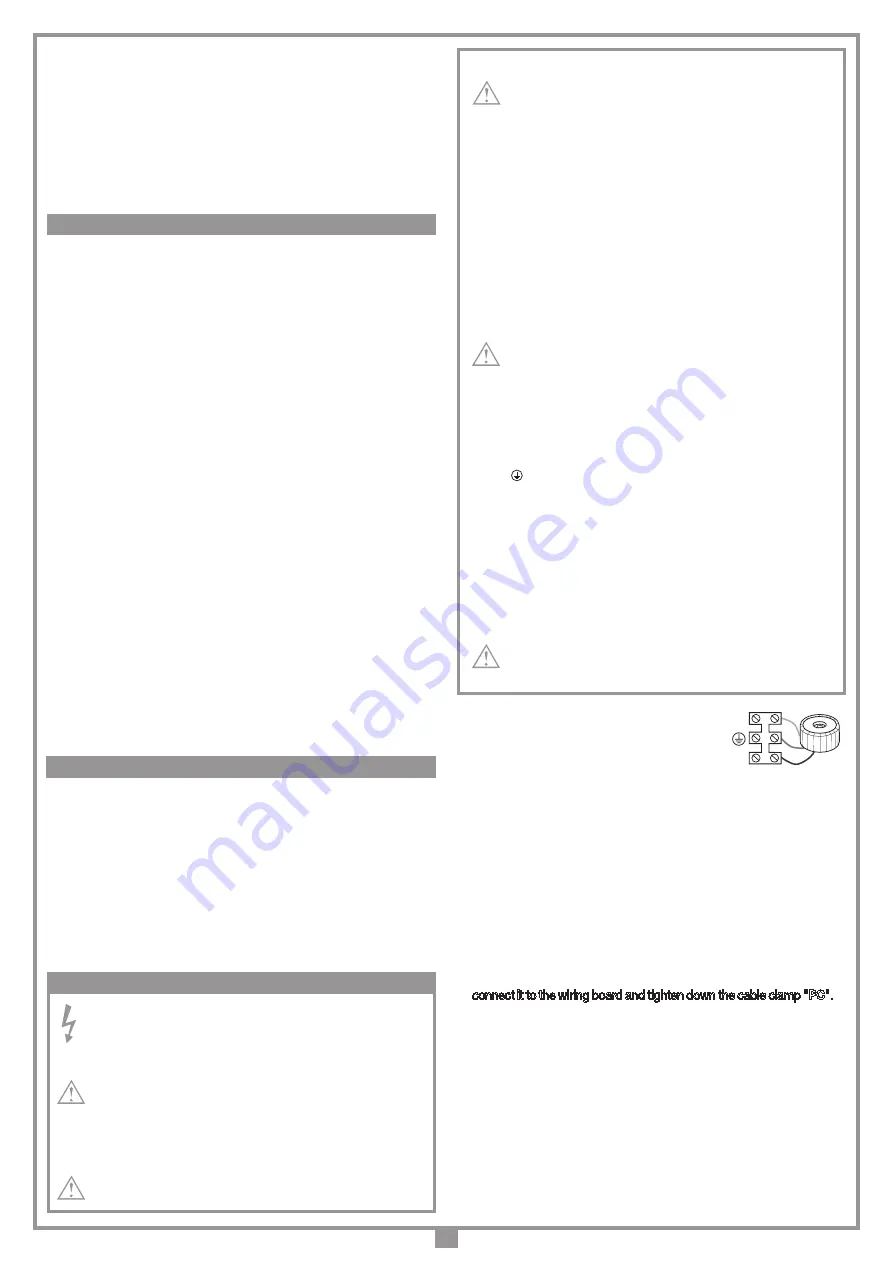
16
• After having installed the device, and
before powering
up the programmer
, release the door (manual release
mechanism) and move it manually, checking that it moves
smoothly and has no unusual points of resistance.
• The controlled load output (binding post 15) is aimed at
reducing battery power consumption (if they are installed)
during blackouts; photocells and other safety devices should
be connected to this output.
• When a command is received, via radio or via wire, the
electronic programmer routes voltage to the
CTRL 24 Vdc
output. It then evaluates the state of the safety devices and
if they are at rest it will activate the motor.
• Connecting devices to the controlled output contact also
allows you to carry out the autotest function (enabled using
"TEST FI" and "TEST FS" in the "OPTIONS) and check that
the safety devices are functioning correctly.
• The presence of the electrical current sensor does not
dispense with the obligation to install photoelectric cells and
other safety devices foreseen by the
safety standards in
force
.
• Before connecting the appliance make sure that the voltage
and frequency rated on the data plate conform to those of
the mains supply.
• For the
230 Vac
power supply only use a
2 x 1.5 mm
2
+
cable.
• The cable may only be replaced by qualified technicians.
• An all pole trip switch with at least
3 mm
between the
contacts must be installed between the unit and the mains
supply.
