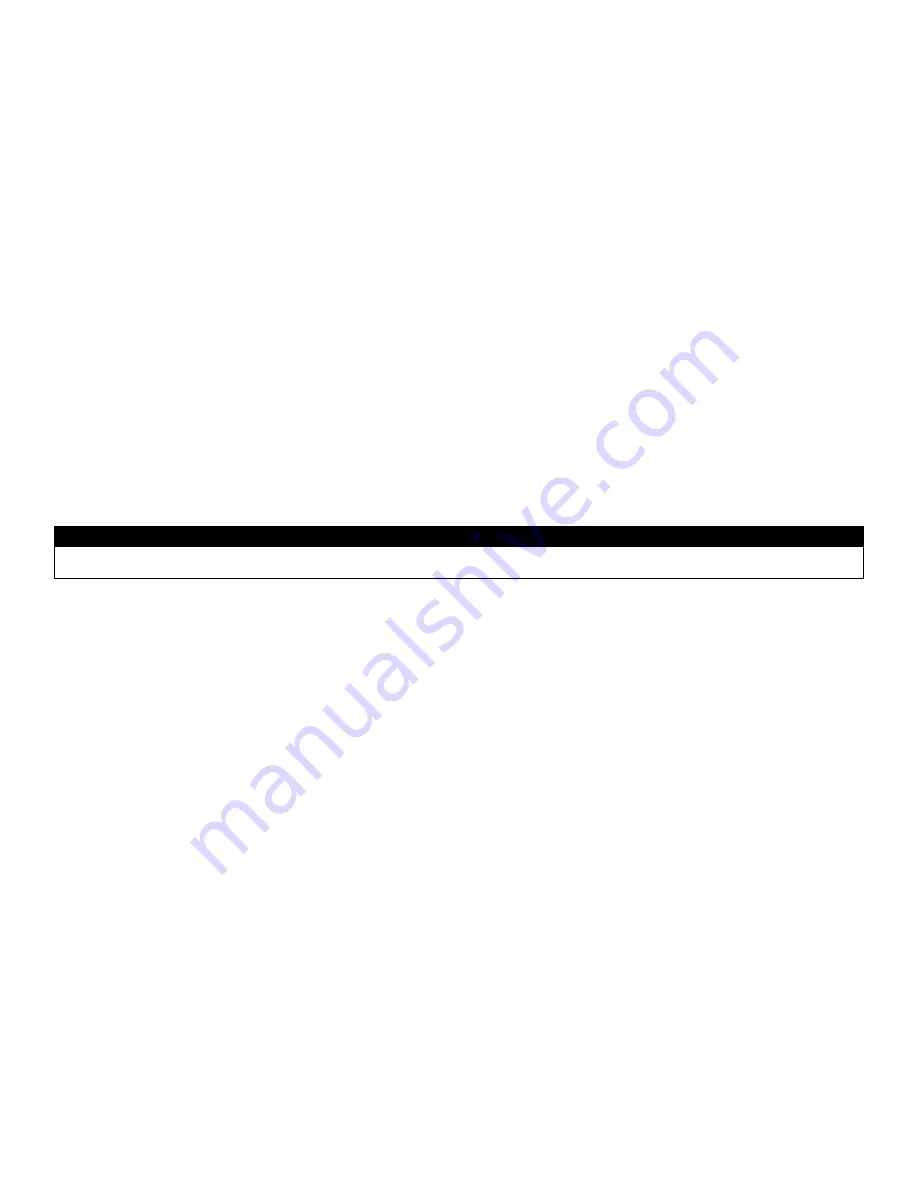
75
10.8
RE-INSTALL HEAT EXCHANGER
Carefully reinstall the heat exchanger if removed from the appliance
Cycle unit and check for proper operation
Replace the top cover
10.9
COMBUSTION AIR FAN
Combustion air fan should be checked every 6 months. Clean the inlet screen and damper plate as required when installed in a dust or
dirt contaminated location. The motor and bearings on the combustion air fan are sealed and permanently lubricated requiring no addition
of oil or lubricants.
