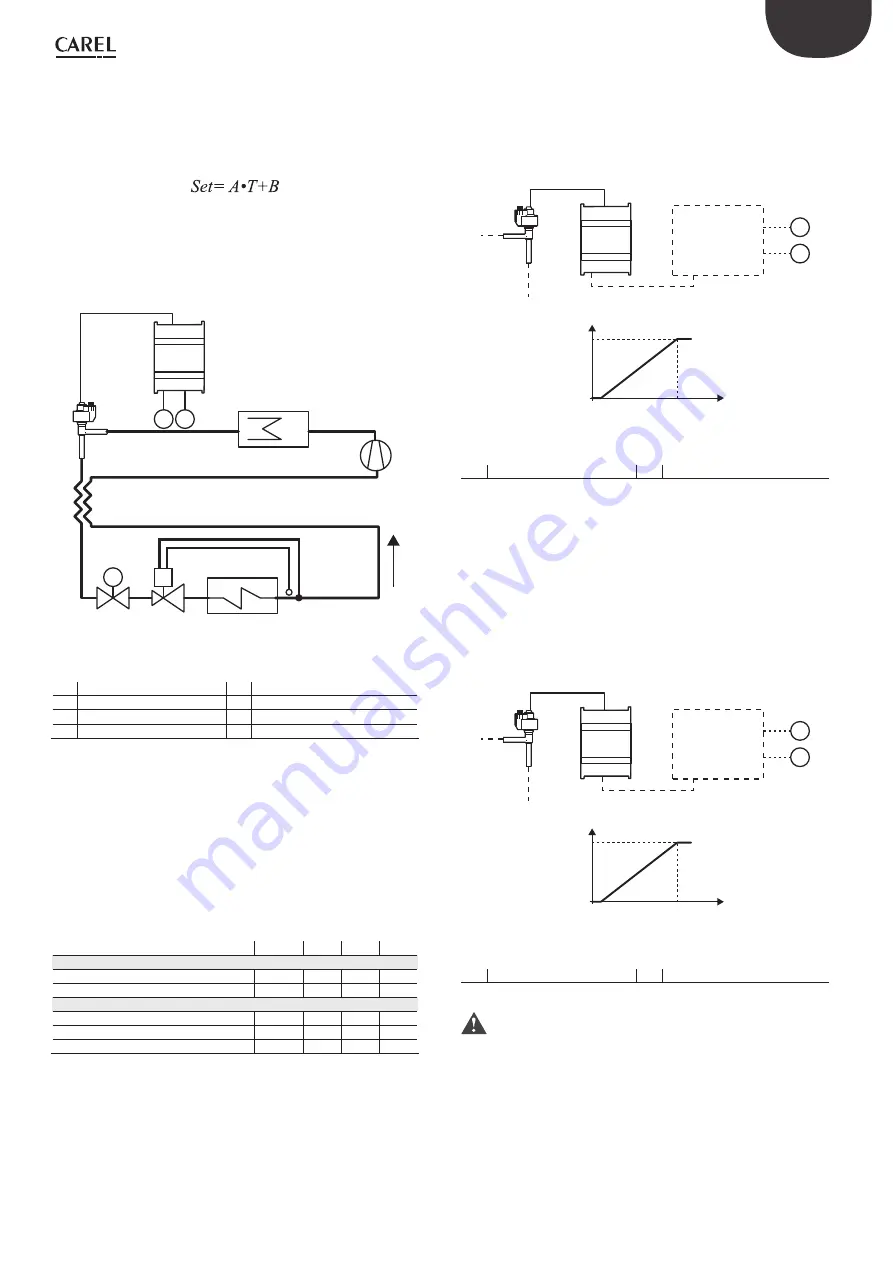
21
ENG
“EVD evolution” +030222041 - rel. 1.0 - 01.06.2008
Transcritical CO
2
gas cooler
This solution for the use of CO
2
in refrigerating systems with a transcritical
cycle involves using a gas cooler, that is a refrigerant/air heat exchanger
resistant to high pressures, in place of the condenser. In transcritical
operating conditions, for a certain gas cooler outlet temperature, there is
pressure that optimises the efficiency of the system:
Set= pressure set point in a gas cooler with transcritical CO
2
T= gas cooler outlet temperature
Default value: A= 3.3, B= -22.7.
In the simplified diagram shown below, the simplest solution in
conceptual terms is shown. The complications in the systems arise due to
the high pressure and the need to optimise efficiency.
E
V1
V2
M
T
CP
GC
IHE
S1
S2
EVD
evolution
P
T
Fig. 5.e
Key:
CP Compressor
V2
Thermostatic expasnion valve
GC Gas cooler
EV
Electronic valve
E
Evaporator
IHE Inside heat exchanger
V1
Solenoid valve
For the wiring, see paragraph 2.7 “General connection diagram”.
This involves PID control without any protectors (LowSH, LOP, MOP,
HiTcond, see the chapter on Protectors), without any valve unblock
procedure and without auxiliary control. Control is performed on the gas
cooler pressure sensor value read by input S1, with a set point depending
on the gas cooler temperature read by input S2; consequently there is
not a set point parameter, but rather a formula:
“CO
2
gas cooler pressure set point”= Coefficient A * Tgas cooler (S2) +
Coefficient B. The set point calculated will be a variable that is visible
in display mode. Control is direct, as the pressure increases, the valve
opens.
Parameter/description
Def.
Min.
Max.
UOM
SPECIAL
Transcritical CO
2
: coefficient A
3,3
-100
800
-
Transcritical CO
2
coefficient B
-22,7
-100
800
-
CONTROL
PID: proportional gain
15
0
800
PID: derivative time
150
0
1000
s
PID: integration time
5
0
800
s
Analogue positioner (4 to 20 mA)
The valve will be positioned linearly depending on the value of the “4 to
20 mA input for analogue valve positioning” read by input S1.
There is no PID control nor any protection (LowSH, LOP, MOP, HiTcond, see
the chapter on Protectors), no valve unblock procedure and no auxiliary
control.
EV
S1
EVD
evolution
4-20 mA
regulator
T
P
4
20
mA
A
0%
100%
Fig. 5.f
Key:
EV
Electronic valve
A
Valve opening
For the wiring, see paragraph 2.7 “General connection diagram”.
Forced closing will only occur when digital input DI1 opens, thus
switching between control status and standby. The pre-positioning and
repositioning procedures are not performed. Manual positioning can be
enabled when control is active or in standby.
Analogue positioner (0 to 10 Vdc)
The valve will be positioned linearly depending on the value of the “0 to
10 V input for analogue valve positioning” read by input S1.
There is no PID control nor any protection (LowSH, LOP, MOP, HiTcond),
no valve unblock procedure and no auxiliary control, with corresponding
forced closing of the valve and changeover to standby status.
EV
S2
EVD
evolution
0-10 Vdc
regulator
T
P
0
10
Vdc
A
0%
100%
Fig. 5.g
Key:
EV
Electronic valve
A
Valve opening
For the wiring, see paragraph 2.7 “General connection diagram”.
Important:
the pre-positioning and repositioning procedures
are not performed. Manual positioning can be enabled when control is
active or in standby.