• Don't use cables with aluminium conductors; don't solder
the ends of cables which are to be inserted into the binding
posts; use cables marked
T min 85°C
and resistant to
atmospheric agents.
• The terminal wires must be positioned in such a way that
both the wire and the insulating sheath are tightly fastened
(a plastic jubilee clip is sufficient).
230 Vac POWER SUPPLY CONNECTION
• Connect the control and security device wires.
• Run the mains power supply to the
separate
three-way
terminal board that is already
connected to the transformer.
• The master motor "
M1
" and relative encoder are pre-wired. If you need
to disconnect them (for maintenance interventions etc.) you must replace
the cable following the colour order of the wires as shown in figure 9.
Preparing the motor connection wires
• The kit contains
10 metres
of 6-wire cable that should be cut according
to the needs of the installation:
- connect the wires of motor "
M2
" and encoder "
2
" to the wiring board
of the slave motor (second motor);
- you must scrupulously respect the motor connection sequence
between the motors and the programmer. The order of the binding
post connections 1 to 6 is identical on both;
- run the end of the cable to the terminal board on the master motor and
connect it to the wiring board and tighten down the cable clamp "
PC
".
Note: If you need to choose a longer cable for particular installations (cut
from the 100 metres of cable supplied in a reel) you must remember that
in order to avoid current dispersion the maximum length of the cable must
not exceed
20 metres
.
Motor 1
1-2
Motor power supply 1
3-4-5-6 Encoder signal input 1
Motor 2
1-2
Motor power supply 2
3-4-5-6 Encoder signal input 2
• Fasten the geared motor to the galvanised steel base "
D
" using the screws
"
G
" with relative self-locking nuts and washers.
• Assemble the articulated operator arm following the indications shown
in figure 6.
• Release the motore (fig. 7).
• After finishing the installation of the appliance and carrying out the electrical
connection fit the carter (fig. 5b) using the self-tapping screws and steel
washers "
N
" and making sure that the two lower teeth on the plastic base
lock the cover.
• You are advised to fit an electric locking device on the installation (see
standard installation fig. 1).
Releasing the gate should only be carried out when the motor has stopped
because of blackouts.
To release the gate use the key supplied with the appliance and turn it anti-
clockwise: details "
1
" and "
2
".
Releasing the gate
Open the access door and rotate the lever as shown in detail "
3
" fino a until it
reaches the release position.
This will release the geared motor and free the gate, which can then be opened
by pushing lightly on the gate.
The release lever may be removed and placed in its housing inside the front
access panel. This will allow the geared motor to remain in the released
position whenever the automation for as long as necessary, see detail "
4
".
Locking the gate
Carry out the previous operations in the reverse order.
Mounting the optional manual release cord (fig 8)
a) Slide out the wire cord from its sheath and insert the free end into the
hole on the release lever, point 1 fig. 8. Slide the regulating device onto
the free end and then the sheath, points 2 and 3 fig. 8.
b) Fasten down the sheath by inserting the regulating device into its seat,
points 2 and 3 fig. 8. Regulate it by as shown in 1/3 and 2/4 fig. 8a.
c) Connect the wire cord and the sheath to the handle and/or external clos-
ing device as shown in points 1 and 2 fig. 8b.
Setting the mechanical travel limits (fig. 6)
• Release the geared motor.
• Move the gate to the open position, place the mechanical stop onto the
straight arm and fasten down using the supplied screws and washers,
see figure 6 details "
4
" and "
5
".
• You may also install a mechanical stop in the closing position by following
the previous described instructions and consulting detail "
6
".
Electronic control unit for two dc motor with an incorporated encoder and
radio receiver card, which allows the memorization of
300 / 1000 user
codes
. The "rolling code" type decoder uses
433.92 MHz
(
868 MHz
on
request)
transmitters.
The motor rotation speed is electronically controlled, starting slowly and
increasing in speed; the speed is reduced as it nears the travel limit so as
to enable a controlled smooth stop.
Programming is carried out using one button and allows you to set the
system, the current sensor and the entire gate travel distance.
The intervention of the anticrush/antidrag sensor during the closing and
opening stages causes travel direction inversion.
Attention!
There is no
230 Vac
contact on any part of the
electronic card: only low voltage safety current is available. In
conformity with the electrical safety standards it is forbidden
to connect binding posts
9
and
10
directly to a circuit that
receives power greater than
30 Vac/dc
.
• Warning!
For the correct operation of the programmer
the incorporated batteries must be in good condition: the
programmer will
lose the position
of the gate in case of
blackouts when the batteries are flat and the alarm indication
will appear on the display.
Check the good working order of the batteries every six
months (see page 22 "
Battery check
").
MANUAL RELEASE MECHANISM
(fig. 7)
ELECTRICAL CONNECTION
IMPORTANT REMARKS
N
L