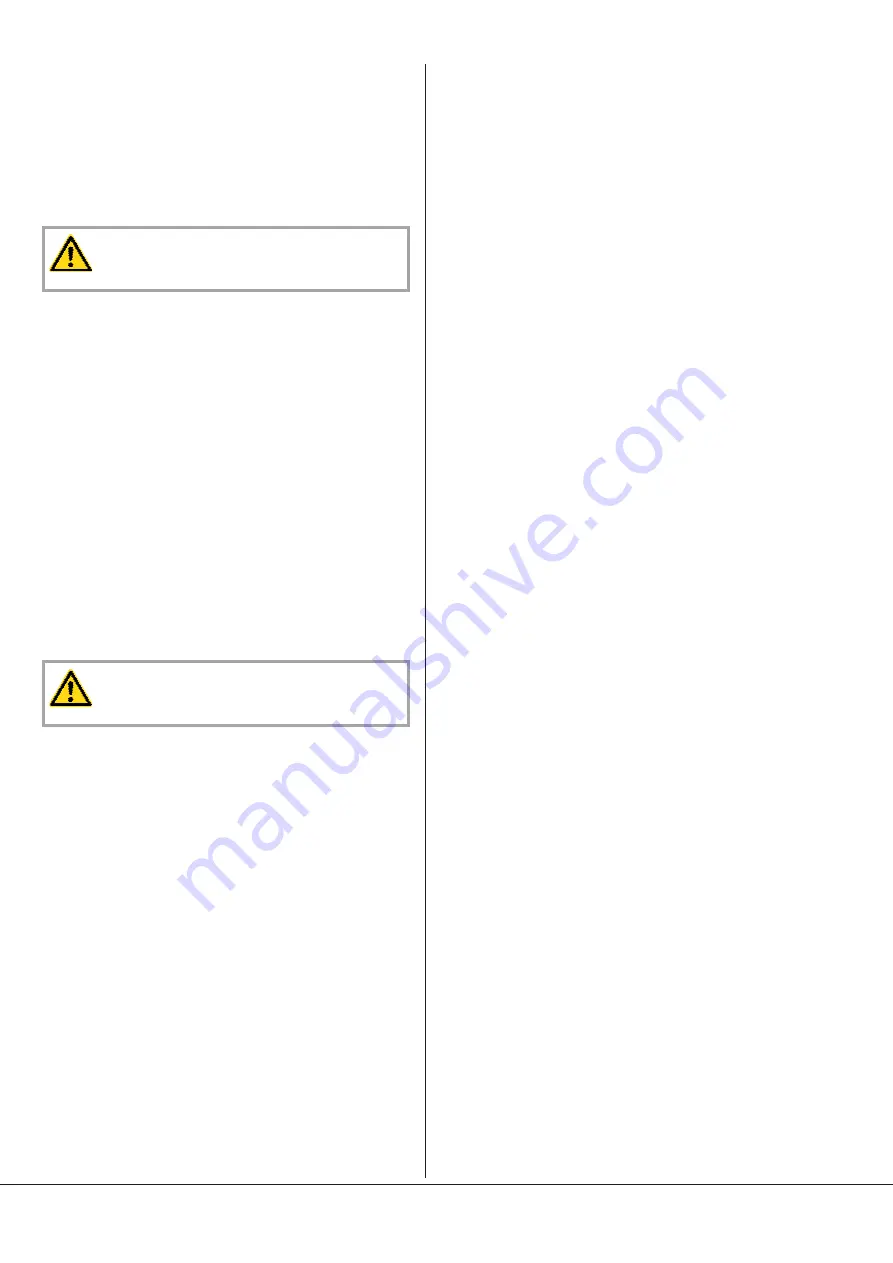
u
If necessary, drain the cooling water with the help of
compressed air to prevent any risk of frost or corrosion
NOTE
: When the vacuum system has not been in operation for a few
days or when a sticky substance has been sucked, it is possible that the
two screw rotors of the NS (DP) vacuum pump will stick to each other.
Screw open the access cover to the screw rotors. Loosen the rotors
from each other with the help of an Allen key by turning them in clock-
wise direction by hand.
Start-up of the vacuum system
WARNING
The vacuum system may be destroyed if low on operating material!
l
Check the gear oil level on the vacuum pumps (oil sight glass), see
also relevant operating instructions!
l
Fill or top up with gear oil as necessary.
l
Inlet and delivery side of vacuum system are correctly piped
l
Inlet and delivery water of vacuum system are correctly piped
l
Compressed air is available for the valve controls
l
Supply voltage is switched on
l
The vacuum system is switched on by the LCD or interface box.
Monitoring equipment
The vacuum system drive motors are safeguarded by a motor protec-
tion circuit. If an overload occurs the vacuum system is shut down.
For DP pumps: the manually set thermical relays shut down the circuit
when alarm occurs. It needs to be reloaded in the electrical box for re-
start. The current sensor and the temperature motor sensor shut down
the power supply of the pumping group when alarm occurs.
For MB pumps: the manually set thermical relays shut down all the MB
pumps when alarm occurs. It needs to be reloaded in the electrical box
for restart. The current sensor, the temperature sensor and the fre-
quency inverter shut down all the MB pumps when alarm occurs.
WARNING
Risk of vacuum system deterioration by excessing temperature!
Switching the vacuum system on/ off
First start-up of the vacuum system
l
In REMOTE mode, the start/ stop drive of the vacuum system
passes through the main machine interface of the vacuum system
(the one connected to TOOL).
l
In LOCAL mode, the start/ stop drive of the COMBI COBRA DS is
done independently.
l
Make sure that the “Necessary installation instructions” are
followed
l
Make sure that the cooling water flow is set correctly
–
The cooling water flow is factory set on 29 l/min and can be
adjusted at the regulating cock CWV 1 and CWV 2. This water
circuit is used to cool the motor of the DP and MB vacuum pumps
and the cylinder covers A- and B-side of the MB vacuum pump. It
cools also the cylinder and cylinder endplate B-side when
temperature of cooling liquid is above 50°C.
l
Make sure that the nitrogen flow is set correctly
–
Nitrogen flow injected in the middle hole (9) is preset at 20 l/min
and can be adjusted with valve DGR 1. Nitrogen flow injected in
the hole on cylinder endplate side (8) is preset at 40 l/min and can
be adjusted with valve DGR 2.
l
Switch on the vacuum system
l
Make sure that the vacuum system does not leak
Switching the vacuum system off
l
In REMOTE mode, the start/ stop drive of the vacuum system
passes through the main machine interface of the vacuum system
(the one connected to TOOL).
l
in LOCAL mode, the start/ stop drive of the COMBI COBRA DS is
done independently.
If the vacuum system is equipped with a solenoid gate valve at the in-
take:
u
Close the solenoid gate valve
l
Switch off the vacuum system
l
Shut off the nitrogen supply
l
Shut off the cooling water supply
If the vacuum system is equipped with a solenoid gate valve (customer
option) in the cooling water circuit:
u
Close the solenoid gate valve
l
Make sure that the vacuum system is currentless
Installation and start-up
COBRA DS 8163 A
Page 22
0870772605
Содержание COBRA DS 8163 A
Страница 34: ......