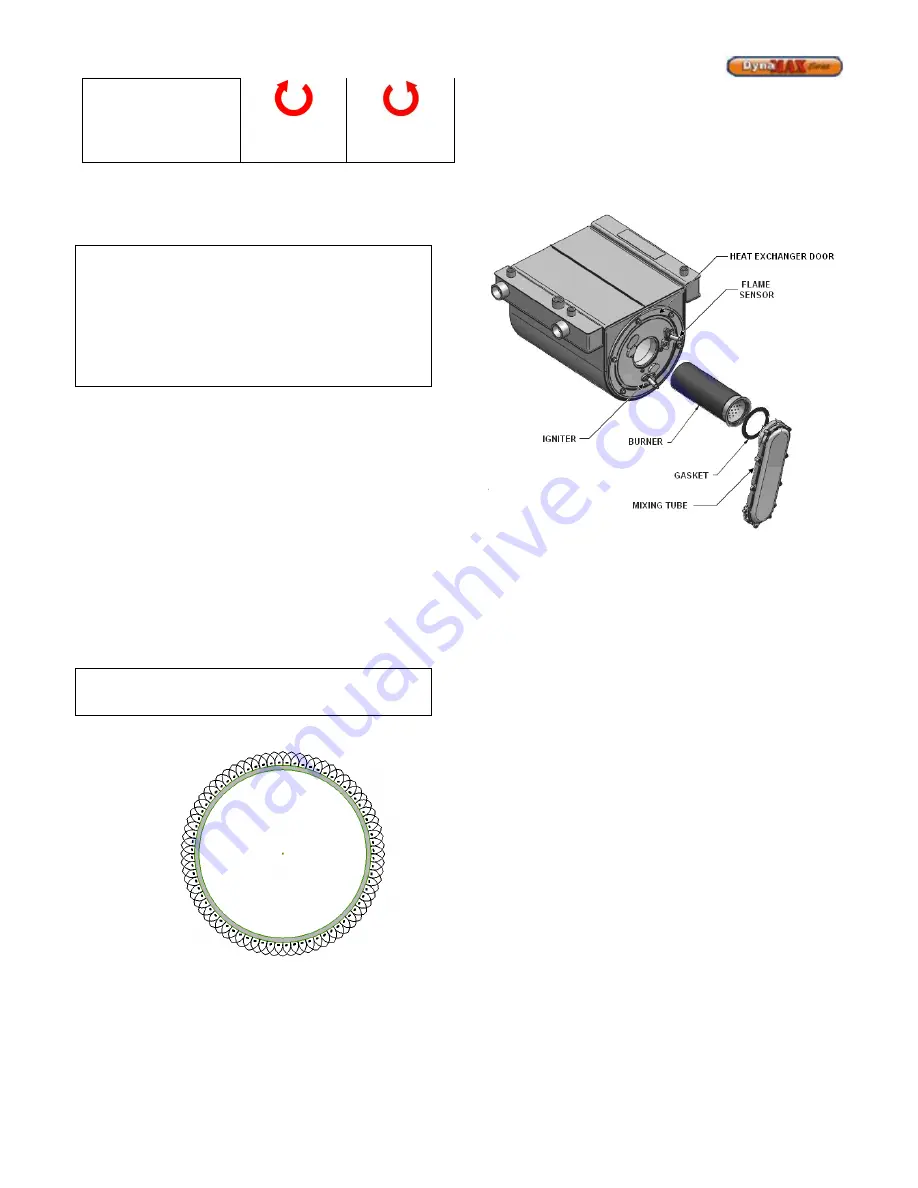
49
Low Fire
Adjustment
Clockwise
Counter-
Clock Wise
Select
Stop Test
to return to normal operation or the boiler
will return to normal operation after 5 minutes
PART 9
MAINTENANCE
CAUTION
It is important that all gas appliances be serviced by a
qualified technician trained by Camus® Hydronics. It is in
your own interest and that of safety to ensure that all local
codes, and all the “NOTES” and “WARNINGS” in this
manual are complied with. To service or adjust this
appliance, it is imperative that the serviceman utilize a
combustion analyzer to read CO
2
and CO according to
Camus® Hydronics recommendations.
Listed below are items that must be checked to ensure safe
reliable operations. Verify proper operation after servicing.
9.1
EXAMINE THE VENTING SYSTEM
Examine the venting system at least once a year. Check
more often in the first year to determine inspection interval.
Check all joints and pipe connections for tightness, corrosion
or deterioration. Flush the condensate drain hose with water
to clean. Clean screens in the venting air inlet system as
required. Have the entire system, including the venting
system, periodically inspected by a qualified service agency.
9.2
VISUALLY CHECK MAIN BURNER FLAMES
At each start up after long shutdown periods or at least every
six months. A burner view port is located on the combustion
chamber front door.
CAUTION
The area around the burner view port is hot and direct
contact could result in burns
Figure 31: Normal Burner Flame Profile (short dense
and blue)
•
Normal Flame
: A normal flame at 100% of burner input
is blue, with a well-defined flame and no flame lifting.
•
Yellow Tip
: Yellow tipping can be caused by blockage
or partial obstruction of air flow to the burner.
•
Yellow Flames
: Yellow flames can be caused by
blockage of primary air flow to the burner or excessive
gas input. This condition
MUST
be corrected
immediately.
If improper flame is observed, examine the venting system;
ensure proper gas supply and adequate supply of
combustion and ventilation air.
9.3
CLEANING BOILER HEAT EXCHANGER
Figure 32: Heat Exchanger & Burner Assembly
1) Shut down boiler:
a) Turn the main power off to the boiler
b) Shut off gas supply at the main manual valve in
the gas piping of the main appliance
c) DO NOT drain the boiler unless it will be exposed
to freezing temperatures. If using antifreeze fluid
in the heat exchanger,
DO NOT
drain.
2) Allow time for the boiler to cool to room temperature if it
has been firing.
3)
Wall Hung:
Remove both the stainless steel upper
jacket and the lower sheetmetal jacket.
Floor Mount:
Remove front stainless steel panel.
4) Remove igniter and flame sensor electrodes. If
necessary, clean with steel wool.
DO NOT
use
sandpaper.
5) Remove the fan/ mixing tube assembly from the heat
exchanger door.
6) Remove burner.
7) Examine burner and clean if required as per 9.7.1.
8) Examine heat exchanger surfaces to determine if
cleaning is required. If cleaning is required remove the
(6) nuts fastening the heat exchanger flange from the
heat exchanger.
9) Disconnect the condensate hose from the heat
exchanger and connect a 5/8” diameter hose (field
supplied) from the bottom of the heat exchanger to a
drain
Содержание DynaMax DMH201
Страница 2: ......
Страница 11: ...7 Figure 5 DynaMax HS Wall Hung Service Clearances Figure 6 DynaMax HS Floor Mount Service Clearances...
Страница 70: ...62 PART 14 EXPLODED VIEW PARTS LIST DYNAMAX HS WALL HUNG 10 May be located outside cabinet...
Страница 71: ...63 DYNAMAX HS FLOOR MOUNT 10 May be located outside cabinet...
Страница 77: ...69 11 6 Front Strut 14 8037 X X Not shown in Exploded View Part Recommended spare parts...
Страница 78: ...70 PART 15 ELECTRICAL DIAGRAMS 15 1 DM 200 299 INTERNAL WIRING DIAGRAM...
Страница 79: ...71 15 2 DM 399 800 INTERNAL WIRING DIAGRAM...
Страница 80: ...72...