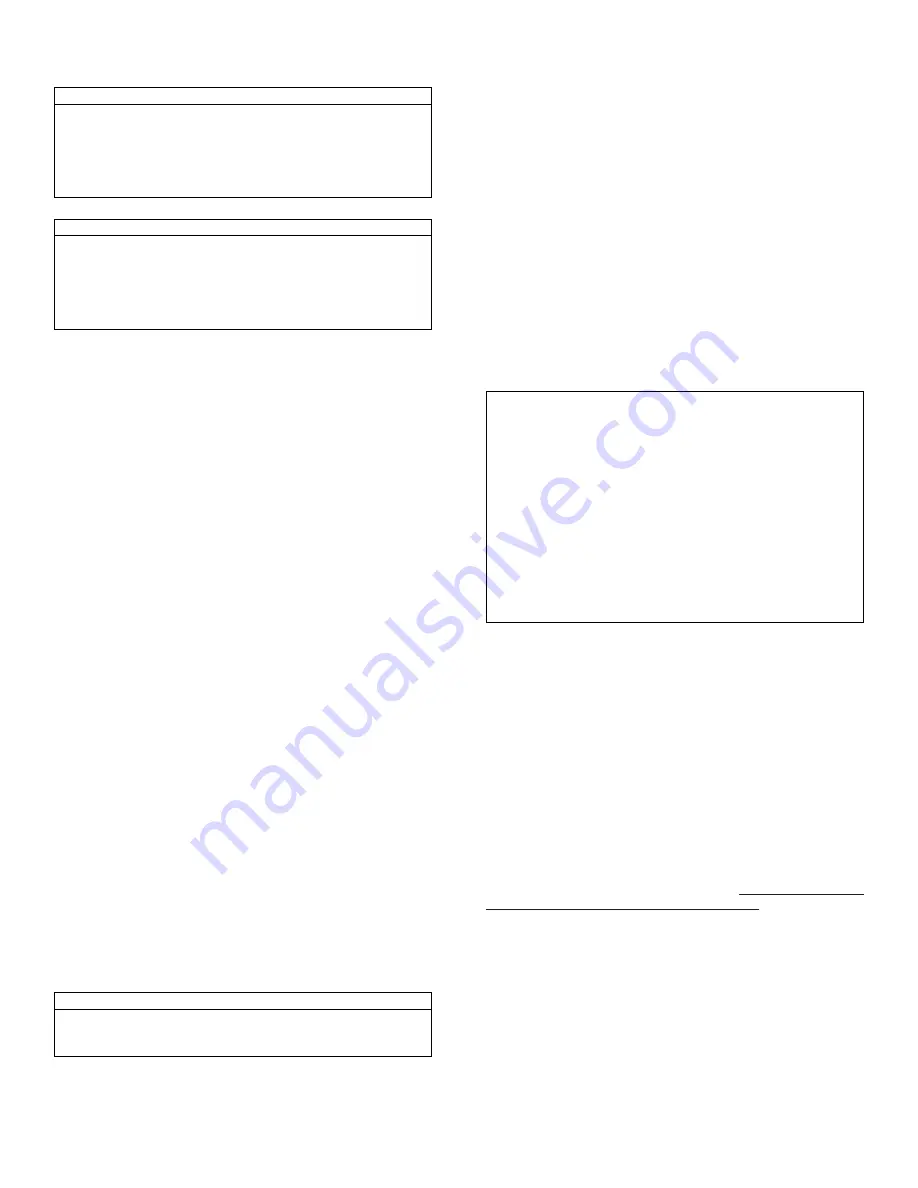
64
PART 11 INSTALLATIONS
WARNING
Before starting the boiler, smell near the floor and around
the boiler for any gas odours or any unusual odour. Remove
the stainless steel jacket and smell the interior of the boiler.
If there is any sign of a gas leak, do not proceed with
startup. Repair all the leaks before attempting to start the
boiler
WARNING
Propane boilers ONLY – Your local propane supplier adds an
odorant to the propane gas to allow for propane gas leak
detection. In some cases, the added odorant can fade and
the gas may not give off any noticeable odour. Before startup
have the local propane supplier check for the correct odorant
level in the gas.
11.1 CHECKING THE INSTALLATION
•
Inspect the connections for water, gas and electricity.
•
Inlet gas pressure must be a minimum of 7” W.C. for natural
gas and 11” W.C. for propane.
•
With the boiler off, open the main gas supply valve and vent
the trapped air from the piping leading to the boiler. Confirm
that all gas connections to the heater are tight and that there
are no missing test plugs.
