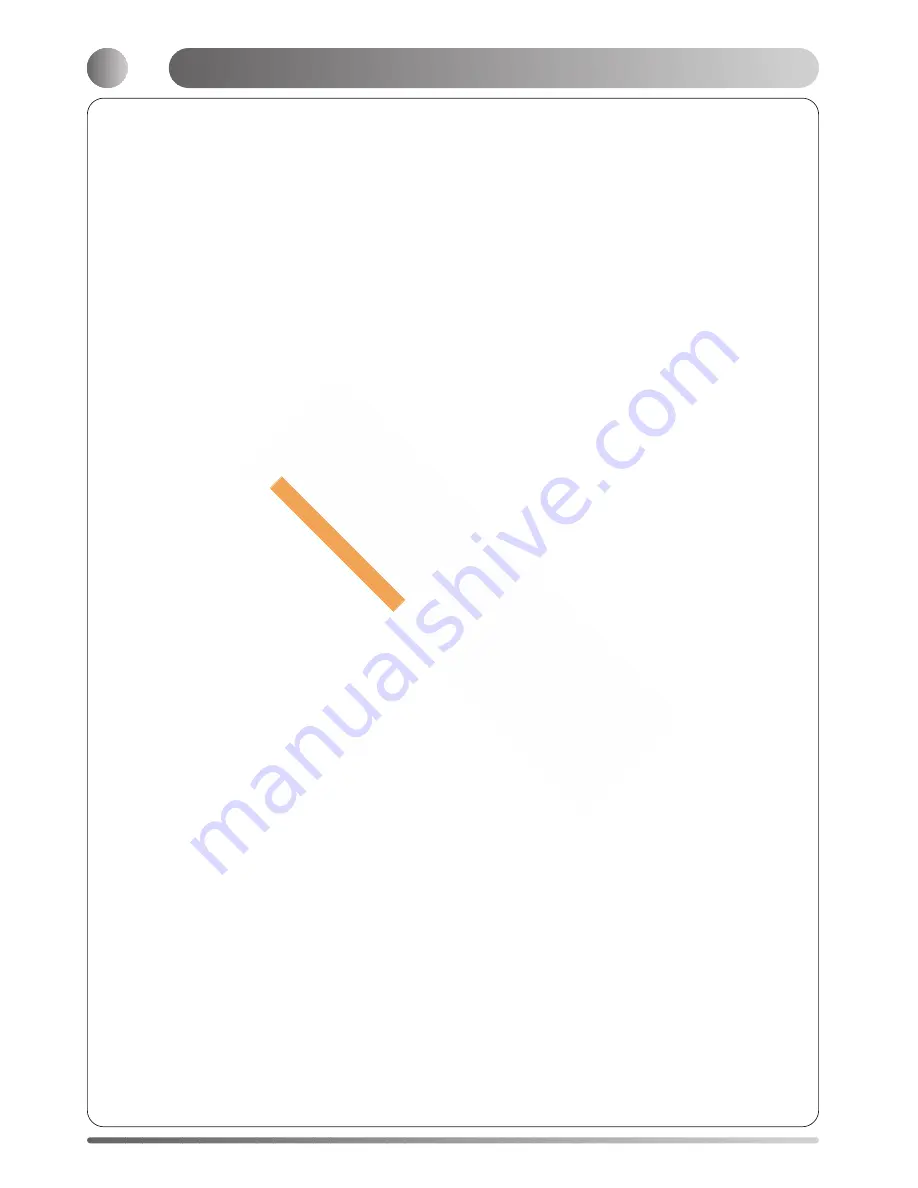
8
5
Please check that you are familiar with the installation requirements before commencing work.(section 6)
The installation accessories described in the following list are included in the boiler packaging.
- Hanging bracket
- A paper template (showing the dimensions of the boiler with 5 mm side clearances, fitting instructions and commissioning
instructions)
- Connection tails
- Screws and wall plugs
- Connection washers and filters
- Installation manual
Method of positioning the boiler on the wall.
The paper template can be used to ensure the correct positioning of kitchen cabinets etc. It also details the commissioning
instructions.
The paper template has to be fixed to the wall and used to locate the position of the hanging bracket and the centre for the flue
hole.
Drill and plug the wall and secure the hanging bracket using the screws provided. Remove the boiler from its packaging as
shown in fig. 8 and unscrew the 4 screws A and remove the casing (Fig. 9).
Place the boiler on the wall on the hanging bracket (Fig. 10).
If required, there is space for all piping to pass behind the boiler. Using Fig. 10 for reference, connect the gas and water pipes
and the valves to the base of the appliance using the tails provided. There is a 190 mm space between the valves and the wall
to make these connections.
Connecting the boiler to the system
- Push in the tabs “P” (fig. 12) on either side of the boiler and pivot the electrical box forward to gain access to the valve
connections
- Remove the yellow caps and connect the boiler to the taps using washers provided in the plastic bag.
2 x fibre washers for the C/H flow and return.
1 x rubber washer for gas connection.
Provision must be made to fill and recharge the system pressure. This can be achieved using a filling loop or other methods
approved by the local water authority.
Safety valve and condensate drains
The pressure relief valve tube is clear silicone. It should terminate below the boiler over a tundish or 22 mm pipe (see I fig 4)
which should in turn discharge safely outside the premises. Care should be taken that it does not terminate over an entrance
or window or where a discharge of heated water could endanger occupants or passers by.
The system should be carefully checked for leaks, as frequent refilling could cause premature system corrosion or
unnecessary scaling of the heat exchanger. The pipe from the siphon 12 (fig. 1) should be connected to a drain is the
conditions described in the relevant Brittish regulations.
External termination via condensate siphon
The condensate drainage pipe should have a minimum diameter of 22 mm, it should be inserted into a suitable acid resitant
pipe - e.g. plastic waste or overflow pipe (refer to BS 6798 : 2000) by at least 50mm, must have a continuous fall and
preferably be installed and terminated within the building.
Pay special attention to not bend the condensates silicone drain pipe such as the flow will be interrupted.
The discharge pipe must terminate in a suitable position:
i)
Connecting to an internal soil stack (at least 450mm above the invert of the stack). A trap giving a water seal of at least
75mm must be incorporated into the pipe run, there must also be an air break upstream of the trap.
ii)
Connecting into the waste system of the building, such as a washing machine or sink. The connection should be upstream
of the washing machine / sink (if the connection is down stream of the waste trap then an additional trap giving a minimum
water seal of 75mm and an air break must be incorporated in the pipe run as above.
iii) Terminating into a gully below the grid level but above the water level.
iv) Into a soakaway.
N
OTE
:
IF ANY CONDENSATE PIPEWORK IS TO BE INSTALLTED EXTERNALLY
,
THEN IT SHOULD BE KEPT TO A MINIMUM AND BE INSULATED WITH
A WATERPROOF INSULATION AND HAVE A CONTINUOUS FALL
The condensate flow can reach 2 litres/hour; because of the acidity of the condensate products (Ph close to 2), take care
before operation.
Fitting the Horizontal Flue
Attention ! Before starting the boiler, the siphon 12 fig. 1 must be filled with water. Before fitting the flue terminal onto
the boiler, please poor 1/4 litre of water in the exhaust pipe as shown in Fig. 11.
The instructions for the vertical and biflux (twin pipe) flue options are included with the relevant adapter kits.
The standard flue supplied with the appliance is suitable for lengths from 300 mm minimum to 720 mm maximum.
Installing the Boiler