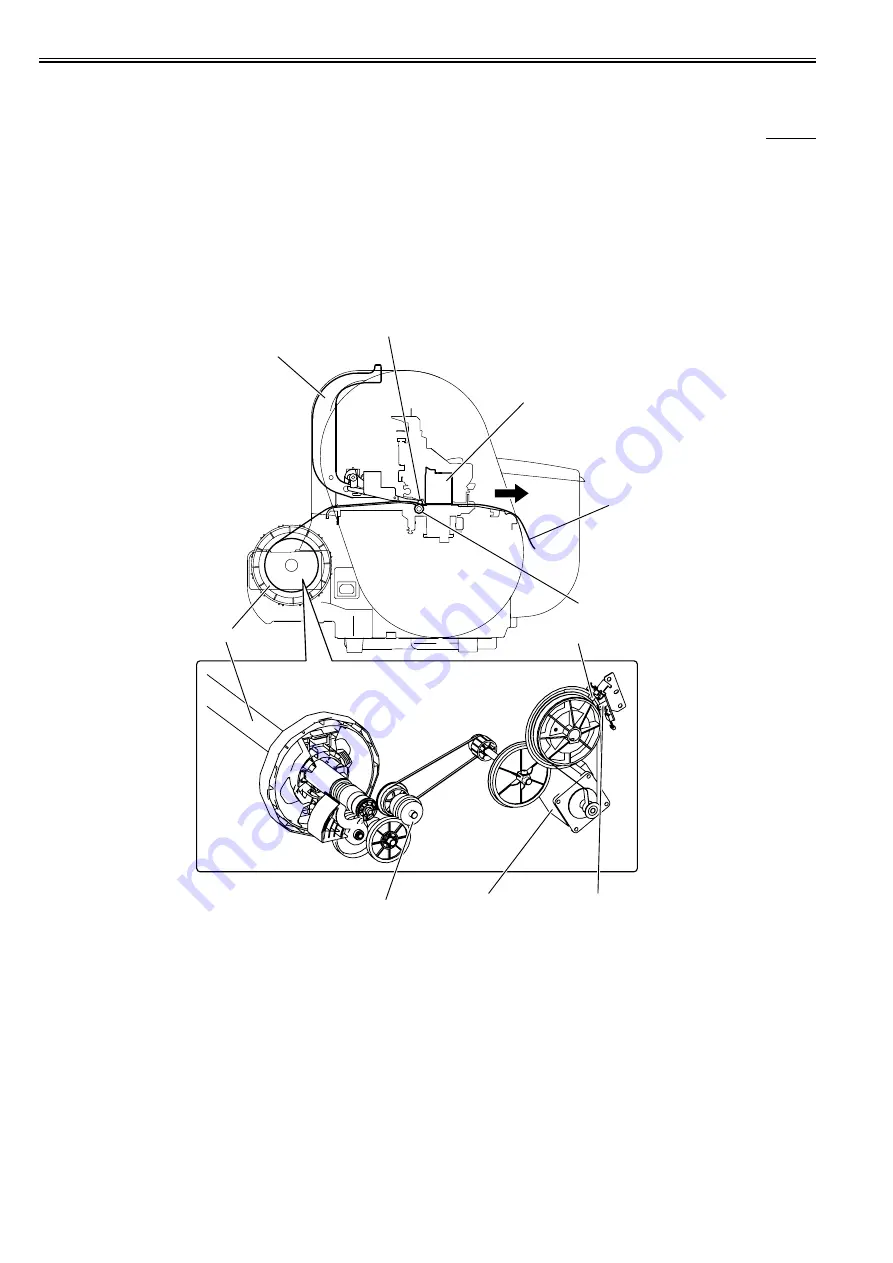
Chapter 2
2-30
2.3.3.2 Paper Path
2.3.3.2.1 Structure of Feed Roller Unit
0017-5580
a) Feed roller assembly
The feed roller assembly consists mainly of a feed roller that is driven by the feed motor, a pinch roller unit that follows up the motion of the feed roller and so on.
Paper is fed horizontally under the printhead on the carriage as it is kept level on the platen to prevent heaving.
b) Sensors
The feed roller assembly includes a feed status detection sensor and paper passage mechanical component status detection sensors.
c) Roll media rewind drive unit
The paper feed unit is provided with a roll media rewind drive to prevent paper from slacking during roll media feed. The rewind drive turns on the roll media
rewinding clutch to rewind the roll media.
The roll media rewinding clutch can be turned on only when the roll media is fed during the backward feed. The feed motor rotates the roll holder to rewind the roll
media. During the forward feed, the roll media rewinding clutch is held off.
F-2-22
Paper release lever
Pinch roller
Printhead
Roll media
Roll holder
Feed roller
Feed roller HP sensor
Feed roller encoder sensor
Feed motor
Roll media rewinding clutch
Содержание iPF720 - imagePROGRAF Color Inkjet Printer
Страница 1: ...Mar 10 2008 Service Manual iPF700 series iPF720 ...
Страница 2: ......
Страница 6: ......
Страница 11: ...Chapter 1 PRODUCT DESCRIPTION ...
Страница 12: ......
Страница 14: ......
Страница 52: ...Chapter 1 1 38 ...
Страница 53: ...Chapter 2 TECHNICAL REFERENCE ...
Страница 54: ......
Страница 98: ......
Страница 99: ...Chapter 3 INSTALLATION ...
Страница 100: ......
Страница 102: ......
Страница 106: ...Chapter 3 3 4 ...
Страница 107: ...Chapter 4 DISASSEMBLY REASSEMBLY ...
Страница 108: ......
Страница 110: ......
Страница 135: ...Chapter 5 MAINTENANCE ...
Страница 136: ......
Страница 138: ......
Страница 142: ...Chapter 5 5 4 ...
Страница 143: ...Chapter 6 TROUBLESHOOTING ...
Страница 144: ......
Страница 146: ......
Страница 165: ...Chapter 7 SERVICE MODE ...
Страница 166: ......
Страница 168: ......
Страница 190: ......
Страница 191: ...Chapter 8 ERROR CODE ...
Страница 192: ......
Страница 194: ......
Страница 203: ...Mar 10 2008 ...
Страница 204: ......