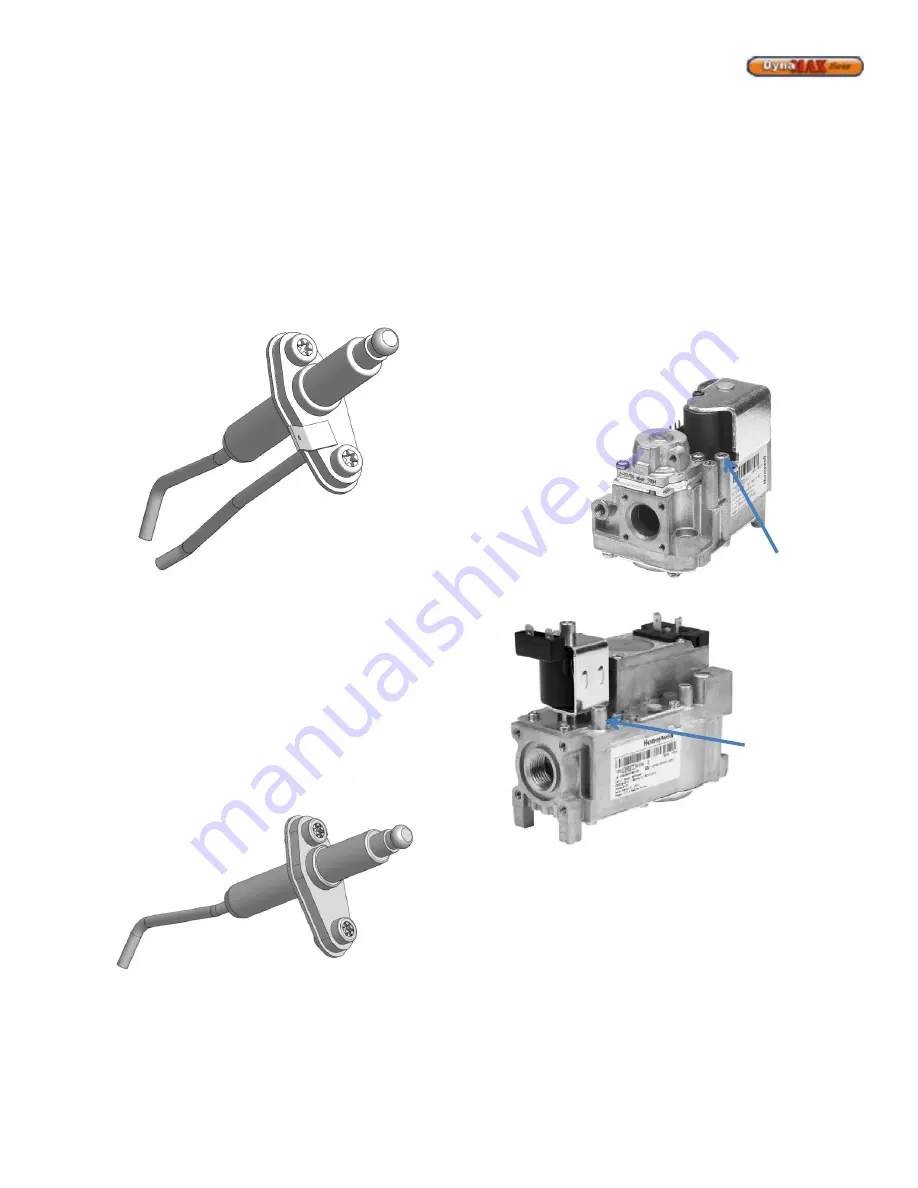
37
PART 7
COMPONENTS
7.1 DIRECT SPARK IGNITER
The direct spark igniter is inserted directly through the
combustion chamber front door and held in place by two torx-
20 screws which must be torqued to 1 ft-lb (1.4 Nm). Care
must be taken when removing and/or installing the igniter.
Always remove the igniter prior to removing the fan assembly
for inspection of the burner and heat exchanger.
When replacing the igniter do not over tighten the mounting
screws. Torque the screws to no more than 10 in-lb.
Figure 27: Direct Spark Igniter
During a trial for ignition sequence a properly operating igniter
will generate a continuous spark with a 13/64
” (5.2mm) spark
gap. It is recommended to clean the direct spark igniter using
steel wool as required.
DO NOT
use sandpaper or grit-cloth
since this will contaminate the metal surface.
7.2
FLAME SENSOR
The flame sensor is inserted directly through the combustion
chamber front door and is screwed into the combustion
chamber front door by torx-20 screws. Care must be taken,
when installing the flame sensor, to align it perpendicular to
the fan flange and parallel to the burner tube and not to over
tighten.
Figure 28: Flame Sensor
The ignition module relies on the flame sensor to provide a
flame rectification signal. Oxide deposits, improper placement
or damaged ceramic insulator will result in insufficient signal
leading to ignition module lock out. For proper operation
minimum 0.8Vdc must be fed back to the module. Oxide
deposit on the sensor rod must be removed with steel-wool.
DO NOT
use sand-paper or grit-cloth since this will
contaminate the metal surface.
7.3 COMBUSTION AIR FAN
DynaMax HS uses a modulating air fan to provide combustible
air/gas mix to the burner and push the products of combustion
through the heat exchanger and venting system. The fan
assembly consists of a sealed housing and fan wheel
constructed from spark resistant cast aluminum. The fan is
operated by a fully enclosed 120 VAC, Single-Phase EC/DC
electric motor. The fan housing and motor assembly is fully
sealed and SHOULD NOT be field serviced. The power draw
of the motor is proportional to the modulated gas input rate of
the appliance.
7.4 GAS VALVE
Figure 29: DynaMax HS 200 -250/260 Gas Valve
Figure 30: DynaMax HS 299 -399 Gas Valve
The gas valve supplied with the DynaMax HS boiler is a
combined valve/venturi assembly. A servo pressure regulator
is incorporated into the gas valve to provide stable gas supply.
Pressure taps are provided to check inlet and outlet gas
pressures. An internal fine mesh screen is incorporated in the
inlet of the gas valve to prevent debris from entering the
combustion chamber. Gas valves are factory set at low and
high
fire
and
modulates
to
maintain
combustion
characteristics across the full operating range.
7.5 OUTER JACKET
The outer jacket assembly is constructed from mirror finish
stainless steel. This ensures a long life for the jacket
assembly, with full integrity
Inlet gas
pressure
Inlet gas
pressure
Содержание DynaMax DMH201
Страница 2: ......
Страница 11: ...7 Figure 5 DynaMax HS Wall Hung Service Clearances Figure 6 DynaMax HS Floor Mount Service Clearances...
Страница 70: ...62 PART 14 EXPLODED VIEW PARTS LIST DYNAMAX HS WALL HUNG 10 May be located outside cabinet...
Страница 71: ...63 DYNAMAX HS FLOOR MOUNT 10 May be located outside cabinet...
Страница 77: ...69 11 6 Front Strut 14 8037 X X Not shown in Exploded View Part Recommended spare parts...
Страница 78: ...70 PART 15 ELECTRICAL DIAGRAMS 15 1 DM 200 299 INTERNAL WIRING DIAGRAM...
Страница 79: ...71 15 2 DM 399 800 INTERNAL WIRING DIAGRAM...
Страница 80: ...72...