Refer to Section 8.3 Gas Valve Adjustment Procedure of the
manual for recommendations on setting combustion
characteristics
11.2 CHECKING THE INSTALLTION
•
Check the boiler wiring to see that it agrees with the
wiring diagram supplied.
•
Confirm that all terminal strips and field connections
are identified.
•
With the boiler running, check for flue gas leaks along
the inner cabinet joints and around the flue outlet.
•
Repair any leaks prior to proceeding to the next step.
•
At the factory, adjustments were made to achieve
proper input and acceptable burner performance at full
input and at minimum input.
11.3 INSPECT & RECHARGE CONDENSATE
COLLECTION & NEUTRALIZING RESERVOIR
1) Inspect the ‘P’ trap and condensate reservoir in the
Dynaforce®, making sure the collection box is intact.
2) Remove screws holding lid on to condensate collection box.
Remove lid from the condensate collection box.
3) Fill with fresh water until the water begins to flow out of
drain.
4) Re-install the lid and hold-down screws on the condensate
collection box.
5) Inspect the condensate neutralizer supplied on site and
confirm that it contains sufficient calcium carbonate to
operate effectively to neutralize condensate to required
level.
6) Check pH level of condensate.
WARNING
The condensate collection box must be filled with water to
prevent flue gas emissions from escaping during boiler
operation.
11.4 HEATING BOILER INSTALLATIONS
The appliance MUST always be installed in a
primary/secondary reverse return piping system for proper
operation.
Before beginning the installation, consult local codes
for specific plumbing requirements. The installation should
provide unions and valves at the inlet and outlet of the appliance
so it can be isolated for service. An air separation device must
be supplied in the installation piping to eliminate trapped air in
the system. Locate a system air vent at the highest point in the
system. The system must also have a properly sized expansion
tank installed. Typically, an air charged diaphragm-type
expansion tank is used. The expansion tank must be installed
close to the boiler and on the suction side of the system pump
(appliance Inlet) to ensure proper operation. Caution: This
appliance should not be operated at less than 30 PSIG. Water
piping must be supported by suitable hangers or floor stands,
NOT by the appliance. Pipe systems will be subject to
considerable expansion and contraction. Pipe supports could
allow the pipe to slide resulting in noise transmitted into the
system. Padding is recommended. The boiler pressure relief
valve must be piped to a suitable floor drain. See Section 4.10.
CAUTION
1) A leak in a boiler “System” will cause the “System” to
intake fresh water constantly, which may cause the
tubes to accumulate a lime/scale build up. This will be a
NON-WARRANTABLE FAILURE.
2) If boiler pumps are not operated when treated water is
introduced, a corrosion cell may be created in the
boilers leading to a failure which is not covered by
warranty.
3) Target water quality of treated water to be stable and
neutral with regards to corrosive/scaling properties.
Damage to or failure of the heat exchanger as a result
of scaling or corrosive water quality is not covered by
warranty.
11.5 WATER CONNECTIONS
All models have groove locked inlet and outlet stainless steel
connections. Pipe size must be in accordance with Table 3 and,
between supply and return lines, must not exceed 80 feet of
equivalent length. Any reduction in recommended pipe size may
decrease flow resulting in high water temperatures, boiler noise,
flashing to steam and non-warrantable heat exchanger damage.
11.6 PIPING LENGTHS
The appliance circulator provides the water flow from the
primary boiler piping, through the boiler and back to the primary
system. Pipe diameter and length are critical to ensure proper
flow through the boiler.
The secondary loop piping to and from the appliance must have
a fully ported ball valve installed in both the inlet and outlet side
piping and will be used for isolation only.
The ball valves must
be the same diameter as the installed piping
. If flow control is
required, other means of flow control such as globe valve or flow
setter should be used.
11.7 INTERMITTENT PUMP OPERATION
An intermittent pump operation signal is standard and can be
used to operate a separate pump contactor. A 1/6 hp pump
delay relay is standard, and a 1 hp pump delay relay is available.
When utilizing this feature, the boiler’s integral circulating pump
will cycle on at each call for heat, before the burner fires. The
pump will continue to operate while the burner is firing. The
pump will run for a post-pump period after the temperature set
Содержание DRW1000
Страница 2: ...99 0171 REV 0 9...
Страница 35: ...35...
Страница 48: ...48...
Страница 67: ...67 PART 12 EXPLODED VIEW 19 1 2 3 4 5 6 7 8 9 10 11 12 13 14 15 16 17 18 20...
Страница 68: ...68 21 22 23 24 26 35 34 33 32 31 30 29 28 27 25 36 37 38 39 40 42 43 56...
Страница 75: ...75 PART 13 ELECTRICAL DIAGRAMS...
Страница 76: ...76...
Страница 77: ...77...
Страница 78: ...78...
Страница 79: ...79...