10.10
COMBUSTION AND VENTILATION AIR
Check frequently to be sure that the flow of combustion and ventilation air to the appliance is not obstructed. Combustion and ventilation
air must be provided to the mechanical room with openings sized per the requirements of the B149 or National Fuel Gas Code. The
optional outdoor air kit brings combustion air from the outdoors directly to the appliance.
10.11
CONTROL CIRCUIT VOLTAGE
This appliance uses a transformer to supply a low voltage control circuit. The voltage on the secondary side should be 24 to 28VAC
when measured with a voltmeter. A secondary voltage of 21VAC or less supplied to 24VAC components may cause operational problems.
A 4A circuit breaker is provided on the secondary side of the transformer. A tripped circuit breaker indicates a short in the 24VAC controls
and must be corrected.
10.12
COMBUSTIBLE MATERIALS
CAUTION
Keep appliance clear from combustible materials; do not store
GASOLINE
and other flammable vapors and liquids in the proximity
of the appliance.
10.13
FREEZE PROTECTION
Installations are not recommended in areas where the danger of freezing exists. Proper freeze protection must be provided for appliances
installed outdoors, in unheated mechanical rooms or where temperatures may drop to the freezing point or lower. If freeze protection is
not provided for the system, a low ambient temperature alarm is recommended for the mechanical room. Damage to the appliance by
freezing is non-warrantable.
Location
- Heating boilers, hot water supply boilers or water heaters must be located in a room having a temperature of at least 50ºF
(10ºC)
Caution
- A mechanical room operating under a negative pressure may experience a downdraft in the flue of an appliance that is
not firing. The cold outside air may be pulled down the flue and freeze a heat exchanger. This condition must be corrected to provide
adequate freeze protection.
Freeze protection for the appliance using an indirect coil can be provided by using hydronic system antifreeze. Follow the
manufacturer’s instructions.
DO NOT
use undiluted or automotive type antifreeze.
Shut-down and draining
- If for any reason, the unit is to be shut off where danger of freezing exists, the following precautionary
measures must be taken:
o
Shut off gas supply
o
Shut off water supply
o
Shut off electrical supply
o
Drain the heat exchanger completely
o
Ensure the pump and connecting piping are fully drained
10.14
FREEZE PROTECTION FOR A HEATING BOILER SYSTEM (Optional)
Use only properly diluted inhibited glycol antifreeze designed for hydronic systems.
Follow the instructions from the antifreeze manufacturer. Quantity of antifreeze required is based on total system volume including
expansion tank volume.
Antifreeze is denser than water and changes the viscosity of the system. The addition of antifreeze will decrease heat transfer and
increase frictional loss in the boiler and related piping. Where antifreeze has been used, to maintain the temperature rise across the
appliance confirm that the recommended GPM for pure water has been increased by 15% and the head loss by 20%.
Local codes may require a back flow preventer or actual disconnect from city water supply when antifreeze is added to the system.
When filling or topping-up the system with water mixed with the antifreeze always used distilled or RO (reverse osmosis) water. This
will prevent the reaction of the water with antifreeze which can create sludge.
Содержание ADVANTUS AVH 1000
Страница 2: ......
Страница 3: ......
Страница 38: ...31 Figure 23 Recommended Piping with Reverse Return and Variable Primary Flow...
Страница 70: ...63 Figure 44 Typical Gas Train Models AV1000 3000 Figure 45 Typical Gas Train Models AV3500 4000...
Страница 88: ...81 PART 12 EXPLODED VIEW Figure A...
Страница 89: ...82 Figure B FAN BURNER ASSEMBLY AV500 600 some items may not be as shown...
Страница 90: ...83 Figure C FAN BURNER ASSEMBLY AV800 4000 some items may not be as shown...
Страница 91: ...84 Figure D Figure E...
Страница 92: ...85 Figure F Figure G...
Страница 93: ...86 Figure H CONTROL BOARD ASSEMBLY...
Страница 100: ...93 PART 13 ELECTRICAL DIAGRAMS...
Страница 101: ...94...
Страница 102: ...95...