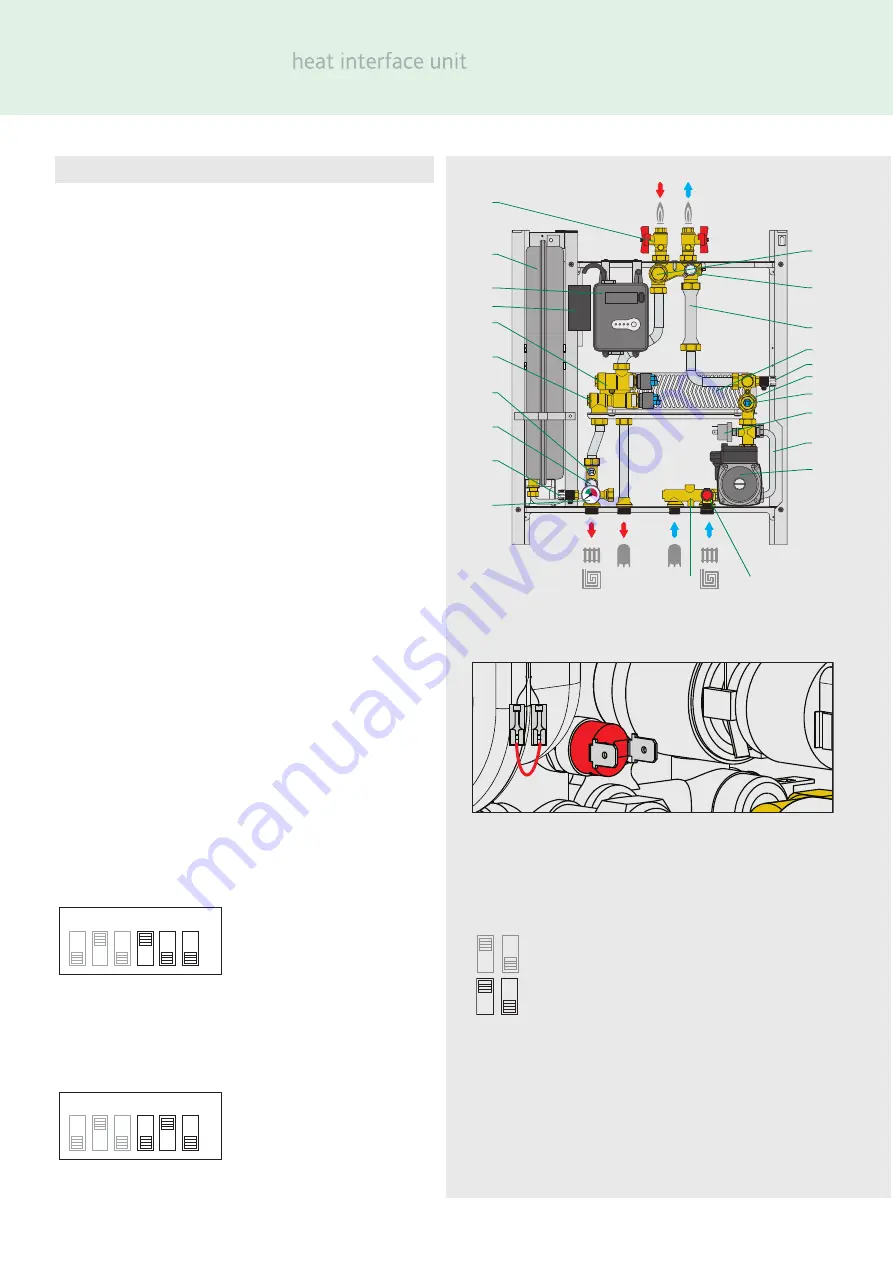
SATK40 & Procyl
®
8
Components - SATK40103
Item Component
1
Frame
2
Expansion vessel
3
Electronic control unit
4
Primary modulating control valve
5
Three port diverting valve
6
Plate heat exchanger (DHW + space heating)
7
Safety relief valve - 3 bar
9
Drain cock
12
Heat meter spool piece - replaced by heat meter when fitted
14
Heating flow temperature sensor
15
Pump
16
Pump safety bypass
18
DP switch
19
Strainer (heating circuit)
22
Primary filter and heat meter probe pocket
23
Heating return temperature sensor
24
Primary isolation valve
25
Probe
26
Pressure gauge
27
Electric connection box
26
Filling loop double check valve
*
27
Filling loop
*
28
Filling loop isolation valve
*
29
Room controller
*
(not supplied)
*
Not shown on Components illustration
Functional characteristics
Heating range:
LOW temperature setting 25 to 45˚C.
MEDIUM/HIGH temperature setting 50 to 75˚C
Optional functions
Heating cycle:
modulating temperature regulation with
compensated set point floor slab heating
function.
Factory settings
SATK 40103 HIUs are factory set to support
MEDIUM
/
HIGH
temperature heating (50 to 75˚C) with the dip switches set as
shown.
To modify the factory settings and enable the HIU to support
LOW
temperature systems (25 to 45˚C) proceed as follows;
1
Switch off the electricity power supply to the HIU
2
Set the switches 2 and 3 with the ON-OFF setting
3 Remove the safety thermostat jumper cable and
connect the cables to the thermostat.
4
Switch on the electricity power supply to the HIU.
Factory settings
Factory set - DO NOT CHANGE
May be switched to activate optional functions
Switch 1:
modulating temperature regulation
with compensated set point
Switch 2-3: change setting
ON
1
2
3
5
6
4
1
0
2
3
4
ON DHW CH FAULT
RESET
1
2
1
20
11
5
28
14
15
2
24
19
4
2
3
16
17
23
22
8
2
12
18
21
ON
1
2
3
5
6
4